In the pharmaceutical industry, reactors play a crucial role in facilitating chemical reactions, synthesis, and production processes. Based on the references provided, there are several types of reactors commonly used, each designed for specific applications and operational requirements. These include stirred reactors, high-pressure reactors, glass-lined reactors, continuous flow tubular reactors, and custom configurations for specialized research. Below is a detailed explanation of the various types of reactors and their applications in the pharmaceutical industry.
Key Points Explained:
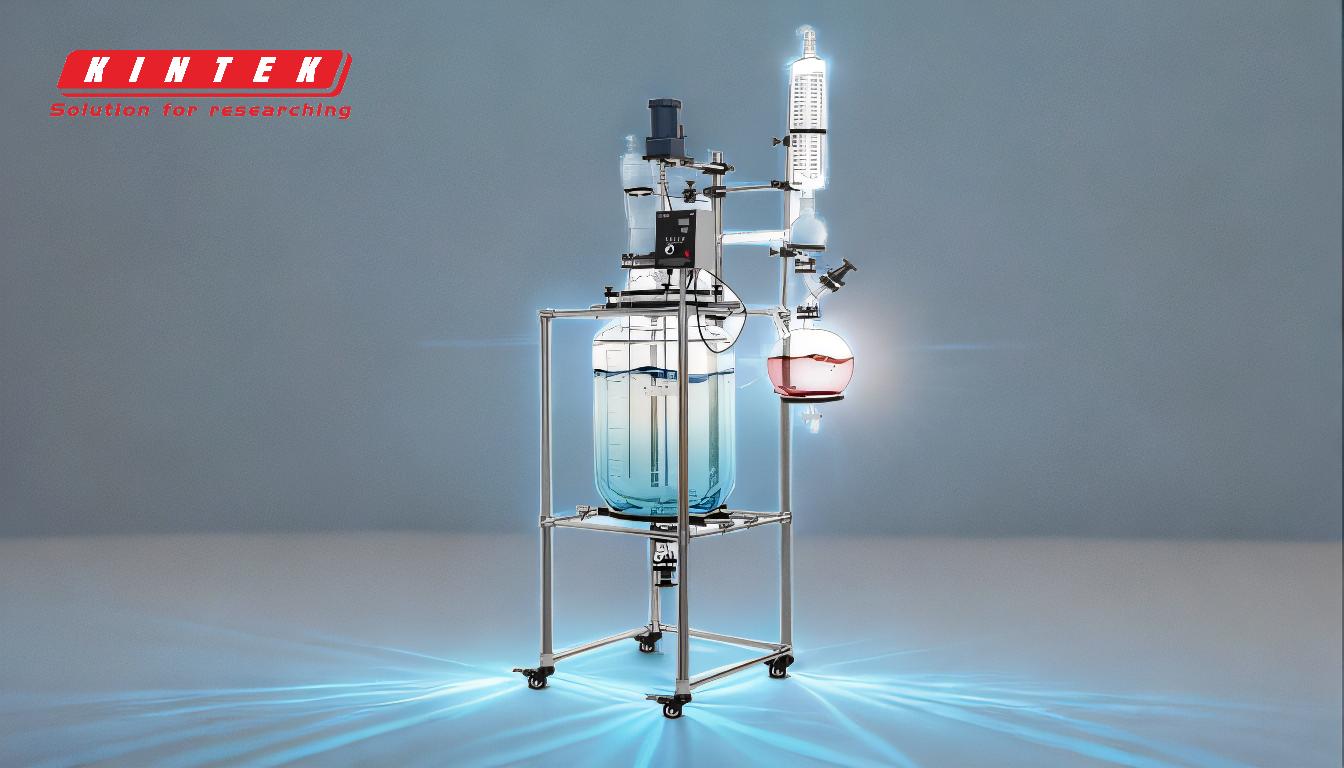
-
Stirred Reactors:
- Description: Stirred reactors are equipped with mechanical agitators to ensure uniform mixing of reactants, which is essential for consistent reaction kinetics and product quality.
- Applications: Widely used in pharmaceutical manufacturing for processes such as crystallization, polymerization, and chemical synthesis.
- Advantages: Efficient mixing, scalability, and flexibility in handling different reaction conditions.
-
High-Pressure Reactors:
- Description: These reactors are designed to withstand high pressures, making them suitable for reactions that require elevated pressure conditions.
- Applications: Commonly used in hydrogenation, oxidation, and other high-pressure reactions in pharmaceutical production.
- Advantages: Enables reactions that are not feasible at atmospheric pressure, improving reaction rates and yields.
-
Glass-Lined Reactors:
- Description: Glass-lined reactors have a glass coating on the interior surfaces, providing excellent resistance to corrosion and chemical attack.
- Applications: Ideal for handling highly corrosive substances and reactions involving acidic or alkaline conditions.
- Advantages: Durability, chemical resistance, and ease of cleaning, which are critical for maintaining product purity.
-
Continuous Flow Tubular Reactors:
- Description: These reactors operate in a continuous flow mode, where reactants flow through a tubular system, often with external heating or jacketed cooling.
- Applications: Suitable for continuous production processes, such as the synthesis of intermediates or active pharmaceutical ingredients (APIs).
- Advantages: High efficiency, consistent product quality, and reduced waste generation.
-
Mini Reactors:
- Description: Mini reactors are small-scale versions of larger reactors, designed for laboratory-scale research and development.
- Applications: Used for process optimization, scale-up studies, and small-batch production in pharmaceutical R&D.
- Advantages: Cost-effective, easy to operate, and ideal for testing new reactions or formulations.
-
Custom Configurations:
- Description: Custom reactors are tailored to specific research or production needs, such as those designed for biofuels research or other specialized applications.
- Applications: Used in niche areas of pharmaceutical research, such as biopharmaceuticals or green chemistry.
- Advantages: Flexibility to meet unique requirements, enabling innovation and specialized production processes.
-
Other Reactor Types:
- Hydrothermal Synthesis Reactors: Used for reactions under high-temperature and high-pressure aqueous conditions.
- Magnetic Stirring Reactors: Utilize magnetic fields for stirring, reducing mechanical wear and contamination risks.
- Electric Heating Reactors: Equipped with electric heating elements for precise temperature control.
- Steam Reactors: Use steam as a heating medium, often for large-scale industrial processes.
By understanding the different types of reactors and their specific applications, pharmaceutical manufacturers can select the most appropriate reactor type for their production needs, ensuring optimal efficiency, product quality, and safety.
Summary Table:
Reactor Type | Applications | Advantages |
---|---|---|
Stirred Reactors | Crystallization, polymerization, chemical synthesis | Efficient mixing, scalability, flexibility |
High-Pressure Reactors | Hydrogenation, oxidation, high-pressure reactions | Enables high-pressure reactions, improves reaction rates and yields |
Glass-Lined Reactors | Handling corrosive substances, acidic/alkaline reactions | Durability, chemical resistance, easy cleaning |
Continuous Flow Reactors | Synthesis of intermediates, APIs, continuous production | High efficiency, consistent quality, reduced waste |
Mini Reactors | Process optimization, scale-up studies, small-batch production | Cost-effective, easy to operate, ideal for R&D |
Custom Configurations | Biopharmaceuticals, green chemistry, specialized applications | Flexibility for unique requirements, enables innovation |
Looking for the right reactor for your pharmaceutical production? Contact our experts today to find the perfect solution!