Plasma generation in sputtering is a critical step in the thin film deposition process, achieved by creating a high-voltage potential difference between the cathode (target) and the anode (chamber or substrate). This potential difference accelerates electrons, which collide with neutral gas atoms (typically argon) in the chamber, causing ionization. The resulting plasma consists of positively charged ions and free electrons. The ions are then accelerated toward the negatively charged cathode, striking the target material and ejecting atoms that deposit onto the substrate. This process requires a vacuum environment, a noble gas, and either DC or RF power to sustain the plasma.
Key Points Explained:
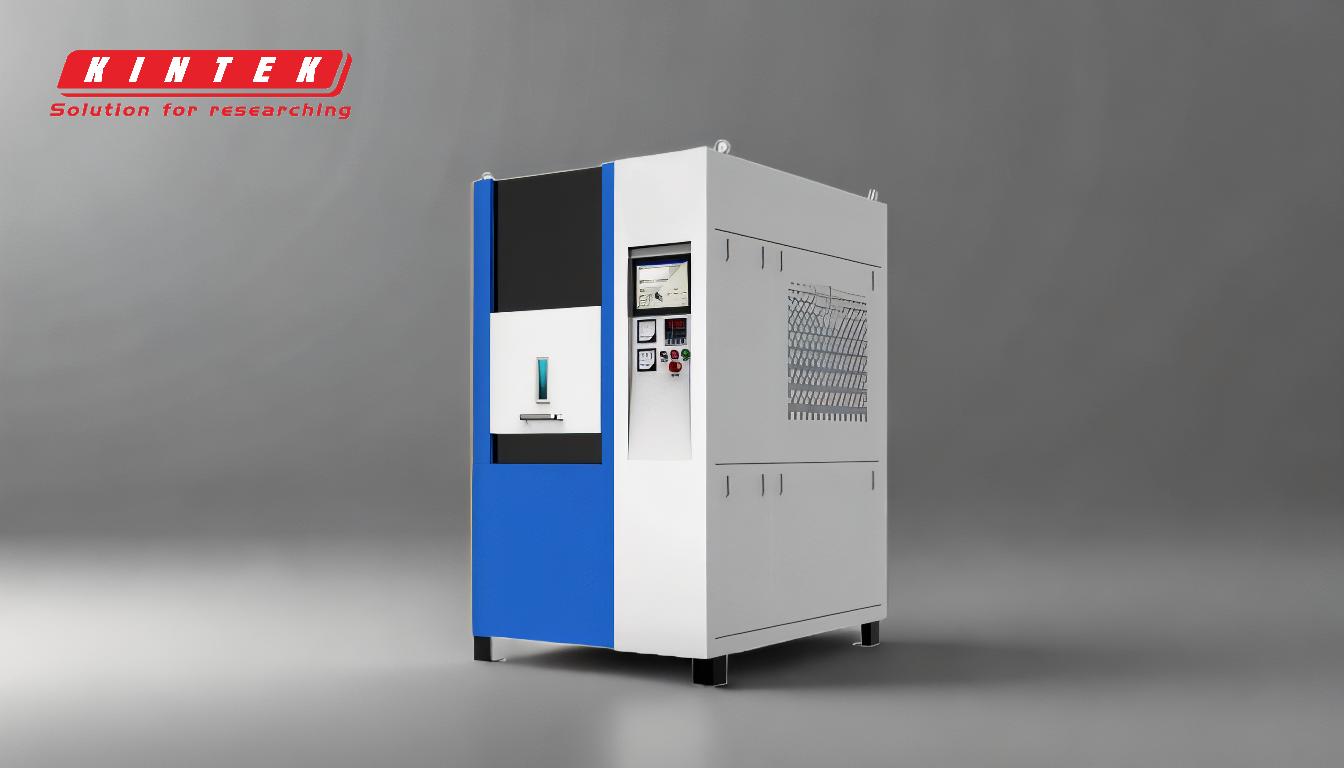
-
High Voltage Application:
- A high voltage is applied between the cathode (target) and the anode (chamber or substrate).
- This creates an electric field that accelerates electrons away from the cathode.
-
Electron Collisions and Ionization:
- Accelerated electrons collide with neutral gas atoms (usually argon) in the chamber.
- These collisions ionize the gas atoms, creating positively charged ions and additional free electrons.
-
Formation of Plasma:
- The ionized gas forms a plasma, a state of matter consisting of free electrons, ions, and neutral atoms.
- The plasma is sustained by continuous ionization due to the applied voltage.
-
Role of Noble Gas:
- Noble gases like argon are used because they are inert and do not react chemically with the target or substrate.
- Argon is introduced into the vacuum chamber at a controlled pressure to facilitate plasma formation.
-
Acceleration of Ions Toward the Cathode:
- Positively charged ions in the plasma are attracted to the negatively charged cathode (target).
- These ions gain high kinetic energy as they accelerate toward the target.
-
High-Energy Collisions with the Target:
- When the ions collide with the target, they dislodge (sputter) atoms from the target material.
- The ejected atoms travel through the vacuum and deposit onto the substrate, forming a thin film.
-
Types of Sputtering:
- DC Sputtering: Uses direct current (DC) power for conductive targets.
- RF Sputtering: Uses radio frequency (RF) power for insulating targets, as it prevents charge buildup.
-
Vacuum Environment:
- The process occurs in a vacuum chamber to minimize contamination and ensure efficient plasma generation.
- The vacuum reduces the presence of other gases that could interfere with the sputtering process.
-
Dynamic Plasma Environment:
- The plasma is a dynamic system with neutral atoms, ions, electrons, and photons in near equilibrium.
- This environment ensures continuous ionization and sputtering of the target material.
-
Applications and Importance:
- Plasma sputtering is widely used in industries such as semiconductors, optics, and coatings.
- It allows for precise control over thin film deposition, enabling the creation of high-quality, uniform layers.
By understanding these key points, equipment and consumable purchasers can better evaluate the requirements for plasma sputtering systems, such as the type of power supply (DC or RF), the choice of noble gas, and the quality of the vacuum chamber. This knowledge ensures the selection of appropriate components for achieving efficient and reliable thin film deposition.
Summary Table:
Key Aspect | Description |
---|---|
High Voltage Application | Creates an electric field to accelerate electrons. |
Electron Collisions | Electrons collide with argon atoms, causing ionization. |
Plasma Formation | Ionized gas forms plasma with free electrons, ions, and neutral atoms. |
Noble Gas Role | Argon is used for its inert properties and controlled pressure. |
Ion Acceleration | Positively charged ions are attracted to the negatively charged cathode. |
Target Collisions | High-energy ions dislodge target atoms, which deposit onto the substrate. |
Sputtering Types | DC for conductive targets, RF for insulating targets. |
Vacuum Environment | Ensures minimal contamination and efficient plasma generation. |
Dynamic Plasma | Continuous ionization and sputtering in a near-equilibrium environment. |
Applications | Used in semiconductors, optics, and coatings for precise thin film deposition. |
Optimize your thin film deposition process—contact our experts today for tailored solutions!