Evaporation is a natural process where a liquid transforms into a gas, but it can pose several hazards depending on the context. These hazards include environmental impacts, health risks, and safety concerns. For instance, evaporation can lead to the release of harmful volatile organic compounds (VOCs) or toxic substances into the air, contributing to air pollution and respiratory issues. In industrial settings, evaporation of flammable or explosive liquids can create fire or explosion risks. Additionally, evaporation can lead to the concentration of hazardous chemicals in residual liquids, posing risks during handling or disposal. Understanding these hazards is crucial for implementing proper safety measures and mitigating risks.
Key Points Explained:
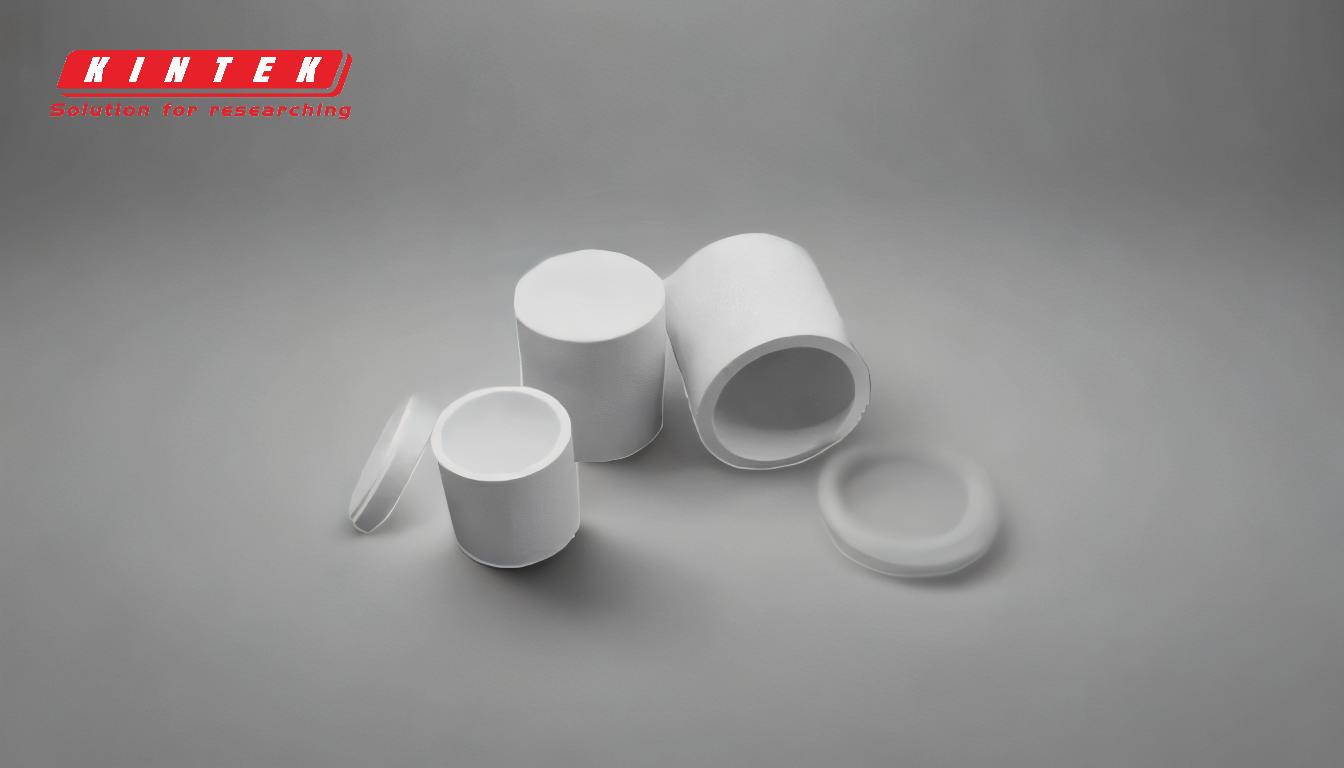
-
Environmental Hazards:
- Air Pollution: Evaporation of volatile substances, such as solvents or chemicals, releases VOCs into the atmosphere. These compounds contribute to smog formation and can harm ecosystems.
- Water Contamination: In some cases, evaporation can concentrate pollutants in water bodies, leading to toxic levels that harm aquatic life.
- Climate Impact: Evaporation of certain substances, like refrigerants, can contribute to greenhouse gas emissions, exacerbating climate change.
-
Health Hazards:
- Inhalation Risks: Evaporated chemicals, especially in confined spaces, can lead to respiratory problems, dizziness, or even long-term health issues like cancer.
- Skin and Eye Irritation: Direct exposure to evaporating liquids, such as acids or solvents, can cause irritation or burns.
- Toxic Exposure: Evaporation of hazardous substances, like mercury or benzene, can result in toxic exposure, leading to severe health complications.
-
Safety Hazards:
- Fire and Explosion Risks: Evaporation of flammable liquids, such as gasoline or alcohol, increases the concentration of vapors in the air, creating a risk of ignition and explosions.
- Chemical Concentration: In industrial processes, evaporation can concentrate hazardous chemicals in residual liquids, making them more dangerous to handle or dispose of.
- Equipment Damage: Evaporation in cooling systems or boilers can lead to scaling or corrosion, reducing equipment lifespan and increasing maintenance costs.
-
Mitigation Strategies:
- Ventilation: Proper ventilation systems can reduce the buildup of harmful vapors in enclosed spaces.
- Containment: Using sealed containers or tanks minimizes the release of evaporating substances into the environment.
- Monitoring and Control: Regular monitoring of evaporation rates and implementing control measures, such as temperature regulation, can mitigate risks.
- Personal Protective Equipment (PPE): Workers should use appropriate PPE, such as respirators and gloves, to protect against exposure to harmful vapors.
By understanding these hazards and implementing appropriate safety measures, the risks associated with evaporation can be effectively managed.
Summary Table:
Hazard Type | Key Risks | Examples |
---|---|---|
Environmental Hazards | Air pollution, water contamination, climate impact | VOCs, smog formation, toxic levels in water, greenhouse gas emissions |
Health Hazards | Inhalation risks, skin/eye irritation, toxic exposure | Respiratory issues, burns, cancer, mercury or benzene exposure |
Safety Hazards | Fire/explosion risks, chemical concentration, equipment damage | Flammable liquids, hazardous residuals, scaling/corrosion in equipment |
Mitigation Strategies | Ventilation, containment, monitoring, PPE | Sealed containers, temperature regulation, respirators, gloves |
Need help managing evaporation risks? Contact our experts today for tailored solutions!