Two-high rolling mills offer several advantages, particularly in hot rolling applications, due to their simpler design and operational efficiency. These mills are self-cleaning, which reduces maintenance downtime, and allow for quick roll changes, enhancing productivity. Their straightforward construction also makes them more cost-effective compared to more complex rolling mills like 4-high mills. Below, the key advantages are explained in detail.
Key Points Explained:
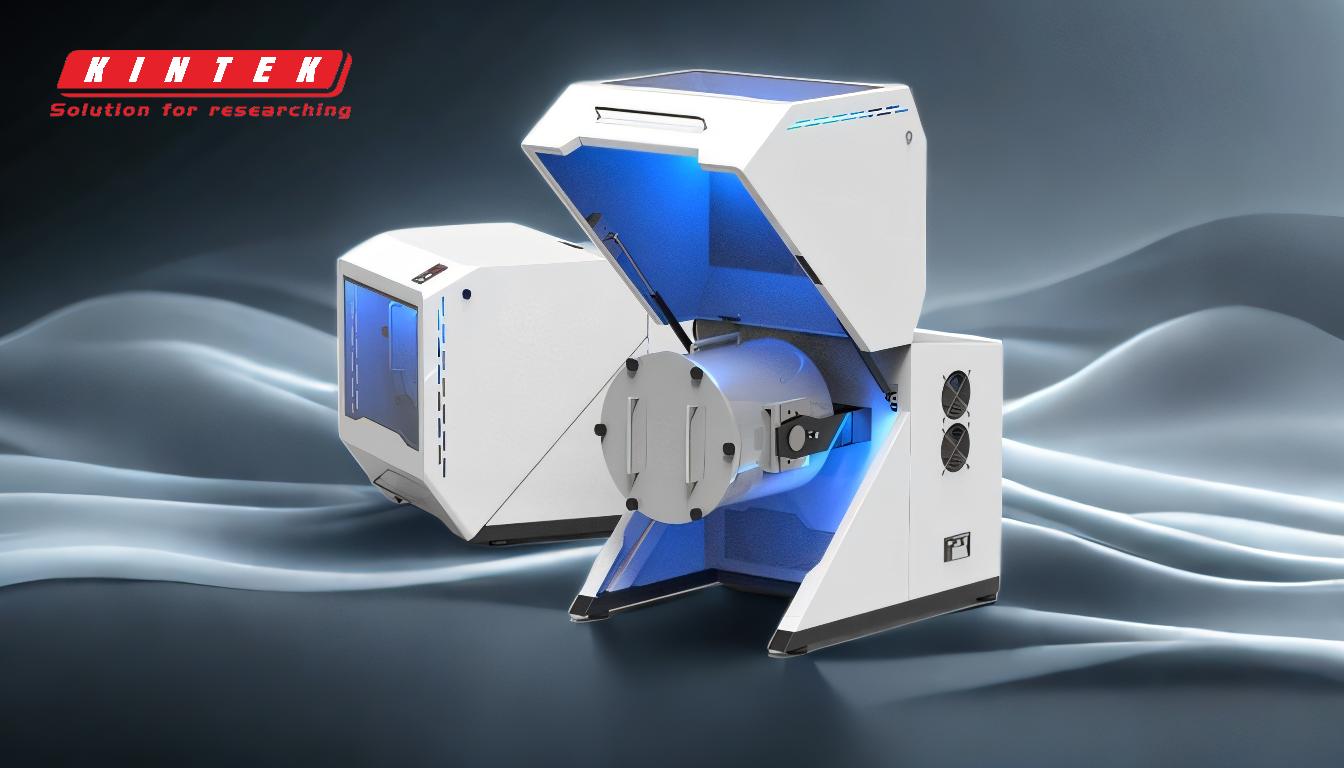
-
Self-Cleaning Rolls
- In a two-high rolling mill, the rolls are self-cleaning, meaning that debris or scale from the material being rolled is less likely to accumulate on the rolls.
- This feature is particularly beneficial in hot rolling processes, where scale formation is common.
- By reducing debris buildup, the mill maintains consistent rolling performance and minimizes the risk of defects in the rolled material.
-
Reduced Roll Replacement Frequency
- The work rolls in a two-high mill do not need to be replaced as often as those in a 4-high mill.
- This is because the simpler design of a two-high mill subjects the rolls to less wear and tear compared to the more complex configurations of 4-high mills.
- Reduced roll replacement frequency translates to lower operational costs and less downtime for maintenance.
-
Quick Roll Change Mechanism
- Two-high mills are designed to allow rolls to be pushed out from the side of the mill, enabling quick and efficient roll changes.
- This feature is critical for maintaining high productivity, especially in industrial settings where downtime directly impacts output.
- The ability to rapidly replace rolls ensures that the rolling process can resume with minimal interruption.
-
Simpler Design and Lower Costs
- Two-high mills have a straightforward design with fewer components compared to 4-high mills.
- This simplicity makes them easier to manufacture, install, and maintain, resulting in lower capital and operational expenses.
- For applications where high precision is not the primary requirement, two-high mills provide a cost-effective solution.
-
Suitability for Hot Rolling Applications
- The self-cleaning nature and robust design of two-high mills make them particularly well-suited for hot rolling processes.
- Hot rolling involves high temperatures and significant scale formation, and the two-high mill's design effectively handles these challenges.
- The mill's ability to operate efficiently under these conditions ensures consistent quality and throughput.
In summary, two-high rolling mills are advantageous due to their self-cleaning rolls, reduced roll replacement needs, quick change mechanisms, simpler design, and suitability for hot rolling. These features make them a practical and cost-effective choice for many industrial rolling applications.
Summary Table:
Advantage | Description |
---|---|
Self-Cleaning Rolls | Reduces debris buildup, ensuring consistent performance and fewer defects. |
Reduced Roll Replacement | Less wear and tear lowers operational costs and maintenance downtime. |
Quick Roll Change Mechanism | Enables rapid roll changes, minimizing downtime and boosting productivity. |
Simpler Design and Lower Costs | Fewer components make manufacturing, installation, and maintenance more affordable. |
Suitability for Hot Rolling | Robust design handles high temperatures and scale formation effectively. |
Ready to enhance your rolling operations? Contact us today to learn more about two-high rolling mills!