Packed bed reactors and fixed bed reactors are terms often used interchangeably in chemical engineering, but they can have nuanced differences depending on the context. Both involve a stationary bed of solid particles through which a fluid flows, facilitating chemical reactions, heat transfer, or mass transfer. However, the terms may refer to slightly different operational or design characteristics. This answer explores the similarities and differences between the two, helping clarify whether they are the same or distinct.
Key Points Explained:
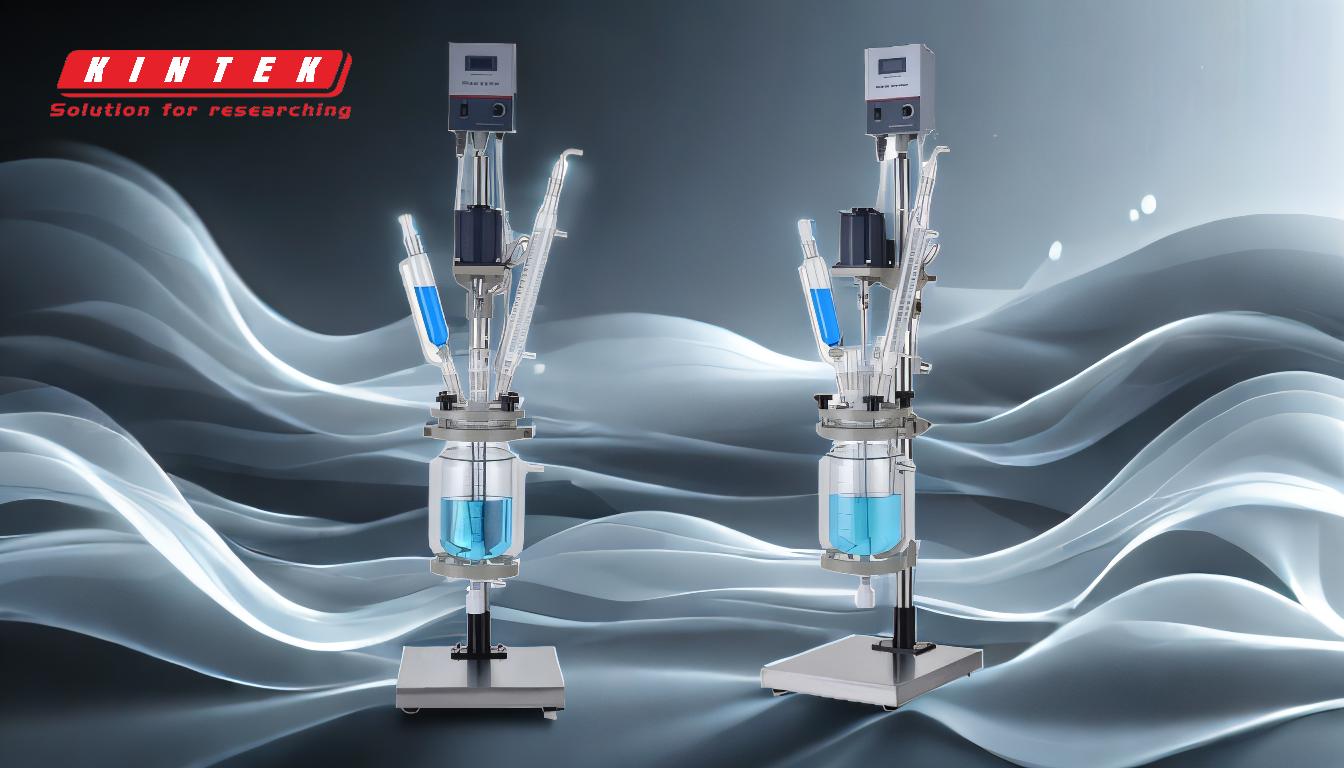
-
Definition of Packed Bed Reactor:
- A packed bed reactor is a type of reactor where solid particles (catalysts, adsorbents, or other materials) are packed into a column or vessel.
- The fluid (gas or liquid) flows through the bed of particles, enabling reactions or separation processes.
- The term "packed bed" emphasizes the arrangement of particles, which are often randomly packed to maximize surface area and interaction with the fluid.
-
Definition of Fixed Bed Reactor:
- A fixed bed reactor also involves a stationary bed of solid particles through which a fluid flows.
- The term "fixed bed" highlights that the solid particles remain stationary and do not move during operation.
- Fixed bed reactors are commonly used in catalytic processes, where the catalyst remains in place while reactants flow through.
-
Similarities Between Packed Bed and Fixed Bed Reactors:
- Both involve a stationary bed of solid particles.
- Both are used for chemical reactions, adsorption, or other processes requiring interaction between a fluid and solid phase.
- The design principles, such as pressure drop considerations and heat transfer, are often similar.
- Both can operate in continuous or batch modes.
-
Differences Between Packed Bed and Fixed Bed Reactors:
- Terminology Context: The term "packed bed" often refers to the physical arrangement of particles, while "fixed bed" emphasizes the immobility of the particles.
- Applications: Packed bed reactors are sometimes associated with non-catalytic processes like adsorption or filtration, whereas fixed bed reactors are more commonly linked to catalytic reactions.
- Design Variations: In some cases, packed bed reactors may include structured packing (e.g., ordered arrangements), while fixed bed reactors typically use random packing.
-
Operational Considerations:
- Both types of reactors require careful design to manage pressure drops, ensure uniform fluid distribution, and optimize heat and mass transfer.
- The choice between the two often depends on the specific application, such as whether the process is catalytic or non-catalytic.
-
Conclusion:
- In most practical contexts, packed bed reactors and fixed bed reactors are considered the same, as both involve a stationary bed of solid particles through which a fluid flows.
- However, subtle differences in terminology and application may lead to distinctions in specific cases.
By understanding these key points, it becomes clear that while the terms are often used interchangeably, their usage may vary based on context and application. For most purposes, they can be considered the same, but it's important to consider the specific requirements of the process when choosing or designing a reactor.
Summary Table:
Aspect | Packed Bed Reactor | Fixed Bed Reactor |
---|---|---|
Definition | Solid particles packed in a column; fluid flows through. | Stationary solid particles; fluid flows through. |
Terminology Emphasis | Focuses on particle arrangement (e.g., random packing). | Emphasizes immobility of particles. |
Common Applications | Adsorption, filtration, non-catalytic processes. | Catalytic reactions, chemical processes. |
Design Variations | May include structured or random packing. | Typically uses random packing. |
Operational Mode | Continuous or batch. | Continuous or batch. |
Need help selecting the right reactor for your application? Contact our experts today for personalized guidance!