Sieve screening is a fundamental method used to analyze and separate particles based on their size, primarily through the use of test sieves. This technique is widely applied across industries such as food, pharmaceuticals, agriculture, and mining for quality control, particle size distribution analysis, and material separation. Test sieves, often used individually or stacked in a sieve shaker, allow particles to be sorted by passing through mesh screens of varying sizes. Smaller particles pass through the mesh, while larger ones are retained, enabling precise classification of materials. This process ensures consistency in particle size, which is critical for product performance and quality in various applications.
Key Points Explained:
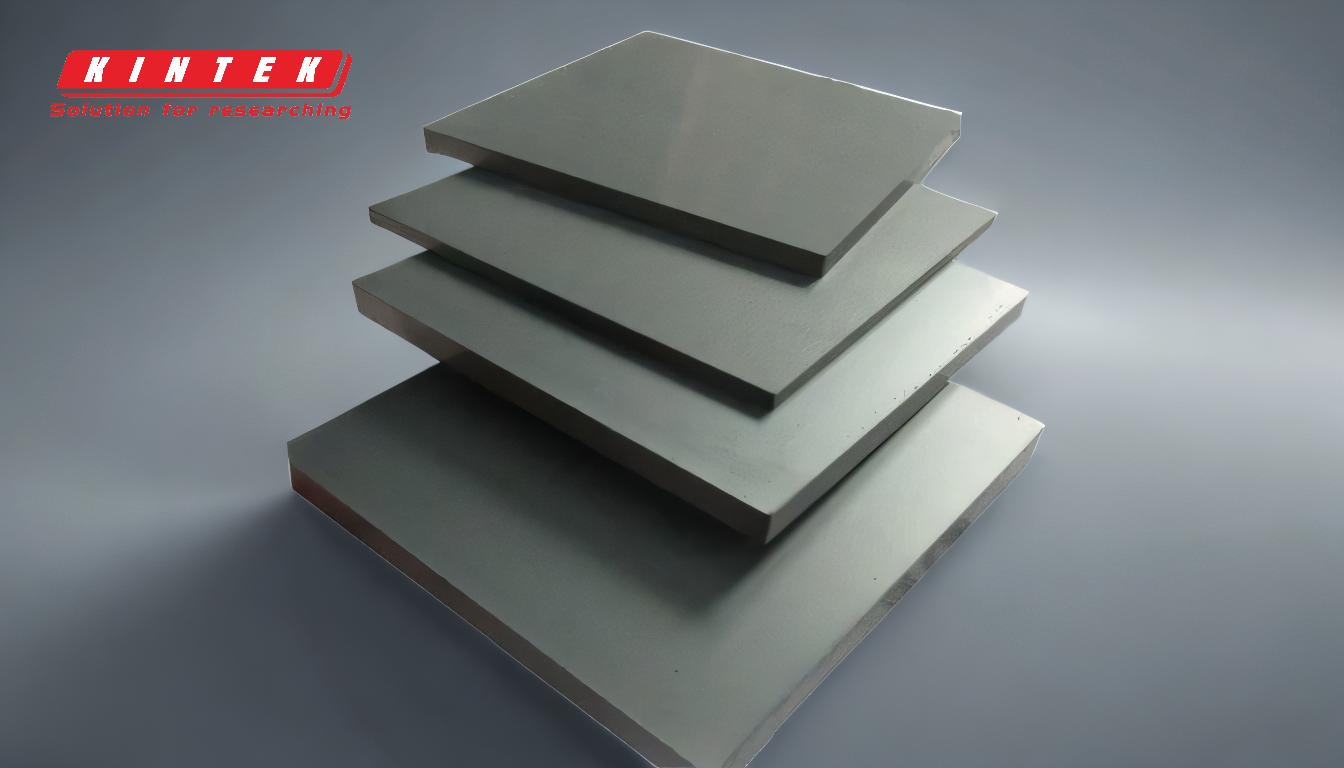
-
Definition and Purpose of Sieve Screening
- Sieve screening is a particle analysis method that separates materials based on particle size using test sieves.
- It is a centuries-old technique used for quality control, ensuring that materials meet specific size and consistency requirements.
- The primary purpose is to determine particle size distribution, analyze impurities, and measure solid content in liquids.
-
How Sieve Screening Works
- Test sieves consist of wire mesh screens with precise openings of varying sizes.
- Particles are placed on the top sieve of a stack, and agitation (often using a sieve shaker) causes smaller particles to pass through the mesh, while larger particles are retained.
- Each sieve in the stack has a progressively smaller mesh size, allowing particles to be sorted into different size fractions.
-
Applications of Sieve Screening
- Particle Size Distribution Analysis: Used to determine the range of particle sizes in a sample, which is critical for product consistency.
- Quality Control: Ensures materials meet specified size standards, which is essential for industries like food, pharmaceuticals, and construction.
- Material Separation: Separates materials into different size fractions for further processing or analysis.
- Soil and Powder Analysis: Commonly used in soil testing and powder processing to classify materials.
-
Types of Materials Analyzed
- Sieve screening is versatile and can handle a wide range of materials, including:
- Powders (e.g., flour, pharmaceuticals)
- Aggregates (e.g., sand, gravel)
- Seeds and agricultural products
- Mining materials (e.g., ores, minerals)
- Sieve screening is versatile and can handle a wide range of materials, including:
-
Equipment Used in Sieve Screening
- Test Sieves: Mesh screens with standardized openings, often stacked for multi-level separation.
- Sieve Shakers: Devices that agitate the sieves to facilitate particle separation. They can handle both dry and wet materials, depending on the application.
- Wet Sieve Analysis: Used for materials that require dispersion in liquid to achieve accurate separation.
-
Importance of Sieve Screening in Industry
- Ensures uniformity in particle size, which is critical for product performance and quality.
- Helps manufacturers maintain compliance with industry standards and regulations.
- Provides valuable data for research and development, enabling the optimization of production processes.
-
Advantages of Sieve Screening
- Simple and cost-effective method for particle analysis.
- Provides accurate and repeatable results when performed correctly.
- Suitable for a wide range of materials and particle sizes.
-
Limitations of Sieve Screening
- Limited to particles larger than the mesh size of the finest sieve (typically around 20 µm).
- May not be suitable for materials that are prone to clumping or agglomeration.
- Wet sieve analysis requires additional steps and may not be applicable to all materials.
-
Best Practices for Effective Sieve Screening
- Use sieves with appropriate mesh sizes for the material being analyzed.
- Ensure proper sample preparation to avoid clumping or uneven distribution.
- Calibrate and maintain sieves regularly to ensure accurate results.
- Follow standardized procedures to achieve consistent and reliable outcomes.
In summary, sieve screening is a vital tool for particle analysis and material separation, offering a straightforward and effective way to ensure product quality and consistency across various industries. By understanding its principles, applications, and best practices, manufacturers and researchers can optimize their processes and achieve better outcomes.
Summary Table:
Aspect | Details |
---|---|
Purpose | Separates particles by size for quality control and material analysis. |
How It Works | Particles pass through mesh screens of varying sizes using test sieves. |
Applications | Particle size distribution, quality control, material separation. |
Materials Analyzed | Powders, aggregates, seeds, mining materials. |
Equipment | Test sieves, sieve shakers, wet sieve analysis tools. |
Advantages | Cost-effective, accurate, and versatile for various materials. |
Limitations | Limited to particles >20 µm; not ideal for clumping materials. |
Best Practices | Use appropriate mesh sizes, prepare samples properly, and maintain sieves. |
Optimize your particle analysis process with sieve screening—contact our experts today for tailored solutions!