A kiln sitter is a critical component in pottery kilns, designed to automatically shut off the kiln when the desired temperature is reached. It consists of several key parts, including the tube assembly, cone supports, and sensing rod. Some kiln sitters also come with an optional timer. Understanding these components is essential for maintenance, troubleshooting, and replacement, especially for older kilns where individual parts may need replacement rather than the entire unit.
Key Points Explained:
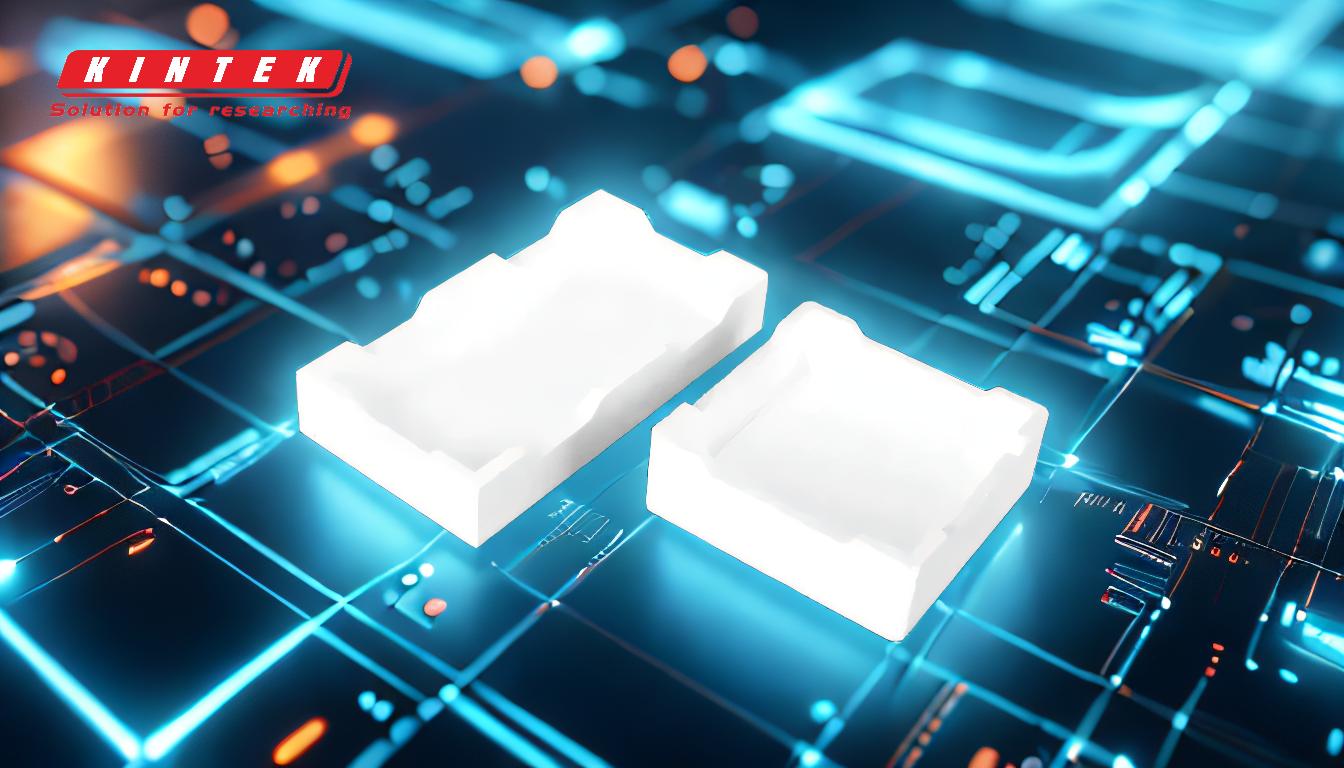
-
Tube Assembly
- The tube assembly is a central part of the kiln sitter, housing the mechanism that detects when the kiln has reached the desired temperature.
- It typically contains a spring-loaded mechanism that interacts with the sensing rod and cone supports.
- Over time, the tube assembly may wear out or become damaged, requiring replacement to ensure proper functionality.
-
Cone Supports
- Cone supports hold the pyrometric cones, which are small ceramic pieces that bend at specific temperatures.
- These cones are chosen based on the firing temperature required for the pottery being fired.
- When the cone bends sufficiently, it triggers the kiln sitter to shut off the kiln.
- Cone supports must be aligned correctly to ensure accurate temperature readings and proper operation.
-
Sensing Rod
- The sensing rod is a metal rod that extends into the kiln chamber and interacts with the pyrometric cone.
- As the cone bends, the sensing rod moves, activating the shut-off mechanism in the tube assembly.
- The rod must be free of obstructions and properly positioned to function correctly.
-
Timer (Optional)
- Some kiln sitters include a timer as an additional feature.
- The timer allows users to set a maximum firing duration, providing an extra layer of safety in case the cone fails to bend or the sensing rod malfunctions.
- This feature is particularly useful for long firings or when using cones that may not bend as predictably.
-
Maintenance and Replacement
- For older kilns, individual components of the kiln sitter (such as the tube assembly, cone supports, or sensing rod) may need replacement rather than the entire unit.
- Regular inspection and maintenance of these parts can extend the lifespan of the kiln sitter and ensure consistent performance.
- Replacing worn or damaged parts promptly can prevent kiln malfunctions and ensure safe operation.
By understanding these components and their functions, users can better maintain their kiln sitters, troubleshoot issues, and make informed decisions about repairs or replacements.
Summary Table:
Component | Function | Maintenance Tips |
---|---|---|
Tube Assembly | Houses the mechanism that detects when the kiln reaches the desired temperature. | Inspect for wear or damage; replace if necessary to ensure proper functionality. |
Cone Supports | Holds pyrometric cones that bend at specific temperatures. | Ensure proper alignment for accurate readings and operation. |
Sensing Rod | Interacts with the pyrometric cone to activate the shut-off mechanism. | Keep free of obstructions and correctly positioned. |
Timer (Optional) | Sets a maximum firing duration for added safety. | Use for long firings or when cones may not bend predictably. |
Maintenance | Regular inspection and replacement of worn parts. | Replace damaged components promptly to prevent malfunctions and ensure safety. |
Need help maintaining or replacing your kiln sitter? Contact our experts today for personalized advice and solutions!