A diffusion pump is a type of vacuum pump that operates without moving parts, relying on the vaporization and condensation of a working fluid, typically oil, to create a high vacuum. It works by heating the oil to produce vapor, which then moves upward and is directed downward through spray valves. The vapor captures air molecules and carries them to the pump's base, where they are released. The cooled oil condenses and returns to the reservoir, ready to repeat the cycle. This process achieves a high vacuum with high pumping speed, making diffusion pumps suitable for applications requiring low pressures, such as mass spectrometry, vacuum metallurgy, and surface state physics.
Key Points Explained:
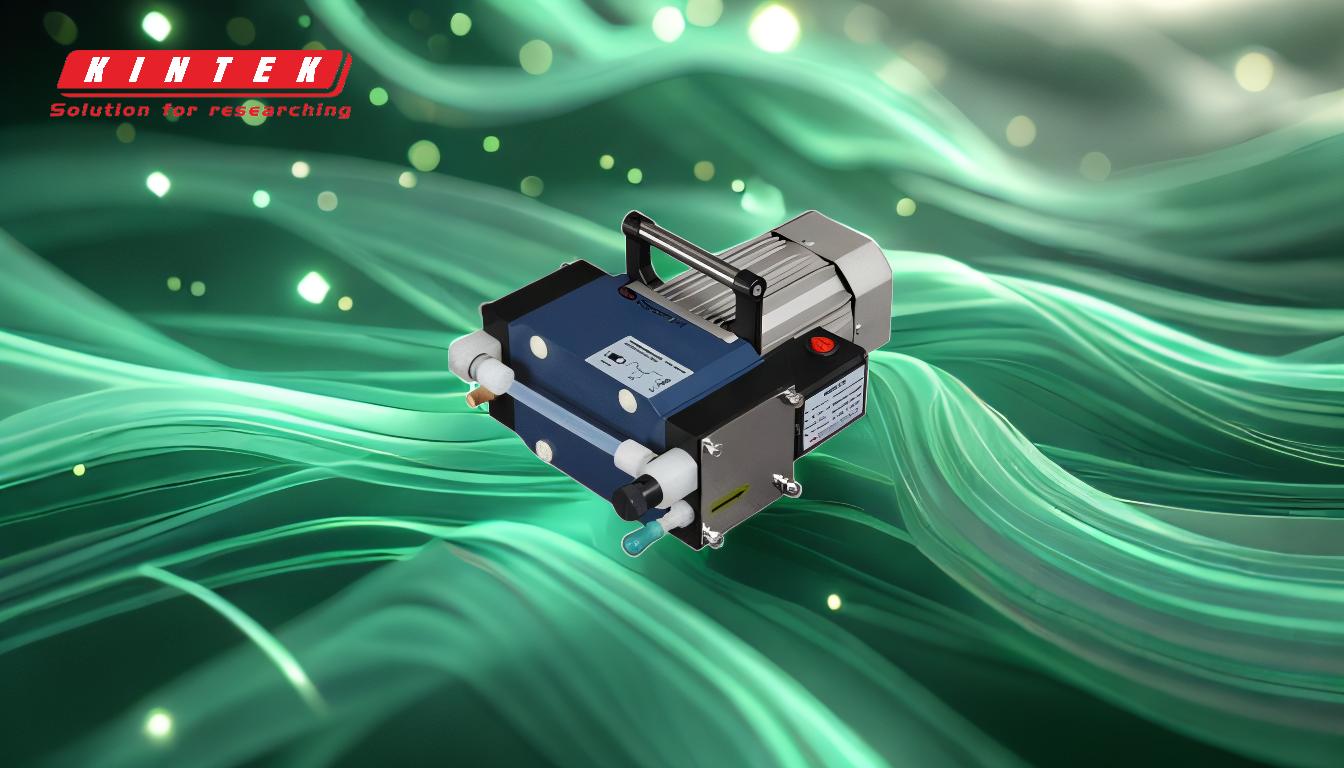
-
No Moving Parts
- Diffusion pumps operate without mechanical components like pistons or lobes, which are common in mechanical pumps.
