Mold design is a specialized field within manufacturing and engineering that focuses on creating molds used in the production of various products. It involves the digital design of molds, such as cavity molds and cold stamping dies, leveraging advanced tools to enhance design quality and efficiency. Mold designers apply both traditional and modern techniques to ensure that molds meet precise specifications, enabling the mass production of components with consistent quality. This process is critical in industries like automotive, consumer goods, and electronics, where molds are used to shape materials into desired forms.
Key Points Explained:
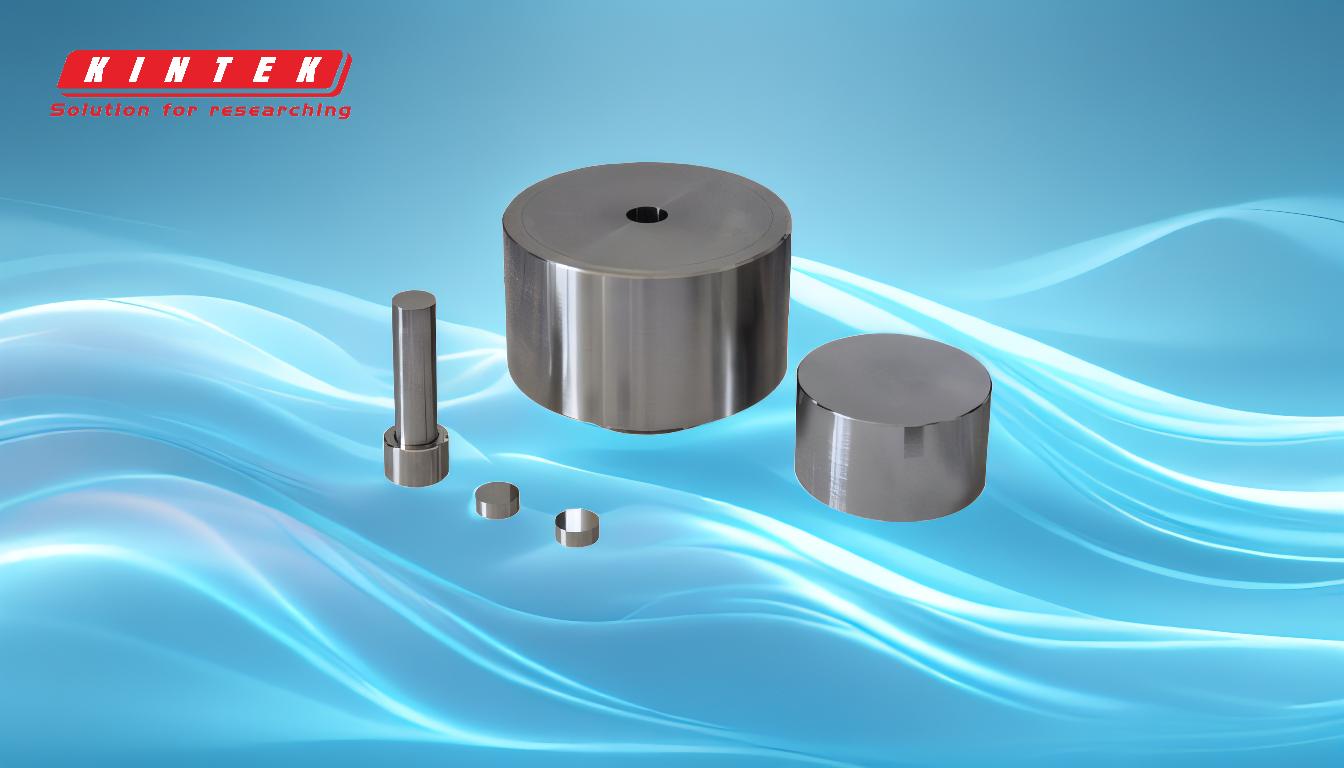
-
Definition of Mold Design:
- Mold design is the process of creating digital designs for molds, which are tools used to shape materials into specific forms during manufacturing.
- It includes the design of cavity molds (used for injection molding) and cold stamping dies (used for metal forming).
-
Role of Mold Designers:
- Mold designers are professionals who specialize in creating detailed digital models of molds.
- They ensure that molds are designed to meet the exact requirements of the production process, including dimensions, material flow, and cooling systems.
-
Digital Design Tools:
- Modern mold design heavily relies on digital tools such as CAD (Computer-Aided Design) software.
- These tools allow designers to create precise 3D models, simulate material behavior, and optimize mold performance before manufacturing begins.
-
Improving Design Quality:
- Digital tools enable designers to identify and resolve potential issues early in the design phase.
- This reduces errors, improves the accuracy of the mold, and ensures that the final product meets quality standards.
-
Shortening Design Cycles:
- By using digital tools, mold designers can streamline the design process, reducing the time required to develop and test molds.
- Faster design cycles lead to quicker production timelines and reduced costs for manufacturers.
-
Applications in Industry:
- Mold design is essential in industries that rely on mass production, such as automotive, consumer goods, and electronics.
- It enables the efficient production of complex parts with consistent quality and precision.
-
Integration of Traditional and Modern Techniques:
- While digital tools are central to modern mold design, traditional techniques and principles still play a role.
- Designers combine their knowledge of materials, manufacturing processes, and engineering principles with advanced software to create effective molds.
-
Importance in Manufacturing:
- High-quality mold design is critical for ensuring the efficiency and reliability of manufacturing processes.
- It directly impacts the cost, speed, and quality of production, making it a key focus area for manufacturers.
By understanding these key points, equipment and consumable purchasers can better appreciate the importance of mold design in the manufacturing process and make informed decisions when sourcing molds or related services.
Summary Table:
Aspect | Description |
---|---|
Definition | Digital design of molds for shaping materials in manufacturing. |
Role of Designers | Create precise molds meeting production requirements using digital tools. |
Digital Tools | CAD software for 3D modeling, simulation, and optimization. |
Design Quality | Early issue resolution ensures accurate molds and high-quality products. |
Design Cycles | Streamlined processes reduce time and costs for faster production. |
Industry Applications | Essential in automotive, consumer goods, and electronics for mass production. |
Techniques | Combines traditional knowledge with modern digital tools for effective designs. |
Manufacturing Impact | Ensures efficiency, reliability, and cost-effectiveness in production. |
Optimize your manufacturing process with expert mold design—contact us today!