Cleaning a sputtering target is a critical process to ensure optimal performance and longevity of the target, as well as to maintain the quality of the thin films deposited during the sputtering process. The cleaning process typically involves removing contaminants such as dust, oils, and oxidation layers that can negatively affect the sputtering process. The method of cleaning depends on the material of the target, the type of contaminants, and the equipment available. Common techniques include mechanical cleaning, chemical cleaning, and ultrasonic cleaning. Proper handling and storage after cleaning are also essential to prevent recontamination.
Key Points Explained:
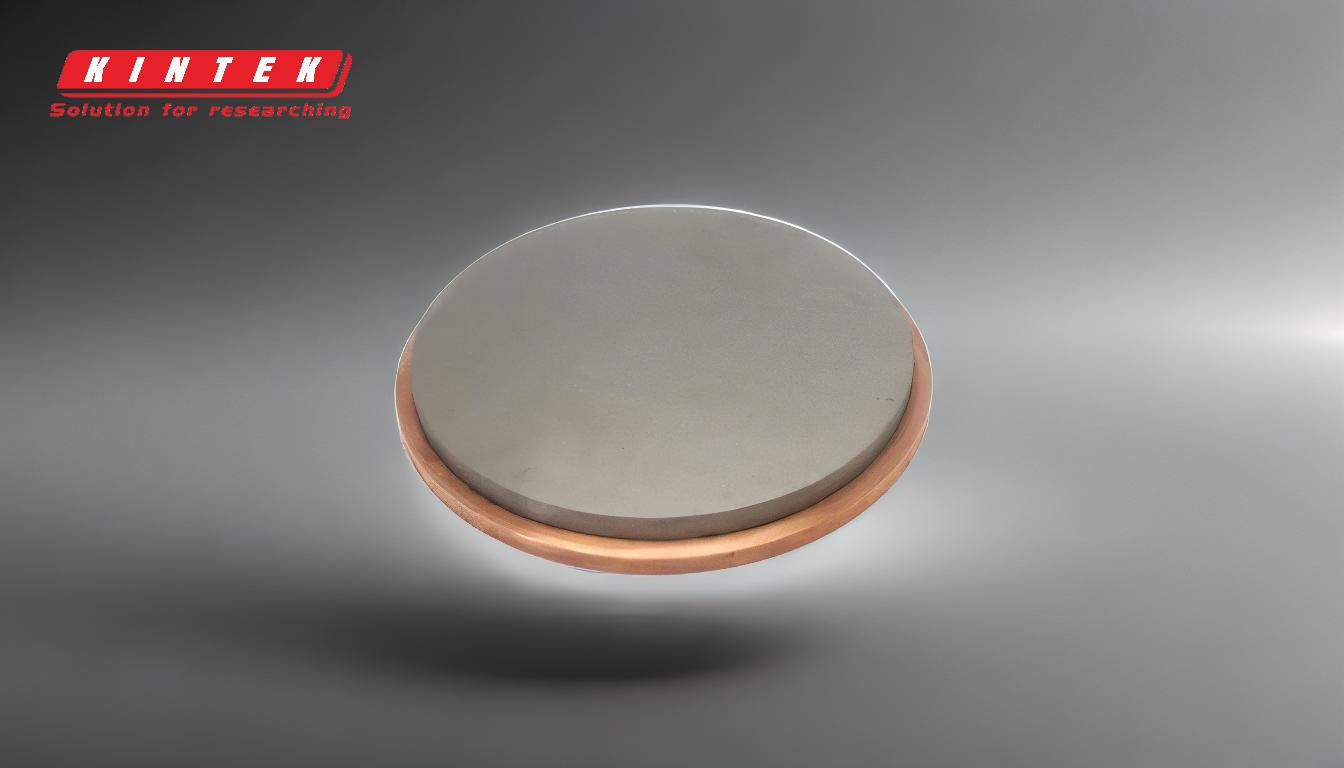
-
Understanding the Importance of Cleaning Sputtering Targets
- Sputtering targets are used in thin film deposition processes, and any contamination on the target surface can lead to defects in the deposited films.
- Contaminants such as dust, oils, and oxidation layers can reduce the efficiency of the sputtering process and affect the quality of the final product.
- Regular cleaning ensures consistent performance and extends the lifespan of the target.
-
Identifying the Type of Contaminants
- Dust and Particulates: These can be introduced during handling or from the environment.
- Oils and Greases: Often from fingerprints or improper handling.
- Oxidation Layers: Formed when the target material reacts with oxygen in the air, especially for reactive metals like aluminum or titanium.
- Residual Films: Leftover materials from previous sputtering runs.
-
Mechanical Cleaning Methods
- Abrasive Cleaning: Using fine abrasives or polishing compounds to remove surface contaminants. This method is suitable for hard targets like metals and ceramics.
- Sanding or Polishing: For targets with thick oxidation layers, sanding with fine-grit sandpaper or polishing with a soft cloth can be effective.
- Brushing: Using soft brushes to remove loose particles without scratching the surface.
-
Chemical Cleaning Methods
- Solvent Cleaning: Using solvents like acetone, isopropyl alcohol, or ethanol to dissolve oils and greases. This is effective for organic contaminants.
- Acid or Alkaline Cleaning: For more stubborn oxidation layers, acids (e.g., nitric acid, hydrochloric acid) or alkaline solutions can be used. This method requires careful handling and proper safety precautions.
- Etching: Chemical etching can be used to remove surface layers, but it must be done carefully to avoid damaging the target material.
-
Ultrasonic Cleaning
- Ultrasonic cleaning uses high-frequency sound waves to create cavitation bubbles in a cleaning solution, which effectively remove contaminants from the target surface.
- This method is particularly effective for removing fine particles and residues that are difficult to remove with mechanical or chemical methods.
- The choice of cleaning solution depends on the target material and the type of contaminants.
-
Post-Cleaning Handling and Storage
- After cleaning, the target should be thoroughly rinsed with deionized water to remove any residual cleaning agents.
- The target should be dried using a lint-free cloth or nitrogen gas to prevent water spots or oxidation.
- Proper storage in a clean, dry environment, preferably in a vacuum or inert gas atmosphere, is essential to prevent recontamination.
-
Safety Considerations
- Always wear appropriate personal protective equipment (PPE) such as gloves, goggles, and lab coats when handling chemicals or performing mechanical cleaning.
- Work in a well-ventilated area or fume hood when using solvents or acids.
- Dispose of chemical waste according to local regulations and safety guidelines.
-
Regular Maintenance and Inspection
- Regularly inspect the target for signs of contamination or wear.
- Establish a cleaning schedule based on the frequency of use and the type of materials being sputtered.
- Keep a record of cleaning procedures and any issues encountered to improve future cleaning processes.
By following these steps, you can effectively clean a sputtering target, ensuring optimal performance and high-quality thin film deposition. Proper cleaning not only enhances the efficiency of the sputtering process but also extends the life of the target, making it a cost-effective practice in the long run.
Summary Table:
Cleaning Method | Best For | Key Considerations |
---|---|---|
Mechanical Cleaning | Hard targets (metals, ceramics) | Avoid scratching the surface |
Chemical Cleaning | Oils, greases, oxidation layers | Use proper PPE and ventilation |
Ultrasonic Cleaning | Fine particles, residues | Choose the right cleaning solution |
Post-Cleaning Handling | Preventing recontamination | Store in a clean, dry environment |
Ensure your sputtering targets perform at their best—contact our experts today for personalized cleaning advice!