Chemical reactors and bioreactors are both vessels designed to facilitate chemical reactions, but they differ significantly in their applications, design, and operational requirements. Chemical reactors are used for industrial chemical processes, often involving high temperatures, pressures, and synthetic catalysts. Bioreactors, on the other hand, are specialized for biological processes, such as fermentation or cell culture, and are designed to maintain optimal conditions for living organisms, including temperature, pH, and oxygen levels. The key differences lie in their purpose, the nature of the reactions they facilitate, and the environmental conditions they maintain.
Key Points Explained:
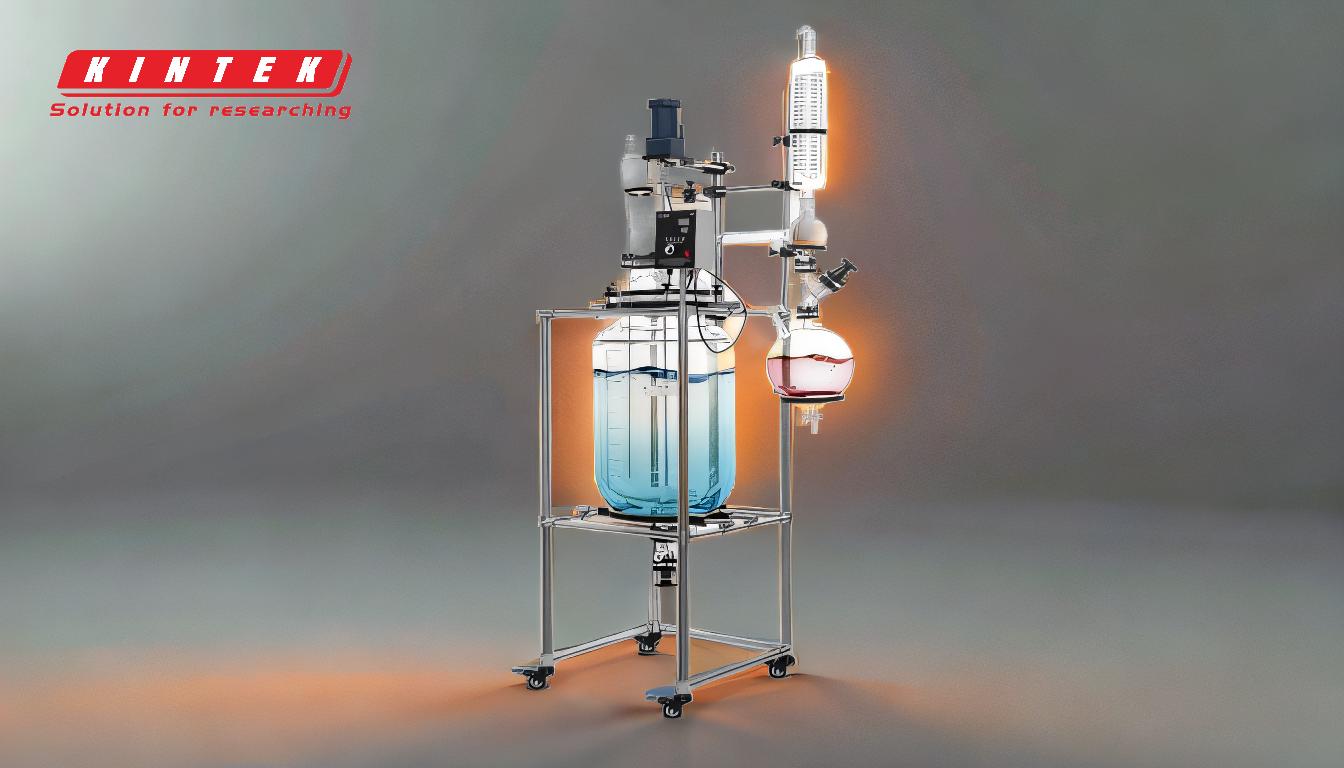
-
Purpose and Application:
- Chemical Reactor: Primarily used for industrial chemical synthesis, such as producing polymers, fuels, or pharmaceuticals. These reactors handle non-living chemical processes, often involving harsh conditions like high temperatures and pressures.
