Fluidized bed reactors (FBRs) are widely used in industries for their advantages, such as uniform particle mixing, temperature gradients, and continuous operation. However, they also come with several disadvantages that can impact their efficiency, cost, and scalability. These include increased reactor vessel size, higher pumping requirements, particle entrainment, erosion of internal components, and challenges related to material behavior understanding and pressure loss scenarios. Understanding these drawbacks is crucial for industries to make informed decisions about their application and to develop strategies to mitigate these issues.
Key Points Explained:
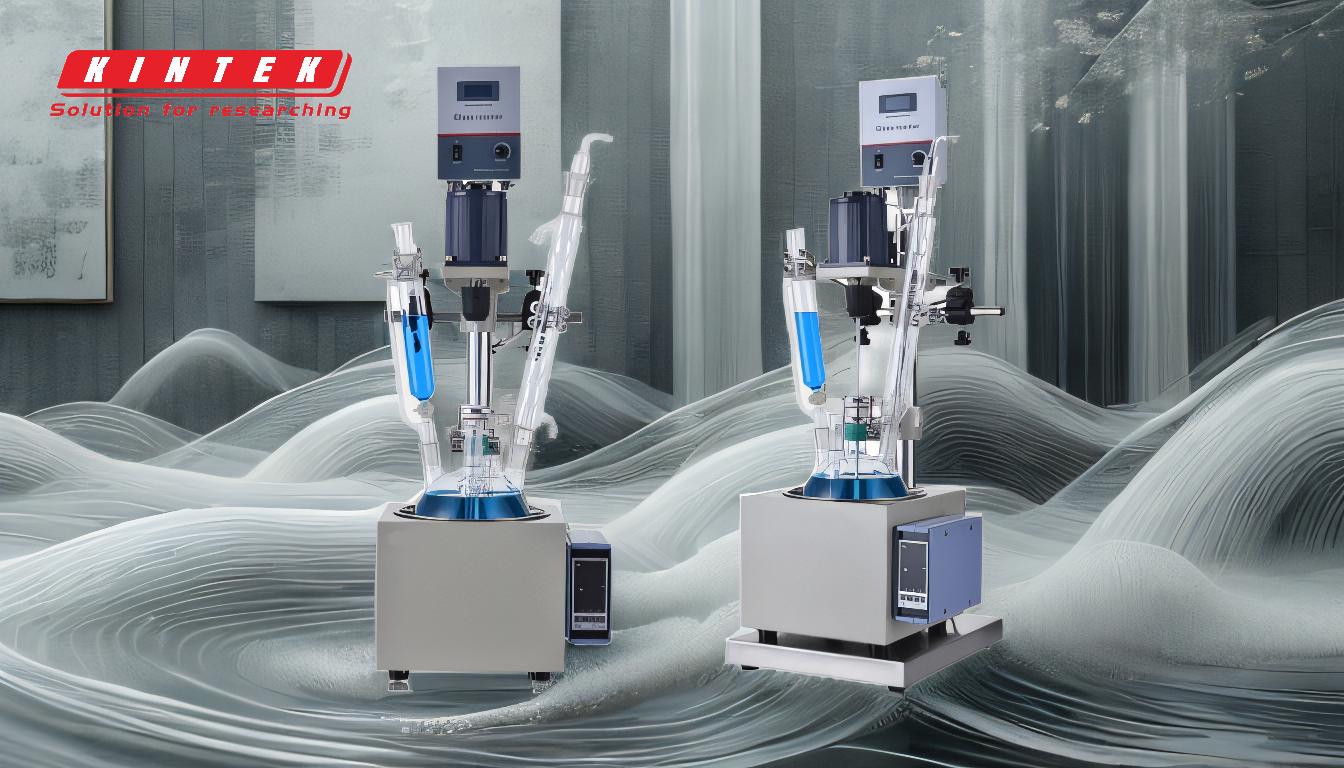
-
Increased Reactor Vessel Size:
- Fluidized bed reactors require larger vessel sizes compared to other reactor types. This is due to the need to accommodate the fluidization process, which involves suspending solid particles in a gas or liquid to create a fluid-like state. The larger size increases capital costs and space requirements, making FBRs less suitable for applications where space is limited.
-
Higher Pumping Requirements and Pressure Drop:
- Maintaining the fluidization state requires significant energy input, leading to higher pumping requirements. This results in increased operational costs. Additionally, the pressure drop across the reactor is higher due to the resistance offered by the fluidized particles, which can further strain the pumping system and reduce overall efficiency.
-
Particle Entrainment:
- One of the significant challenges in FBRs is particle entrainment, where fine particles are carried out of the reactor by the fluidizing gas. This can lead to product loss, contamination of downstream equipment, and the need for additional separation processes, such as cyclones or filters, to capture and recycle the entrained particles.
-
Lack of Current Understanding of Material Behavior:
- The behavior of materials in a fluidized bed is complex and not yet fully understood. This includes the dynamics of particle movement, heat transfer, and chemical reactions. The lack of comprehensive models and predictive tools can make it challenging to optimize reactor design and operation, leading to suboptimal performance and potential safety risks.
-
Erosion of Internal Components:
- The continuous movement of particles in a fluidized bed can cause erosion of internal components, such as the reactor walls, distributor plates, and heat exchangers. This erosion can lead to frequent maintenance requirements, increased downtime, and higher operational costs. In severe cases, it can compromise the structural integrity of the reactor.
-
Pressure Loss Scenarios:
- FBRs are susceptible to pressure loss scenarios, where the fluidization process is disrupted, leading to uneven particle distribution and poor reactor performance. This can occur due to changes in operating conditions, such as variations in gas flow rate or particle size distribution. Pressure loss scenarios can result in reduced product quality, increased energy consumption, and potential safety hazards.
In summary, while fluidized bed reactors offer several advantages, such as uniform mixing and temperature control, they also present significant challenges that need to be carefully managed. These include increased reactor size, higher energy requirements, particle entrainment, material behavior uncertainties, component erosion, and pressure loss issues. Addressing these disadvantages through improved design, advanced materials, and better process control can help maximize the benefits of FBRs in industrial applications.
Summary Table:
Disadvantage | Description |
---|---|
Increased Reactor Vessel Size | Larger vessels increase capital costs and space requirements. |
Higher Pumping Requirements | Significant energy input needed, leading to higher operational costs. |
Particle Entrainment | Fine particles carried out, causing product loss and contamination risks. |
Erosion of Internal Components | Continuous particle movement erodes reactor parts, increasing maintenance costs. |
Pressure Loss Scenarios | Disruptions in fluidization reduce efficiency and pose safety hazards. |
Need help addressing fluidized bed reactor challenges? Contact our experts today for tailored solutions!