A 4-high rolling mill, while efficient for high production metal rolling, has certain disadvantages. The primary disadvantage is the elongation of material edges due to the lack of supporting surfaces, which can lead to quality issues in the rolled product. Additionally, the open area on the rollers can cause loss of volatiles, affecting the consistency and quality of the material being processed. These factors can impact the overall efficiency and output quality of the rolling process.
Key Points Explained:
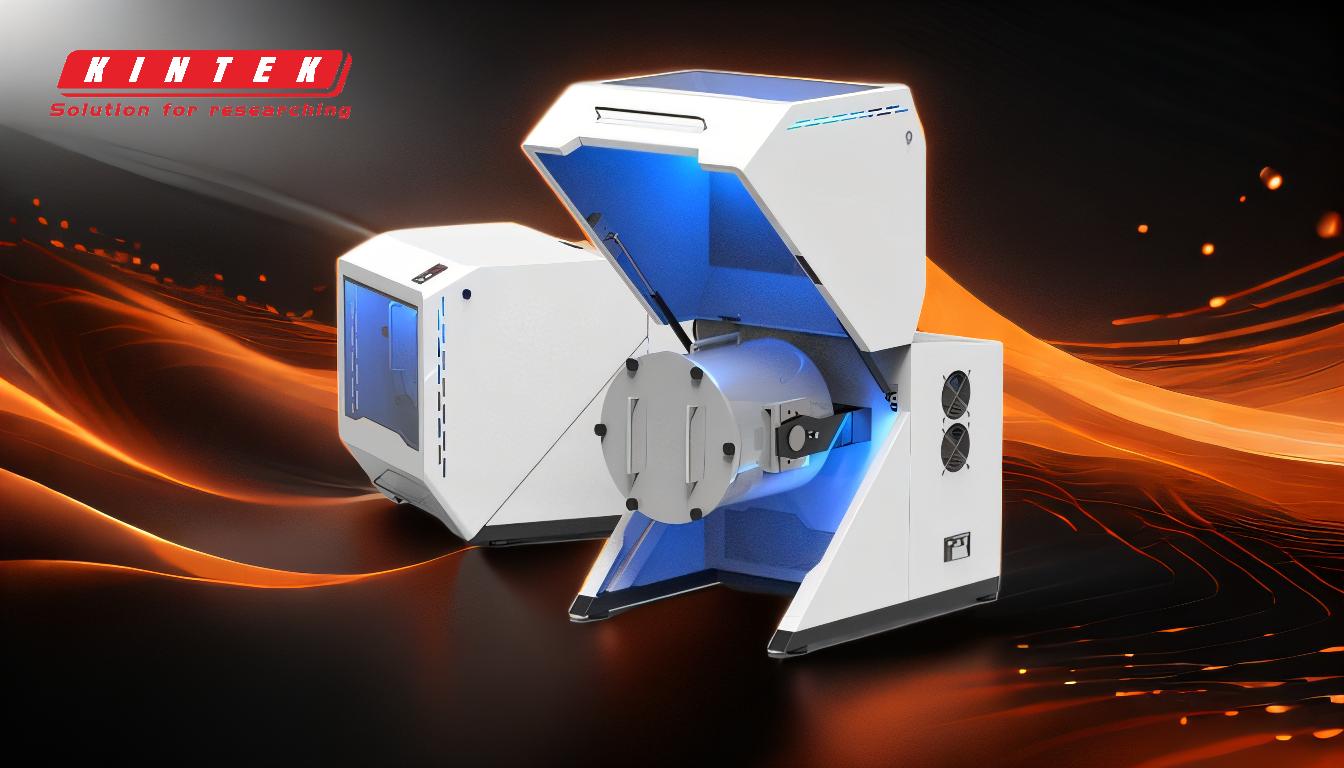
-
Edge Elongation:
- Description: In a 4-high rolling mill, the edges of the material being rolled tend to elongate. This is because there is no supporting surface at the edges.
- Impact: This elongation can lead to uneven thickness and quality issues in the final product. It may require additional processing steps to correct these imperfections, increasing production time and costs.
-
Loss of Volatiles:
- Description: The large open area of paste on the rollers in a 4-high rolling mill can cause a loss of volatiles.
- Impact: The loss of volatiles can affect the consistency and quality of the material being processed. This can lead to variations in the final product's properties, potentially requiring additional quality control measures and increasing waste.
-
Operational Challenges:
- Description: The design of a 4-high rolling mill can present certain operational challenges.
- Impact: These challenges can include difficulties in maintaining uniform pressure across the rollers, leading to potential defects in the rolled material. Operators may need to adjust settings frequently to maintain quality, which can reduce overall efficiency.
-
Maintenance Requirements:
- Description: The complexity of a 4-high rolling mill can lead to higher maintenance requirements.
- Impact: Regular maintenance is necessary to ensure the rollers and other components are in good working condition. This can increase downtime and maintenance costs, impacting the overall productivity of the rolling mill.
-
Material Limitations:
- Description: Certain materials may not be suitable for processing in a 4-high rolling mill due to the aforementioned issues.
- Impact: This limitation can restrict the types of materials that can be efficiently processed, potentially requiring alternative methods for certain materials, which can increase production complexity and costs.
-
Cost Implications:
- Description: The disadvantages of a 4-high rolling mill can have cost implications.
- Impact: Increased production time, additional processing steps, higher maintenance costs, and the need for alternative processing methods can all contribute to higher overall costs. This can affect the profitability of using a 4-high rolling mill for certain applications.
In summary, while 4-high rolling mills are efficient for high production metal rolling, they come with several disadvantages that can impact the quality, consistency, and cost of the rolled products. Understanding these drawbacks is crucial for making informed decisions about their use in various industrial applications.
Summary Table:
Disadvantage | Description | Impact |
---|---|---|
Edge Elongation | Edges elongate due to lack of supporting surfaces. | Uneven thickness, quality issues, increased production time and costs. |
Loss of Volatiles | Open roller areas cause loss of volatiles. | Inconsistent material quality, increased waste, and additional quality control measures. |
Operational Challenges | Difficulty maintaining uniform pressure across rollers. | Potential defects, frequent adjustments, reduced efficiency. |
Maintenance Requirements | Complex design leads to higher maintenance needs. | Increased downtime, higher maintenance costs, reduced productivity. |
Material Limitations | Some materials are unsuitable due to edge elongation and volatiles loss. | Restricted material types, increased production complexity and costs. |
Cost Implications | Higher production time, maintenance, and alternative processing costs. | Reduced profitability for certain applications. |
Want to optimize your rolling mill operations? Contact our experts today for tailored solutions!