Sputtering targets are manufactured using a variety of processes tailored to the material properties and intended applications. Common methods include classical and vacuum hot-pressing, cold-pressing and sintering, and vacuum melting and casting. Advanced techniques are employed to achieve fine grain structures and precise shapes, ensuring high-quality targets for applications like thin-film deposition. Silicon sputtering targets, for example, can be produced through electroplating, sputtering, and vapor deposition. The choice of manufacturing process depends on the material's characteristics and the desired performance of the sputtering target in its end-use environment.
Key Points Explained:
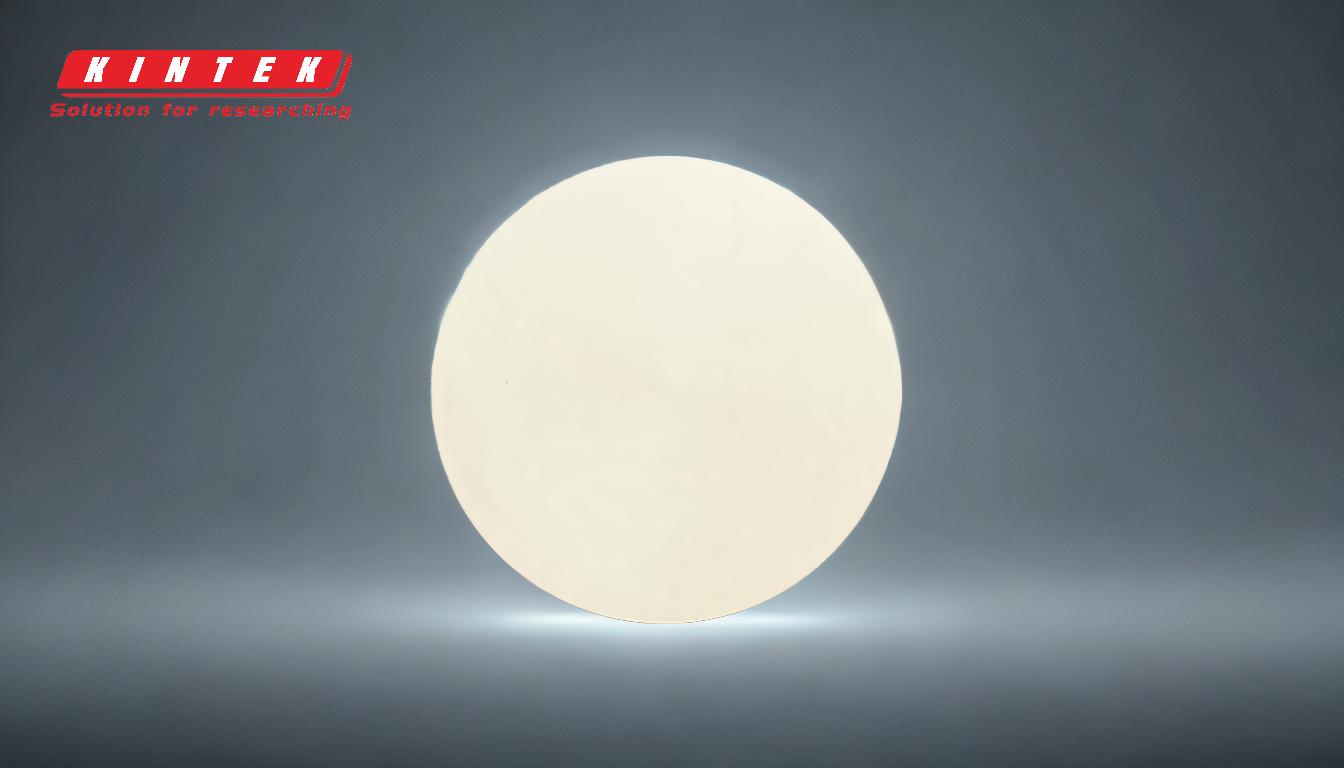
-
Common Manufacturing Processes:
- Classical and Vacuum Hot-Pressing: This method involves applying heat and pressure to the target material in a controlled environment. It is suitable for materials that require high density and uniformity.
- Cold-Pressing and Sintering: In this process, the material is pressed at room temperature and then sintered at high temperatures to achieve the desired density and mechanical properties.
- Vacuum Melting and Casting: This technique involves melting the material in a vacuum to prevent contamination and then casting it into the desired shape. It is particularly useful for materials that need to be free from impurities.
-
Advanced Manufacturing Methods:
- Fine Grain Structures: Advanced methods are used to produce sputtering targets with very fine grain structures, which are essential for achieving high-quality thin films. These methods ensure that the targets have uniform properties and can be manufactured in nearly any shape or size.
- Broad Portfolio of Materials: Advanced manufacturing leverages a wide range of materials to create targets that meet specific application requirements. This flexibility allows for the production of targets with tailored properties.
-
Silicon Sputtering Targets:
- Electroplating: This process involves depositing a layer of silicon onto a substrate using an electric current. It is used to create thin, uniform layers of silicon for sputtering targets.
- Sputtering: In this method, silicon atoms are ejected from a target material and deposited onto a substrate. It is a common technique for producing high-purity silicon targets.
- Vapor Deposition: This process involves the deposition of silicon vapor onto a substrate to form a thin film. It is used to create targets with precise thickness and uniformity.
-
Application-Specific Manufacturing:
- Material Properties: The choice of manufacturing process depends on the properties of the sputtering target material, such as its melting point, density, and mechanical strength.
- End-Use Requirements: The intended application of the sputtering target also influences the manufacturing process. For example, targets used in semiconductor manufacturing may require higher purity and finer grain structures than those used in other industries.
-
Quality Control and Precision:
- Uniformity and Density: Ensuring that the sputtering target has uniform density and grain structure is crucial for achieving consistent performance in thin-film deposition.
- Contamination Prevention: Manufacturing processes that involve vacuum environments, such as vacuum melting and casting, help prevent contamination and ensure the purity of the target material.
By understanding these key points, a purchaser can make informed decisions about the type of sputtering target that best meets their needs, considering both the material properties and the intended application.
Summary Table:
Manufacturing Process | Description |
---|---|
Classical and Vacuum Hot-Pressing | Applies heat and pressure in a controlled environment for high density and uniformity. |
Cold-Pressing and Sintering | Pressed at room temperature, then sintered at high temperatures for density and strength. |
Vacuum Melting and Casting | Melts material in a vacuum to prevent contamination, then casts into desired shapes. |
Electroplating (Silicon Targets) | Deposits silicon onto a substrate using an electric current for thin, uniform layers. |
Sputtering (Silicon Targets) | Ejects silicon atoms from a target material to deposit onto a substrate. |
Vapor Deposition (Silicon Targets) | Deposits silicon vapor onto a substrate for precise thickness and uniformity. |
Need high-quality sputtering targets tailored to your application? Contact our experts today for a customized solution!