- Bioreactor: Designed for biological processes, such as growing microorganisms, animal cells, or plant cells. Applications include fermentation (e.g., beer, yogurt), biopharmaceutical production (e.g., vaccines, monoclonal antibodies), and wastewater treatment.
-
Nature of Reactions:
- Chemical Reactor: Facilitates chemical reactions involving inorganic or organic compounds, often using synthetic catalysts. Reactions are typically faster and can be highly exothermic or endothermic.
- Bioreactor: Supports biological reactions mediated by living organisms (e.g., bacteria, yeast, mammalian cells). These reactions are generally slower and require precise control of environmental conditions to sustain life.
-
Design and Components:
- Chemical Reactor: Built to withstand extreme conditions, such as high pressures and temperatures. Common types include batch reactors, continuous stirred-tank reactors (CSTRs), and plug-flow reactors. Materials are often corrosion-resistant metals or alloys.
- Bioreactor: Designed to maintain sterile conditions and provide optimal growth environments for living organisms. Features include temperature control, pH monitoring, and aeration systems. Common types include stirred-tank bioreactors, airlift bioreactors, and photobioreactors. Materials are often glass or stainless steel with biocompatible coatings.
-
Environmental Control:
- Chemical Reactor: Focuses on controlling reaction kinetics, heat transfer, and pressure. Temperature and pressure are often manipulated to optimize reaction rates and yields.
- Bioreactor: Requires precise control of biological parameters, such as temperature, pH, dissolved oxygen, and nutrient levels. Sterility is critical to prevent contamination by unwanted microorganisms.
-
Scale-Up Considerations:
- Chemical Reactor: Scale-up is often straightforward, relying on principles of chemical engineering, such as maintaining similar reaction conditions and mixing efficiency.
- Bioreactor: Scale-up is more complex due to the sensitivity of living organisms. Factors like oxygen transfer, shear stress, and nutrient distribution must be carefully managed to avoid compromising cell viability.
-
Examples of Use:
- Chemical Reactor: Producing ammonia via the Haber process, synthesizing polyethylene in petrochemical plants, or manufacturing sulfuric acid.
- Bioreactor: Cultivating yeast for beer production, growing mammalian cells for monoclonal antibody production, or treating wastewater using microbial consortia.
In summary, while both chemical reactors and bioreactors are essential for industrial processes, their differences stem from the nature of the reactions they facilitate and the conditions they must maintain. Chemical reactors are optimized for synthetic chemical processes, whereas bioreactors are tailored for biological systems, requiring careful control of living organisms' growth conditions.
Summary Table:
Aspect | Chemical Reactor | Bioreactor |
---|---|---|
Purpose | Industrial chemical synthesis (e.g., polymers, fuels, pharmaceuticals) | Biological processes (e.g., fermentation, cell culture, biopharmaceuticals) |
Nature of Reactions | Inorganic/organic compounds, synthetic catalysts, faster reactions | Living organisms, slower reactions, precise environmental control |
Design | High pressure/temperature resistance, corrosion-resistant materials | Sterile conditions, temperature/pH control, biocompatible materials |
Environmental Control | Focus on reaction kinetics, heat transfer, pressure | Control of temperature, pH, dissolved oxygen, nutrient levels, sterility |
Scale-Up | Straightforward, based on chemical engineering principles | Complex, requires careful management of oxygen transfer, shear stress, etc. |
Examples | Ammonia production, polyethylene synthesis, sulfuric acid manufacturing | Beer production, monoclonal antibody production, wastewater treatment |
Need help choosing the right reactor for your application? Contact our experts today for tailored solutions!