Twin-screw compounding is a critical process in polymer and material science, used to mix, blend, and homogenize materials into a uniform product. The process involves several sequential steps, each contributing to the final quality of the compounded material. These steps include feeding, melting, conveying, mixing, venting, and extrusion. Each stage is carefully controlled to ensure optimal material properties, such as consistency, homogeneity, and performance. Below, the key steps are explained in detail to provide a comprehensive understanding of the twin-screw compounding process.
Key Points Explained:
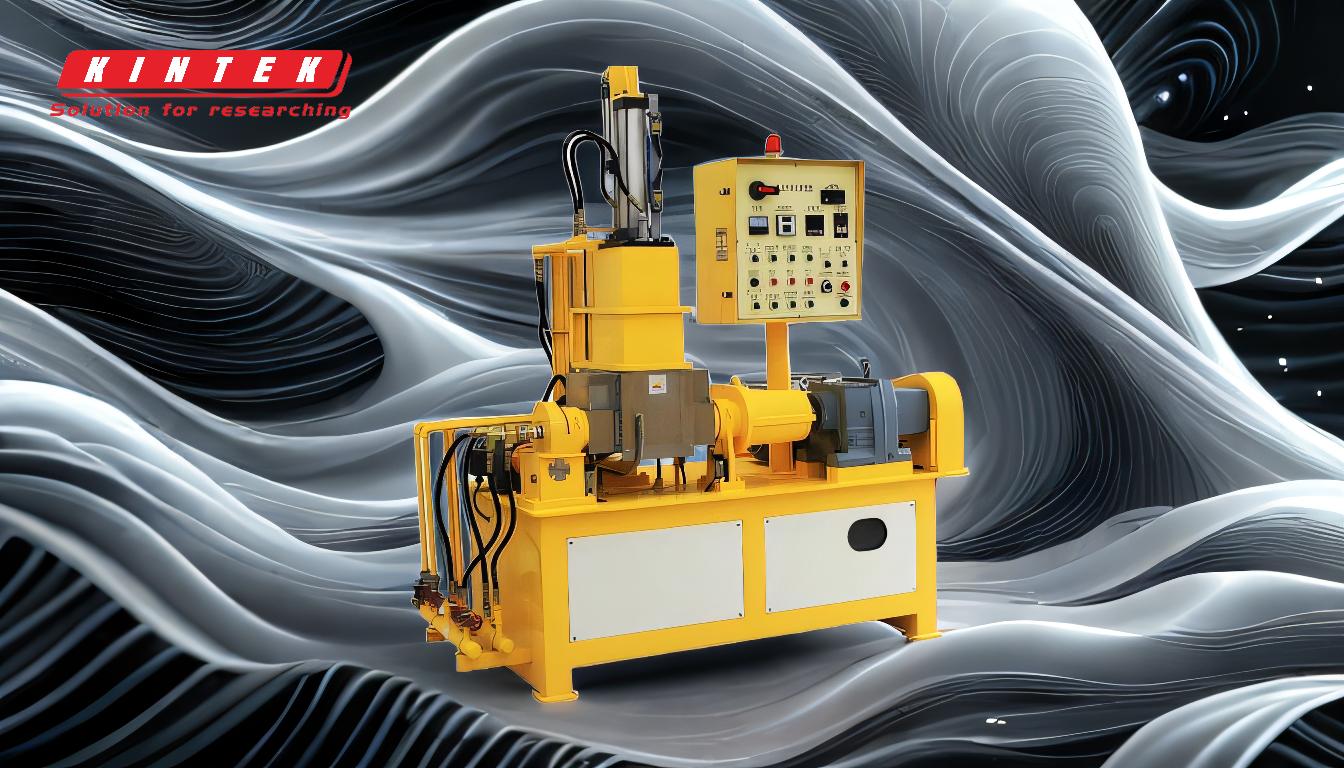
-
Feeding
- Purpose: Introduce raw materials into the twin-screw extruder.
-
Process: Solid materials (polymers, additives, fillers, etc.) are fed into the extruder using volumetric or gravimetric feeders.
- Volumetric feeders measure material by volume, while gravimetric feeders measure by weight, ensuring precise control over the feed rate.
-
Considerations:
- Proper feeding ensures consistent material flow and prevents interruptions in the compounding process.
- Air removal and compaction of low-density materials occur in this zone to prepare the material for subsequent stages.
-
Melting
- Purpose: Convert solid materials into a molten state for easier mixing and processing.
-
Process: The material is heated through barrel heating and mechanical shear generated by the rotating screws.
- The screws are designed with specific geometries to enhance heat transfer and melting efficiency.
-
Considerations:
- Temperature control is critical to avoid thermal degradation of the material.
- The melting zone must ensure complete and uniform melting to achieve a homogeneous mixture.
-
Conveying
- Purpose: Transport the molten material through the extruder.
-
Process: The rotating screws move the material forward along the barrel.
- Screw design (e.g., pitch, flight depth) influences conveying efficiency and material residence time.
-
Considerations:
- Conveying must be consistent to maintain steady material flow and prevent backflow or stagnation.
- Proper screw geometry ensures efficient material transport without excessive energy consumption.
-
Mixing
- Purpose: Achieve a uniform blend of all components (polymers, additives, fillers, etc.).
-
Process: Mixing occurs through distributive and dispersive mechanisms.
- Distributive mixing evenly distributes components throughout the material.
- Dispersive mixing breaks down agglomerates and ensures fine dispersion of additives.
-
Considerations:
- Screw elements (e.g., kneading blocks, mixing elements) are tailored to the specific mixing requirements.
- Mixing intensity and duration must be optimized to achieve the desired material properties without excessive shear stress.
-
Venting
- Purpose: Remove volatile components, moisture, or trapped air from the material.
-
Process: The material passes through a venting zone, where vacuum or atmospheric pressure is applied to extract volatiles.
- Vent ports are strategically placed to ensure effective removal of unwanted components.
-
Considerations:
- Proper venting prevents defects such as bubbles, voids, or poor surface finish in the final product.
- Venting efficiency depends on material viscosity, vent port design, and vacuum level.
-
Extrusion
- Purpose: Form the homogenized material into the desired shape or form.
-
Process: The molten material is forced through a die to create pellets, strands, or profiles.
- The die design determines the final product geometry.
-
Considerations:
- Die pressure and temperature must be controlled to ensure consistent product dimensions and quality.
- Cooling and cutting systems are used downstream to solidify and size the extruded material.
By following these steps, twin-screw compounding ensures the production of high-quality, uniform materials tailored to specific applications. Each stage is interdependent, requiring precise control and optimization to achieve the desired material properties and performance.
Summary Table:
Step | Purpose | Key Considerations |
---|---|---|
Feeding | Introduce raw materials into the extruder. | Ensure consistent flow; remove air and compact low-density materials. |
Melting | Convert solids into a molten state for mixing. | Control temperature to avoid degradation; ensure uniform melting. |
Conveying | Transport molten material through the extruder. | Maintain steady flow; optimize screw geometry for efficiency. |
Mixing | Achieve a uniform blend of components. | Use distributive and dispersive mixing; optimize intensity and duration. |
Venting | Remove volatiles, moisture, or trapped air. | Prevent defects like bubbles; optimize vent port design and vacuum level. |
Extrusion | Form the material into the desired shape or form. | Control die pressure and temperature; ensure consistent product dimensions and quality. |
Ready to optimize your twin-screw compounding process? Contact our experts today for tailored solutions!