Getter pumps, while highly effective in creating and maintaining ultra-high vacuum environments, come with several disadvantages that potential users should consider. These include limited gas absorption capacity, sensitivity to certain gases, high initial and operational costs, and the need for periodic regeneration or replacement. Additionally, getter pumps are not suitable for all types of gases, particularly inert gases and hydrocarbons, which can limit their applicability in certain industrial or research settings. Understanding these drawbacks is crucial for making an informed decision when selecting vacuum pump technology.
Key Points Explained:
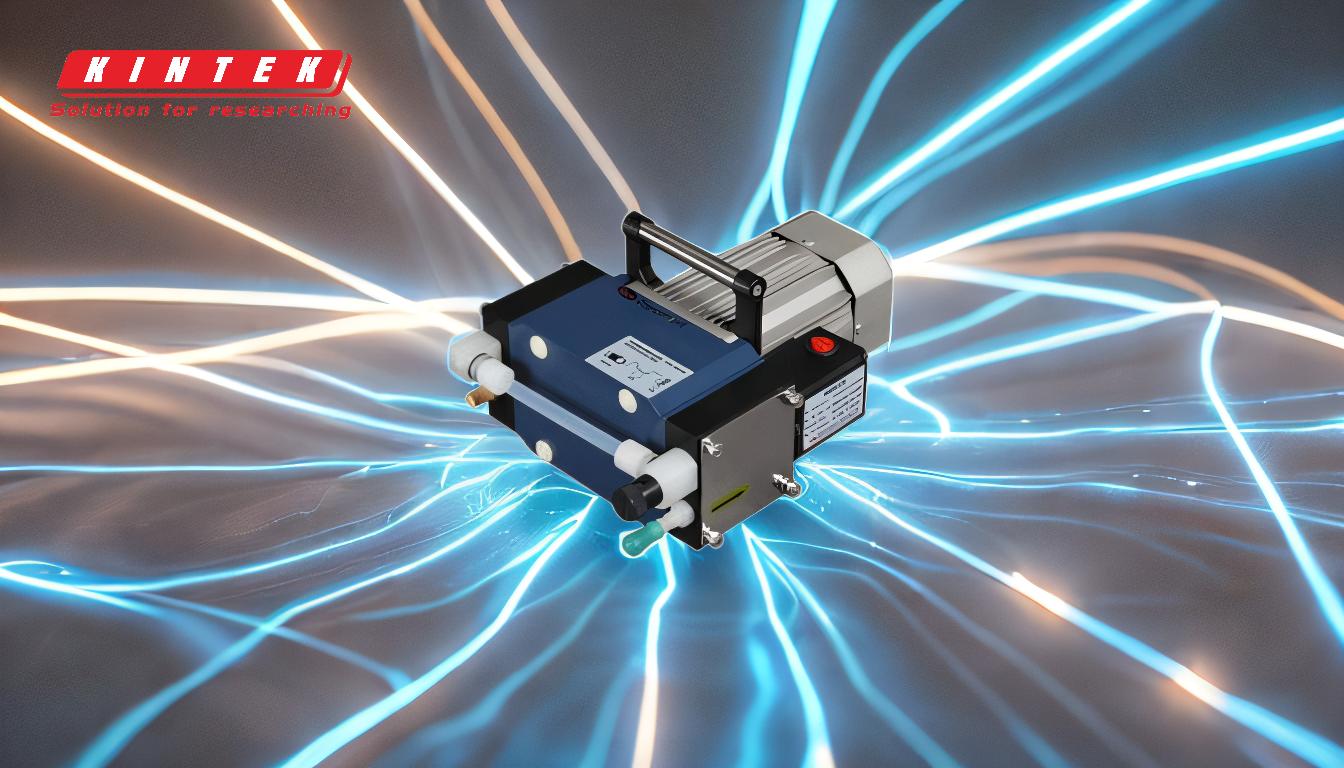
-
Limited Gas Absorption Capacity:
- Getter pumps rely on chemical reactions or physical adsorption to capture gas molecules. Over time, the getter material becomes saturated, reducing its effectiveness. This limitation means that getter pumps cannot continuously operate without periodic regeneration or replacement, which can be inconvenient and costly.
-
Sensitivity to Certain Gases:
- Getter pumps are highly effective for reactive gases like hydrogen, oxygen, and nitrogen but are less effective or completely ineffective for inert gases (e.g., argon, helium) and hydrocarbons. This restricts their use in environments where these gases are present, necessitating alternative pumping solutions.
-
High Initial and Operational Costs:
- The initial investment for getter pumps is often higher compared to other vacuum pump technologies. Additionally, the cost of getter materials and the need for periodic regeneration or replacement add to the operational expenses, making them less economical for some applications.
-
Need for Periodic Regeneration or Replacement:
- Once the getter material is saturated, it must be regenerated or replaced to restore the pump's efficiency. This process can be time-consuming and may require specialized equipment or expertise, leading to downtime and additional costs.
-
Limited Lifespan:
- The lifespan of a getter pump is directly tied to the capacity of the getter material. Frequent use in high-gas-load environments can significantly shorten its operational life, necessitating more frequent maintenance or replacement.
-
Incompatibility with Oils and Contaminants:
- Getter pumps are sensitive to contamination from oils and other substances, which can degrade the getter material and reduce its effectiveness. This makes them unsuitable for environments where such contaminants are present unless additional filtration systems are employed.
-
Complexity in Integration:
- Integrating getter pumps into existing vacuum systems can be complex, especially when combining them with other types of pumps. The need for careful system design to avoid contamination and ensure compatibility can increase the overall complexity and cost of the vacuum system.
-
Environmental and Safety Concerns:
- Some getter materials, such as titanium, can pose safety and environmental hazards if not handled properly. The disposal of used getter materials must be managed carefully to avoid environmental contamination.
By understanding these disadvantages, potential users can better assess whether getter pumps are the right choice for their specific vacuum requirements. While they offer significant advantages in certain applications, their limitations must be carefully weighed against the operational and financial implications.
Summary Table:
Disadvantage | Explanation |
---|---|
Limited Gas Absorption Capacity | Requires periodic regeneration or replacement due to saturation. |
Sensitivity to Certain Gases | Ineffective for inert gases and hydrocarbons, limiting applicability. |
High Initial and Operational Costs | Higher upfront and ongoing costs compared to other vacuum pump technologies. |
Need for Periodic Regeneration | Time-consuming and costly process to restore efficiency. |
Limited Lifespan | Frequent use in high-gas-load environments shortens operational life. |
Incompatibility with Oils | Contamination degrades getter material, requiring additional filtration systems. |
Complexity in Integration | Requires careful system design, increasing complexity and cost. |
Environmental and Safety Concerns | Handling and disposal of getter materials pose safety and environmental risks. |
Need help choosing the right vacuum pump for your application? Contact our experts today for personalized advice!