A fluidized bed reactor (FBR) is a versatile and efficient device used in chemical and industrial processes to carry out multiphase reactions. It operates by passing a fluid (gas or liquid) through a solid granular material, typically a catalyst, at high velocities, causing the solid particles to suspend and behave like a fluid. This fluidization process enhances heat and mass transfer, ensuring uniform mixing and temperature distribution, which are critical for consistent product quality. FBRs are widely used in industries such as petroleum, chemical, and biomass processing due to their ability to handle particulate substrates efficiently and produce high yields of byproducts like bio-oils and gases.
Key Points Explained:
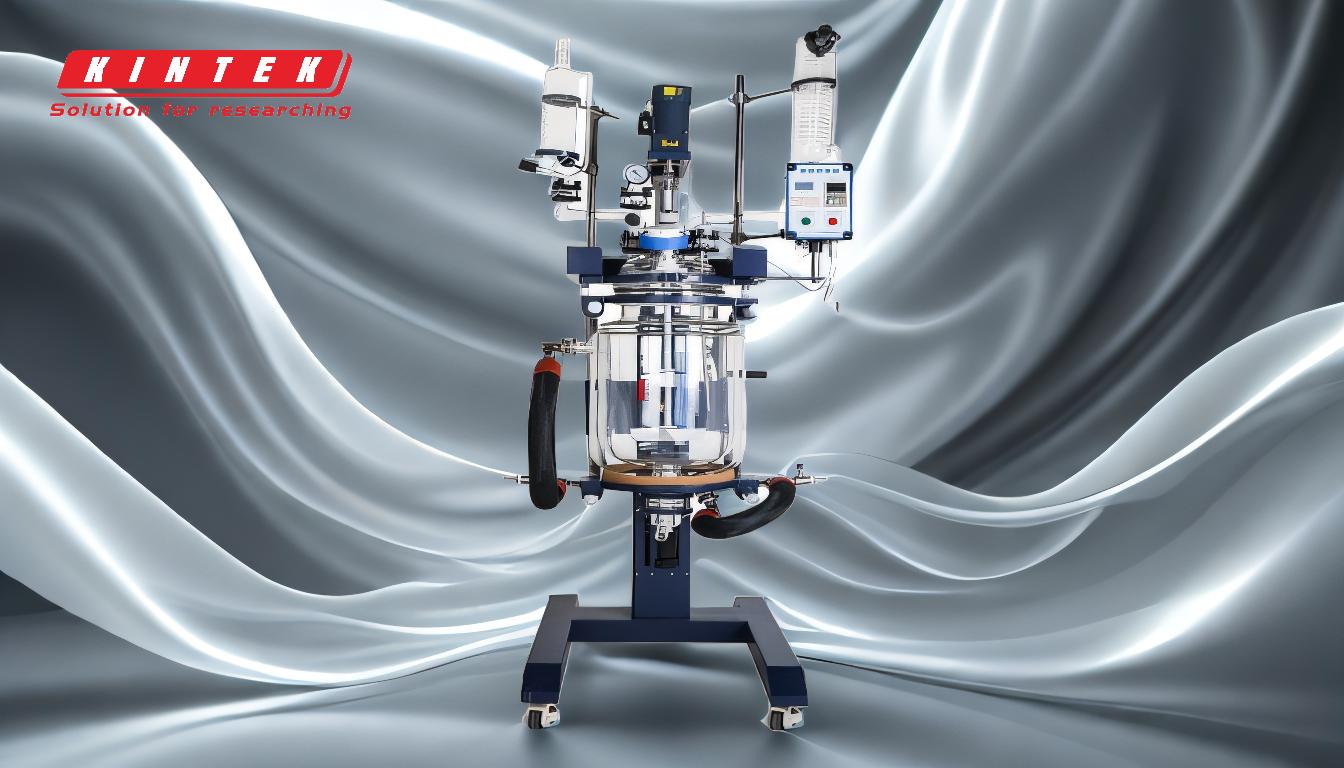
-
Definition and Working Principle:
- A fluidized bed reactor (FBR) is designed for multiphase chemical reactions, where a fluid (gas or liquid) is passed through a solid granular material (usually a catalyst) at high speeds.
- This process, called fluidization, suspends the solid particles, making them behave like a fluid. This enhances interaction between the fluid and solid phases, improving reaction efficiency.
-
Components of a Fluidized Bed Reactor:
- Solid Substrate Material: Typically a catalyst, which facilitates the chemical reaction.
- Porous Distributor Plate: Supports the solid material and allows the fluid to pass through uniformly.
- Fluid Flow: At lower velocities, the solids remain stationary (packed bed reactor). At higher velocities, the solids become fluidized, creating a dynamic and efficient reaction environment.
-
Advantages of Fluidized Bed Reactors:
- Uniform Mixing: Eliminates poor mixing, ensuring a consistent product quality.
- Uniform Temperature Gradients: Prevents local hot or cold spots, which can degrade products or cause inefficiencies.
- Continuous Operation: Allows for efficient production by continuously withdrawing products and introducing new reactants.
- Enhanced Heat Transfer: Approximately 90% of heat transfer occurs through conduction, with the remainder through convection, ensuring efficient thermal management.
-
Industrial Applications:
- Biomass Processing: Effective for particulate substrates like woody biomass, increasing yields of bio-oils and gases.
- Petroleum and Chemical Industries: Used for catalytic cracking, gasification, and other chemical processes due to their efficiency and scalability.
-
Challenges and Considerations:
- Attrition: Fluidization can cause erosion of the biomass and catalyst surfaces, exposing fresh material for reaction but also leading to wear and tear.
- Micro Carbon Formation: A small amount of micro carbon may form during reactions, though this is minimal compared to other reactor types.
-
Comparison with Other Reactors:
- FBRs outperform packed bed reactors in terms of mixing efficiency, heat transfer, and scalability.
- They are particularly advantageous for processes requiring uniform temperature distribution and continuous operation.
By leveraging the unique properties of fluidization, fluidized bed reactors offer a robust solution for a wide range of industrial applications, ensuring high efficiency, consistent product quality, and operational flexibility.
Summary Table:
Key Aspect | Details |
---|---|
Definition | Device for multiphase reactions using fluidization to suspend solid particles. |
Components | Solid substrate (catalyst), porous distributor plate, fluid flow. |
Advantages | Uniform mixing, temperature gradients, continuous operation, enhanced heat transfer. |
Applications | Biomass processing, petroleum, chemical industries. |
Challenges | Attrition, micro carbon formation. |
Comparison | Outperforms packed bed reactors in efficiency and scalability. |
Unlock the potential of fluidized bed reactors for your industrial processes—contact our experts today!