The design of a fluidized bed reactor involves a systematic approach to ensure efficient operation, safety, and optimal performance. Key steps include defining the reactor's purpose, selecting appropriate materials and dimensions, determining operating conditions, and incorporating safety measures. The reactor typically consists of two main components: the combustor and the pyrolyser. Design considerations include operating velocity, height, diameter, wall thickness, and the distributor plate, all tailored to the specific density and viscosity of the components at the desired temperature and pressure. Safety features such as maintaining an inert atmosphere, monitoring pressure and level, and controlling wall temperature are critical to prevent explosions and ensure smooth operation.
Key Points Explained:
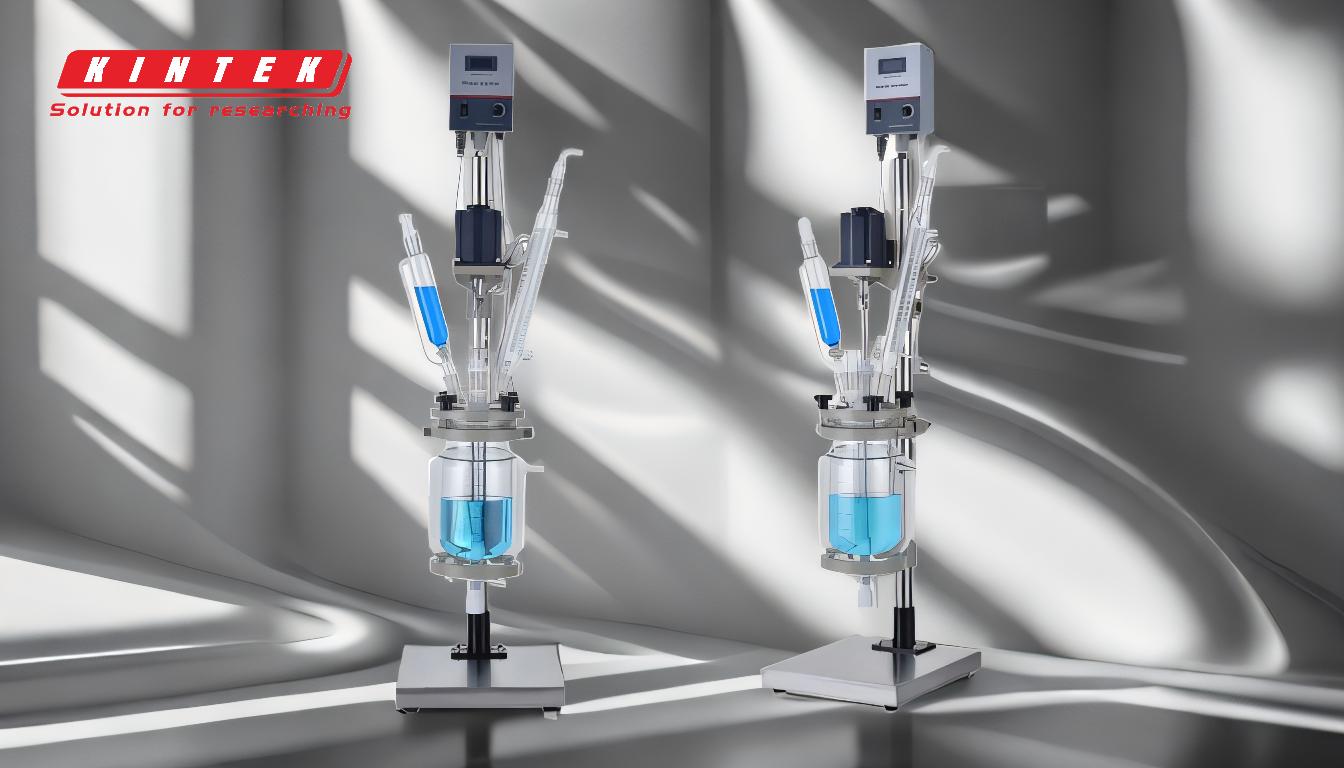
-
Define the Purpose and Requirements:
- The first step in designing a fluidized bed reactor is to clearly define its purpose, such as pyrolysis or combustion. This determines the type of reactor (e.g., bubbling fluidized bed) and the specific requirements for the process, including the desired reaction rates, temperature control, and heat transfer efficiency.
- For pyrolysis, the reactor must ensure high-quality bio-oil production, which requires small biomass particle sizes and efficient heat transfer.
-
Select Bed Material and Fluid:
- The reactor contains a layer of bed material, typically sand, at its bottom. This material plays a crucial role in heat transfer and preventing unwanted reactions.
- A fluid, usually pure nitrogen, is introduced at the bottom to maintain an inert atmosphere, fluidize the particles, and ensure efficient heat transfer.
-
Determine Operating Conditions:
- Operating velocity, height, diameter, and wall thickness are calculated based on the density and viscosity of the components at the specified temperature and pressure (e.g., 101,325 kPa).
- The distributor plate, which supports the bed material, must be designed to ensure uniform fluidization and prevent blockages.
-
Design the Reactor Structure:
- The reactor is divided into two main sections: the combustor and the pyrolyser. Each section must be designed to handle specific reactions and conditions.
- The height and diameter of the reactor are determined by the desired residence time and flow rate of the reactants.
-
Incorporate Safety Measures:
- Safety is a critical aspect of reactor design. Key considerations include maintaining a maximum allowable wall temperature of 55 °C to prevent overheating.
- The absence of oxygen in the pyrolyser is essential to prevent explosions. This is achieved using a para-magnetic sensor to detect oxygen and cleaning the system with inert gas.
- Pressure and level sensors are installed to monitor for blockages or excessive fluidization velocity, ensuring safe and efficient operation.
-
Optimize Heat Transfer and Reaction Efficiency:
- The design must ensure efficient heat transfer to the substrate undergoing pyrolysis. This is achieved through the bed material, which transfers heat effectively.
- The reactor should be designed to achieve high biomass heating rates, which are crucial for generating high-quality bio-oil.
-
Consider Flow Regimes and Fluidization:
- The basic principles of fluidization involve passing a fluid through a solid granular material supported by a distributor plate. At lower velocities, the solids remain stationary, forming a packed bed reactor. As velocity increases, the solids become suspended, leading to fluidization.
- The design must account for various flow regimes depending on the operating conditions and properties of the solid phase.
-
Test and Validate the Design:
- Once the reactor is designed, it must be tested under controlled conditions to validate its performance. This includes checking for uniform fluidization, efficient heat transfer, and safe operation.
- Any necessary adjustments are made based on the test results to ensure the reactor meets the desired specifications.
By following these steps, the design of a fluidized bed reactor can be optimized for efficient and safe operation, ensuring that it meets the specific requirements of the intended process, such as pyrolysis or combustion.
Summary Table:
Key Design Steps | Details |
---|---|
Define Purpose | Determine if the reactor is for pyrolysis or combustion. |
Select Bed Material & Fluid | Use sand for heat transfer and nitrogen for inert atmosphere. |
Operating Conditions | Calculate velocity, height, diameter, and wall thickness for efficiency. |
Safety Measures | Maintain inert atmosphere, monitor pressure, and control wall temperature. |
Heat Transfer Optimization | Ensure efficient heat transfer for high-quality bio-oil production. |
Flow Regimes | Design for fluidization based on solid phase properties. |
Testing & Validation | Test for uniform fluidization, heat transfer, and safe operation. |
Ready to design a fluidized bed reactor tailored to your needs? Contact our experts today for personalized guidance!