Extrusion and co-extrusion are both manufacturing processes used to create plastic products, but they differ in complexity and application. Standard extrusion involves melting solid plastic pellets and forcing them through a die to create a continuous shape, such as pipes, tubes, or sheets. Co-extrusion, on the other hand, uses multiple extruders to combine different materials into a single product, creating layered or encapsulated structures. This allows for enhanced functionality, such as improved barrier properties, strength, or aesthetic appeal. While extrusion is simpler and more cost-effective for single-material products, co-extrusion is ideal for applications requiring multiple material properties in one product.
Key Points Explained:
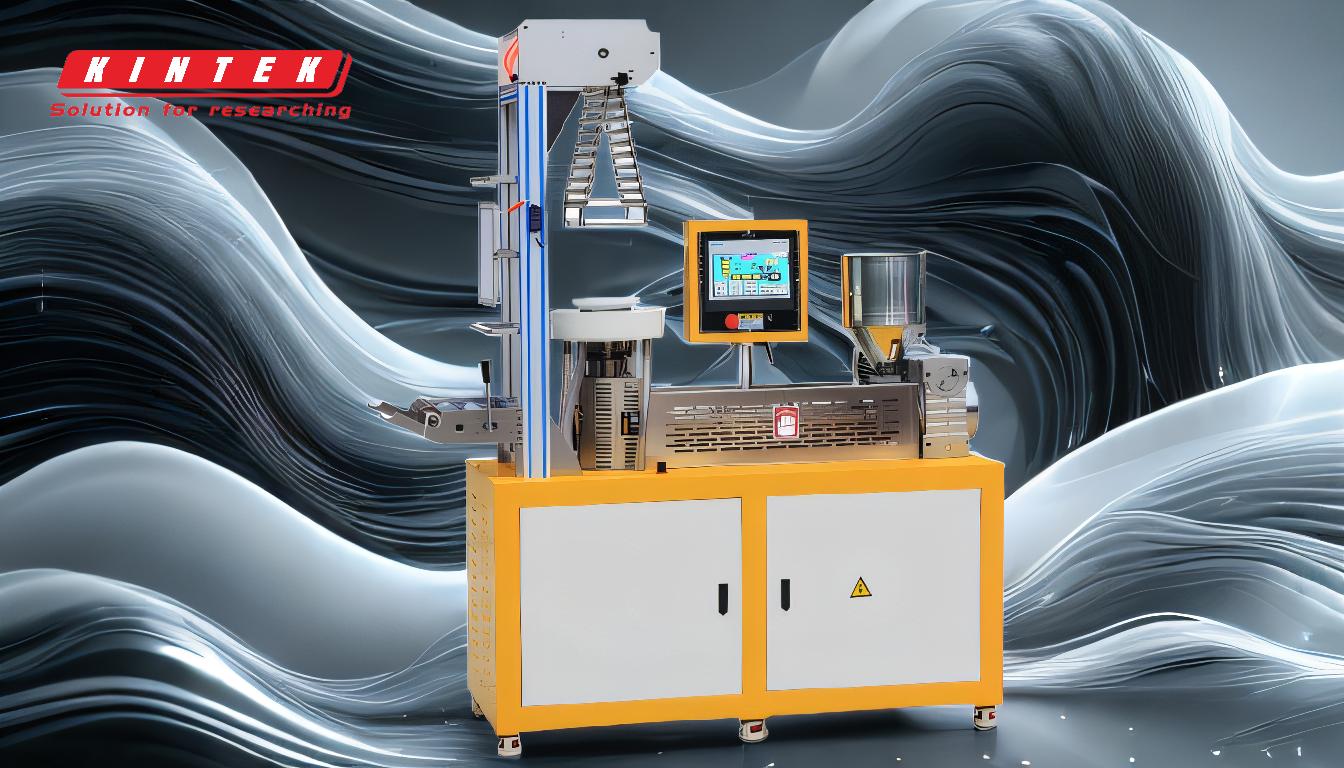
-
Process Overview:
- Extrusion: In standard extrusion, solid plastic pellets are gravity-fed into a forming mechanism. Compression screws melt the pellets, and the molten plastic is forced through a die to create a continuous shape. This process is used for single-material products like pipes, tubes, and sheets.
- Co-Extrusion: Co-extrusion involves multiple extruders working simultaneously. Each extruder processes a different material, which are then combined in a die to form a single product with multiple layers or encapsulated components. This is used for products requiring multiple material properties, such as food packaging with barrier layers.
-
Material Usage:
- Extrusion: Utilizes a single type of plastic material. The process is straightforward, making it cost-effective for producing uniform products.
- Co-Extrusion: Uses multiple materials, which can include different types of plastics or even combinations of plastic with other materials like adhesives or barrier layers. This allows for more complex and functional product designs.
-
Applications:
- Extrusion: Commonly used for products like PVC pipes, plastic sheets, and profiles. It is ideal for applications where a single material suffices.
- Co-Extrusion: Used in applications requiring multiple material properties, such as multi-layer food packaging, automotive parts with different surface and core materials, and medical tubing with barrier layers.
-
Advantages and Limitations:
-
Extrusion:
- Advantages: Simplicity, cost-effectiveness, and high production rates for single-material products.
- Limitations: Limited to single-material products, which may not meet the requirements for more complex applications.
-
Co-Extrusion:
- Advantages: Ability to combine different materials, enhancing product functionality and performance. This can include improved barrier properties, strength, and aesthetic appeal.
- Limitations: More complex and expensive due to the need for multiple extruders and precise control over material flow and layering.
-
Extrusion:
-
Equipment and Setup:
- Extrusion: Requires a single extruder, a die, and a cooling circulator system. The setup is relatively simple and can be easily scaled for high-volume production.
- Co-Extrusion: Requires multiple extruders, each dedicated to a different material, and a complex die that can combine these materials into a single product. The setup is more complex and requires precise control to ensure proper material layering and bonding.
-
Quality and Performance:
- Extrusion: Produces uniform products with consistent properties. However, the properties are limited to those of the single material used.
- Co-Extrusion: Allows for the creation of products with tailored properties, such as enhanced strength, flexibility, or barrier performance. This makes it suitable for more demanding applications.
In summary, while extrusion is a simpler and more cost-effective process for single-material products, co-extrusion offers the ability to create more complex and functional products by combining multiple materials. The choice between the two depends on the specific requirements of the product being manufactured.
Summary Table:
Aspect | Extrusion | Co-Extrusion |
---|---|---|
Process | Single extruder, single material, simpler process | Multiple extruders, multiple materials, complex layering |
Materials | Single type of plastic | Multiple materials (e.g., plastics, adhesives, barrier layers) |
Applications | Pipes, tubes, sheets, profiles | Multi-layer food packaging, automotive parts, medical tubing |
Advantages | Cost-effective, high production rates, simplicity | Enhanced functionality (e.g., barrier properties, strength, aesthetics) |
Limitations | Limited to single-material products | More complex, expensive, requires precise control |
Equipment | Single extruder, die, cooling system | Multiple extruders, complex die, precise layering control |
Quality | Uniform products with consistent properties | Tailored properties (e.g., strength, flexibility, barrier performance) |
Need help choosing between extrusion and co-extrusion for your project? Contact our experts today!