Sputtering is a versatile and widely used technique in various industries, primarily for depositing thin films of materials onto substrates. It is a key process in the creation of semiconductors, computer chips, and advanced materials. Sputtering is also employed in surface cleaning, chemical composition analysis, and the production of durable, lightweight, and high-performance coatings. Industries such as electronics, optics, aerospace, medicine, and architecture benefit from sputtering for applications ranging from circuit boards and solar cells to medical implants and energy-efficient window coatings. The process involves ejecting atoms from a target material in a vacuum chamber, which then form a thin film on a substrate, making it essential for modern technology and material science.
Key Points Explained:
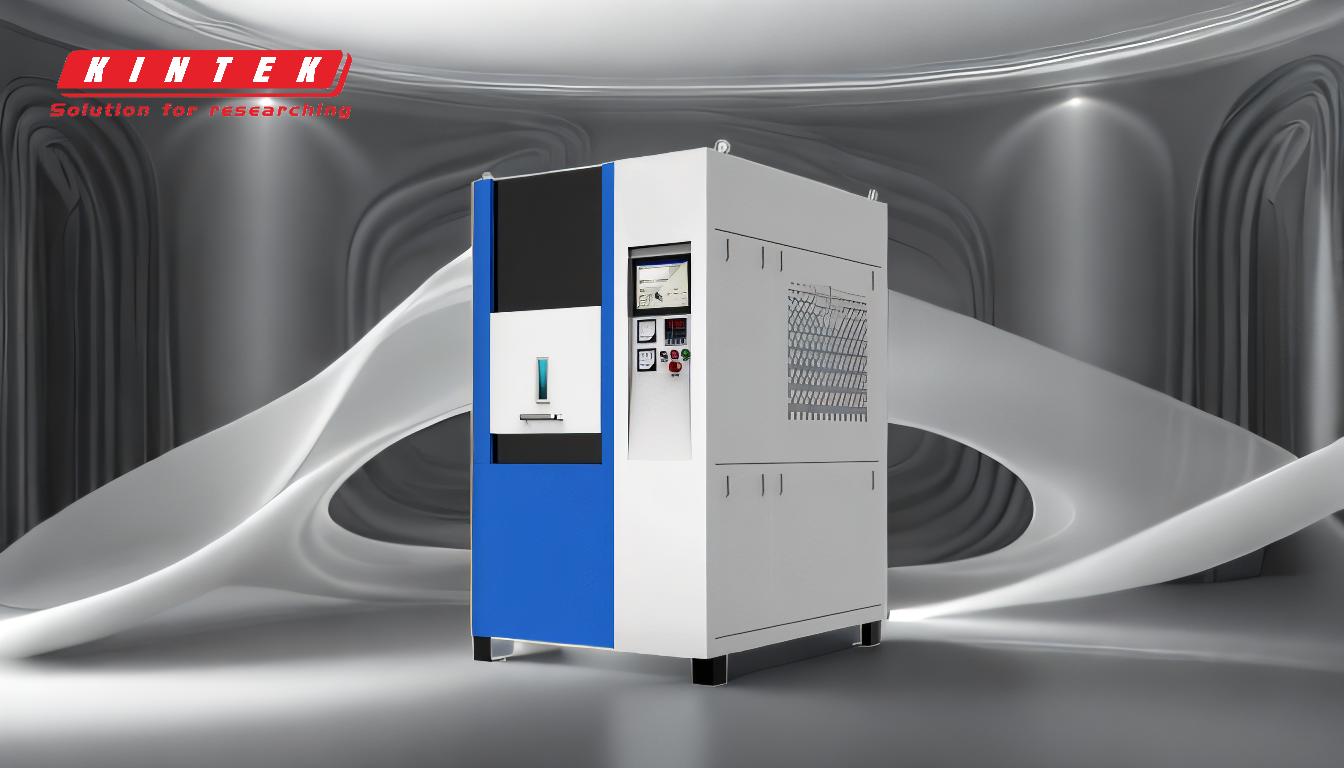
-
Semiconductor and Computer Chip Manufacturing:
- Sputtering is a critical technique in the production of semiconductors and computer chips. It is used to deposit thin films of conductive and insulating materials onto silicon wafers, which are essential for the functionality of integrated circuits.
- The process allows for precise control over the thickness and composition of the films, ensuring high performance and reliability in electronic devices.
-
Thin Film Deposition:
- One of the primary applications of sputtering is the deposition of thin films, which can range from a few nanometers to several micrometers in thickness. These films are used in various industries for coatings, protective layers, and functional surfaces.
- The process involves bombarding a target material with high-energy ions, causing atoms to be ejected and deposited onto a substrate in a vacuum chamber.
-
Advanced Materials and Coatings:
- Sputtering is used to develop advanced materials and coatings that are smaller, lighter, and more durable. This is particularly important in industries such as aerospace, where materials must withstand extreme conditions.
- The technique allows for the creation of alloys and composite materials with tailored properties, such as increased hardness, corrosion resistance, or thermal stability.
-
Electronics Industry:
- In the electronics industry, sputtering is commonly used to apply conductive coatings, such as gold, to circuit boards and other components. Gold's excellent conductivity makes it ideal for ensuring reliable electrical connections.
- Sputtering is also used in the production of optical devices, solar cells, and other electronic components that require precise and uniform coatings.
-
Medical and Life Sciences:
- Sputtering is employed in the medical field to create biocompatible coatings for medical implants and devices. These coatings can improve the performance and longevity of implants by reducing wear and preventing corrosion.
- The technique is also used in life sciences for applications such as preparing specimens for scanning electron microscopy, where a thin conductive coating is necessary for visibility under the microscope.
-
Optics and Architecture:
- In the optics industry, sputtering is used to create reflective and anti-reflective coatings on lenses, mirrors, and other optical components. These coatings enhance the performance of optical devices by improving light transmission and reducing glare.
- In architecture, sputtering is used to apply energy-efficient coatings to windows, which can reduce heat loss and improve insulation in buildings.
-
Surface Cleaning and Analysis:
- Sputtering is used in surface physics as a method for cleaning and preparing high-purity surfaces. This is essential for research and development in materials science, where contamination can affect experimental results.
- The technique is also used for analyzing the chemical composition of surfaces, providing valuable information about the structure and properties of materials.
-
Versatility and Precision:
- Sputtering is a highly versatile technique that can be used with a wide range of materials, including metals, alloys, and ceramics. This allows for the creation of thin films with specific properties tailored to the needs of different applications.
- The precision of the sputtering process ensures that coatings are uniform and consistent, which is critical for the performance and reliability of the final product.
In summary, sputtering is a fundamental process in modern technology and material science, with applications spanning from semiconductor manufacturing to medical devices and architectural coatings. Its ability to deposit thin films with precision and control makes it indispensable in the development of advanced materials and high-performance products.
Summary Table:
Application | Key Benefits |
---|---|
Semiconductor Manufacturing | Precise control of film thickness and composition for high-performance devices |
Thin Film Deposition | Uniform coatings for protective layers and functional surfaces |
Advanced Materials & Coatings | Durable, lightweight, and corrosion-resistant materials for extreme conditions |
Electronics Industry | Conductive coatings (e.g., gold) for reliable electrical connections |
Medical & Life Sciences | Biocompatible coatings for implants and specimen preparation |
Optics & Architecture | Reflective and energy-efficient coatings for lenses and windows |
Surface Cleaning & Analysis | High-purity surface preparation and chemical composition analysis |
Versatility & Precision | Tailored thin films for diverse applications with consistent quality |
Learn how sputtering can enhance your industry's capabilities—contact our experts today!