- This design reduces wear and tear, ensuring long-term reliability and minimal maintenance.
- The absence of moving parts also makes diffusion pumps quieter and less prone to mechanical failure.
-
Working Principle
- The pump uses a working fluid, typically oil, which is heated to produce vapor.
- The vapor rises and is directed downward through spray valves or jets.
- As the vapor moves downward, it captures air molecules and carries them to the base of the pump.
- The vapor condenses on the water-cooled walls, releasing the trapped air molecules.
- The condensed oil returns to the reservoir, ready to be heated and vaporized again.
-
High Vacuum Creation
- The differential pressure between the top and bottom of the pump creates a high vacuum in the connected chamber.
- This process is highly efficient, achieving pressures as low as 10⁻³ to 10⁻⁴ mbar, which is essential for applications like mass spectrometry and surface state physics.
- The high pumping speed ensures rapid evacuation of air molecules, making diffusion pumps ideal for processes requiring fast vacuum creation.
-
Cooling Mechanism
- The pump's exterior is equipped with cooling coils or water-cooled walls to condense the oil vapor.
- Cooling ensures the vapor transitions back to liquid form, allowing it to flow back into the reservoir.
- This cooling process is critical for maintaining the pump's efficiency and preventing overheating.
-
Applications
- Diffusion pumps are used in fields requiring high or ultrahigh vacuum levels, such as:
- Laboratories: For experiments requiring precise vacuum conditions.
- Medical and Pharmaceutical Industries: For processes like freeze-drying and sterilization.
- Mass Spectrometry: For analyzing chemical compounds.
- Vacuum Metallurgy: For processes like vacuum melting and sintering.
- Surface State Physics: For studying material surfaces at atomic levels.
- Diffusion pumps are used in fields requiring high or ultrahigh vacuum levels, such as:
-
Advantages Over Mechanical Pumps
- Higher Vacuum Levels: Diffusion pumps can achieve much lower pressures compared to mechanical pumps.
- Greater Pumping Speed: They evacuate air molecules more quickly, making them suitable for time-sensitive processes.
- Quieter Operation: The absence of moving parts results in quieter performance.
- Lower Maintenance: Fewer mechanical components mean less frequent maintenance and longer operational life.
-
Limitations
- Oil Contamination: A small amount of oil molecules may remain in the vacuum chamber, which can be problematic for ultra-sensitive applications.
- Heat Generation: The heating process requires energy and can lead to thermal management challenges.
- Pre-Vacuum Requirement: Diffusion pumps typically require a pre-vacuum pump to reduce the initial pressure before they can operate effectively.
-
Key Components
- Boilerplate: Heats the oil to produce vapor.
- Spray Valves or Jets: Direct the vapor downward to capture air molecules.
- Cooling Coils or Walls: Condense the vapor back into liquid oil.
- Reservoir: Stores the condensed oil for reuse in the cycle.
By understanding these key points, a purchaser can evaluate whether a diffusion pump is suitable for their specific application, considering factors like required vacuum levels, pumping speed, and operational environment.
Summary Table:
Feature | Description |
---|---|
No Moving Parts | Operates without mechanical components, ensuring reliability and low maintenance. |
Working Principle | Uses oil vaporization and condensation to capture and remove air molecules. |
High Vacuum Creation | Achieves pressures as low as 10⁻³ to 10⁻⁴ mbar, ideal for sensitive applications. |
Cooling Mechanism | Water-cooled walls condense vapor, maintaining efficiency and preventing overheating. |
Applications | Used in labs, medical/pharmaceutical industries, mass spectrometry, and more. |
Advantages | Higher vacuum levels, faster pumping speed, quieter operation, and lower maintenance. |
Limitations | Potential oil contamination, heat generation, and pre-vacuum requirement. |
Key Components | Boilerplate, spray valves, cooling coils, and reservoir. |
Ready to enhance your vacuum processes? Contact us today to find the perfect diffusion pump for your needs!