Plasma sputtering is a sophisticated physical vapor deposition (PVD) technique used to create thin films on substrates by bombarding a target material with high-energy ions, typically argon, in a vacuum environment. This process involves the ionization of inert gas atoms, which are then accelerated towards a negatively charged target material. The collision between the ions and the target causes atoms from the target to be ejected and deposited onto a substrate, forming a thin, uniform coating. Plasma sputtering is widely used in various industries, including semiconductor manufacturing, optical coatings, and tool coatings, due to its ability to produce precise and high-quality films.
Key Points Explained:
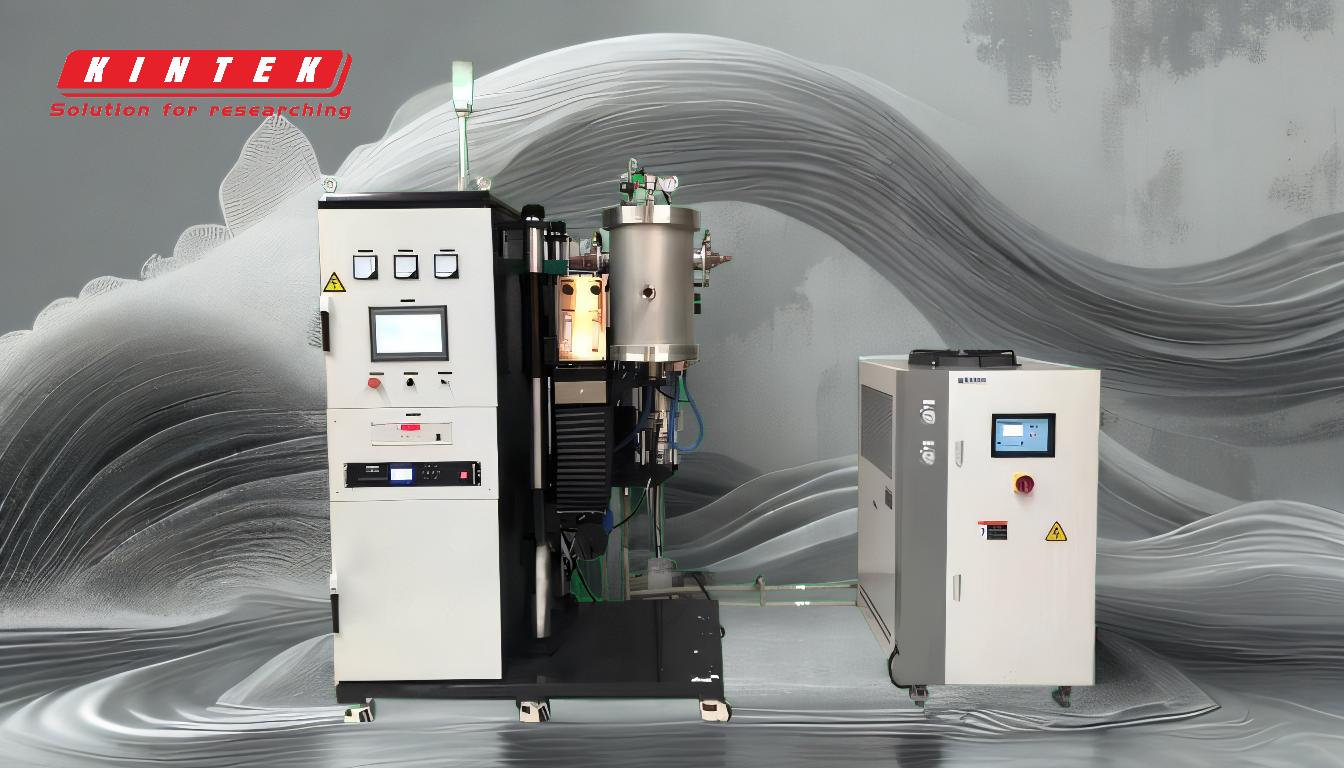
-
Basic Mechanism of Plasma Sputtering:
- Plasma sputtering involves the use of a vacuum chamber where argon gas is ionized to form plasma.
- The target material, which is the source of the coating, is connected to a negatively charged cathode.
- The substrate, where the coating is to be deposited, is connected to a positively charged anode.
- Free electrons in the plasma collide with argon atoms, ionizing them and creating positively charged argon ions.
- These ions are then accelerated towards the target material due to the electrical field, causing atoms from the target to be ejected.
-
Energy Transfer and Ejection of Target Atoms:
- When the high-energy argon ions collide with the target material, they transfer their kinetic energy to the target atoms.
- This energy transfer causes the target atoms to be ejected from the surface in a process known as sputtering.
- The ejected atoms travel through the vacuum chamber and eventually condense on the substrate, forming a thin film.
-
Deposition of Thin Films:
- The ejected target atoms diffuse through the vacuum chamber and deposit onto the substrate.
- The deposition process results in a thin, uniform coating that adheres strongly to the substrate at an atomic level.
- This method is capable of producing films with precise thickness and composition, making it ideal for applications requiring high accuracy.
-
Applications of Plasma Sputtering:
- Semiconductor Manufacturing: Used in the production of integrated circuits and other microelectronic components.
- Optical Coatings: Applied to create anti-reflective or high-emissivity films on glass.
- Tool Coatings: Enhances the durability and performance of cutting tools.
- Data Storage: Used in the production of CD/DVD coatings.
-
Advantages of Plasma Sputtering:
- Precision and Uniformity: The process allows for the deposition of very thin and uniform films, essential for high-performance applications.
- Versatility: Can be used with a wide range of target materials, including metals, alloys, and ceramics.
- Strong Adhesion: The high-energy impact of the target atoms ensures strong bonding with the substrate, resulting in durable coatings.
-
Challenges and Considerations:
- Heat Management: The process generates significant heat, requiring specialized cooling systems to maintain optimal conditions.
- Vacuum Requirements: The need for a high-vacuum environment can increase the complexity and cost of the equipment.
- Target Erosion: Continuous bombardment of the target material leads to its erosion, necessitating periodic replacement.
Plasma sputtering is a highly effective and versatile technique for depositing thin films with exceptional precision and quality. Its applications span across various industries, making it a critical process in modern manufacturing and technology development.
Summary Table:
Aspect | Details |
---|---|
Mechanism | Ionization of argon gas in a vacuum chamber to eject target material atoms. |
Applications | Semiconductor manufacturing, optical coatings, tool coatings, data storage. |
Advantages | Precision, uniformity, versatility, and strong adhesion. |
Challenges | Heat management, vacuum requirements, and target erosion. |
Interested in plasma sputtering for your applications? Contact our experts today to learn more!