Centrifugal filtration, while effective in many applications, has several disadvantages that can impact its efficiency, cost, and suitability for certain processes. These drawbacks include higher operational costs, potential damage to sensitive materials, limitations in scalability, and the need for specialized equipment. Understanding these disadvantages is crucial for making informed decisions when selecting filtration methods for specific applications.
Key Points Explained:
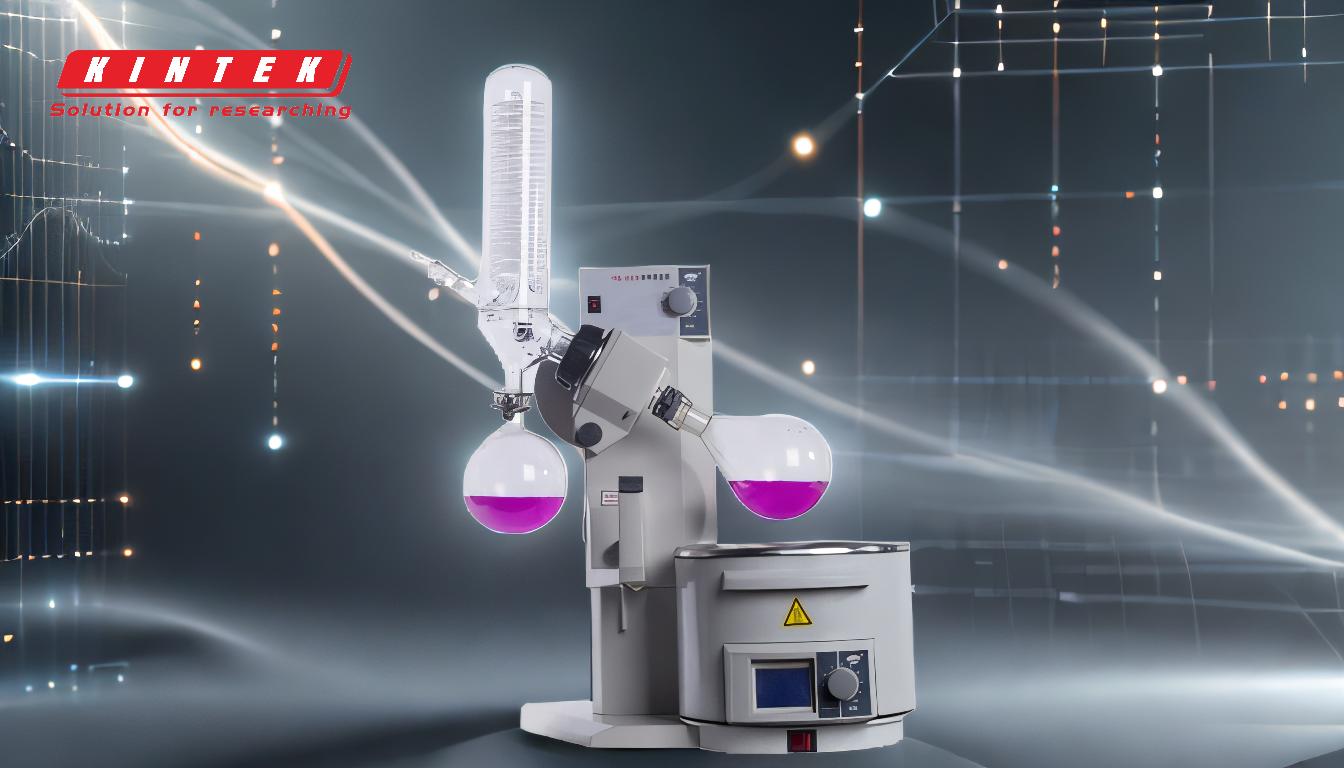
-
Higher Operational Costs:
- Centrifugal filtration systems often require significant energy to operate, especially when dealing with large volumes or high-speed rotations. This can lead to increased electricity consumption and higher operational costs.
- Maintenance costs can also be higher due to the wear and tear on moving parts, such as the centrifuge rotor and motor, which may require frequent servicing or replacement.
-
Potential Damage to Sensitive Materials:
- The high-speed rotation involved in centrifugal filtration can generate significant shear forces, which may damage delicate or fragile materials, such as biological samples or certain polymers.
- This makes centrifugal filtration less suitable for applications where the integrity of the sample must be preserved.
-
Limitations in Scalability:
- While centrifugal filtration is effective for small to medium-scale applications, it may not be as scalable as other filtration methods for large-scale industrial processes.
- The need for specialized equipment and the physical limitations of centrifuge size can restrict the volume of material that can be processed at once.
-
Complexity and Specialized Equipment:
- Centrifugal filtration systems are often more complex to set up and operate compared to simpler filtration methods, such as gravity filtration or vacuum filtration.
- The need for specialized equipment, such as high-speed centrifuges and rotors, can also increase initial capital costs and require additional training for operators.
-
Environmental and Safety Concerns:
- The high-speed operation of centrifugal filtration systems can pose safety risks, such as the potential for rotor failure or the ejection of materials if the centrifuge is not properly balanced.
- Additionally, the energy consumption associated with centrifugal filtration can have environmental implications, particularly if the energy source is not renewable.
-
Limited Flexibility in Filtration Media:
- Centrifugal filtration typically relies on specific types of filtration media, such as filter papers or membranes, which may not be suitable for all types of samples or applications.
- This lack of flexibility can limit the versatility of centrifugal filtration in comparison to other methods that allow for a wider range of filtration media.
In summary, while centrifugal filtration is a powerful tool in many scientific and industrial applications, its disadvantages—such as higher operational costs, potential damage to sensitive materials, and limitations in scalability—must be carefully considered. These factors can influence the overall efficiency, cost-effectiveness, and suitability of centrifugal filtration for specific processes.
Summary Table:
Disadvantage | Key Details |
---|---|
Higher Operational Costs | Increased energy consumption, high maintenance due to wear and tear. |
Damage to Sensitive Materials | High-speed rotation can harm delicate samples like biological or polymer materials. |
Limitations in Scalability | Less suitable for large-scale industrial processes due to equipment constraints. |
Complexity & Specialized Equipment | Requires high-speed centrifuges, rotors, and operator training. |
Environmental & Safety Concerns | Safety risks like rotor failure; high energy use impacts the environment. |
Limited Filtration Media Flexibility | Restricted to specific media types, reducing versatility. |
Need help choosing the right filtration method? Contact our experts today for personalized advice!