The difference between single screw and twin screw extruders primarily lies in their design, functionality, and application suitability. Single screw extruders are simpler and more cost-effective, ideal for straightforward extrusion tasks. Twin screw extruders, on the other hand, offer superior mixing, compounding, and throughput capabilities, making them better suited for complex material processing and high-volume production. Below is a detailed breakdown of the key differences and their implications.
Key Points Explained:
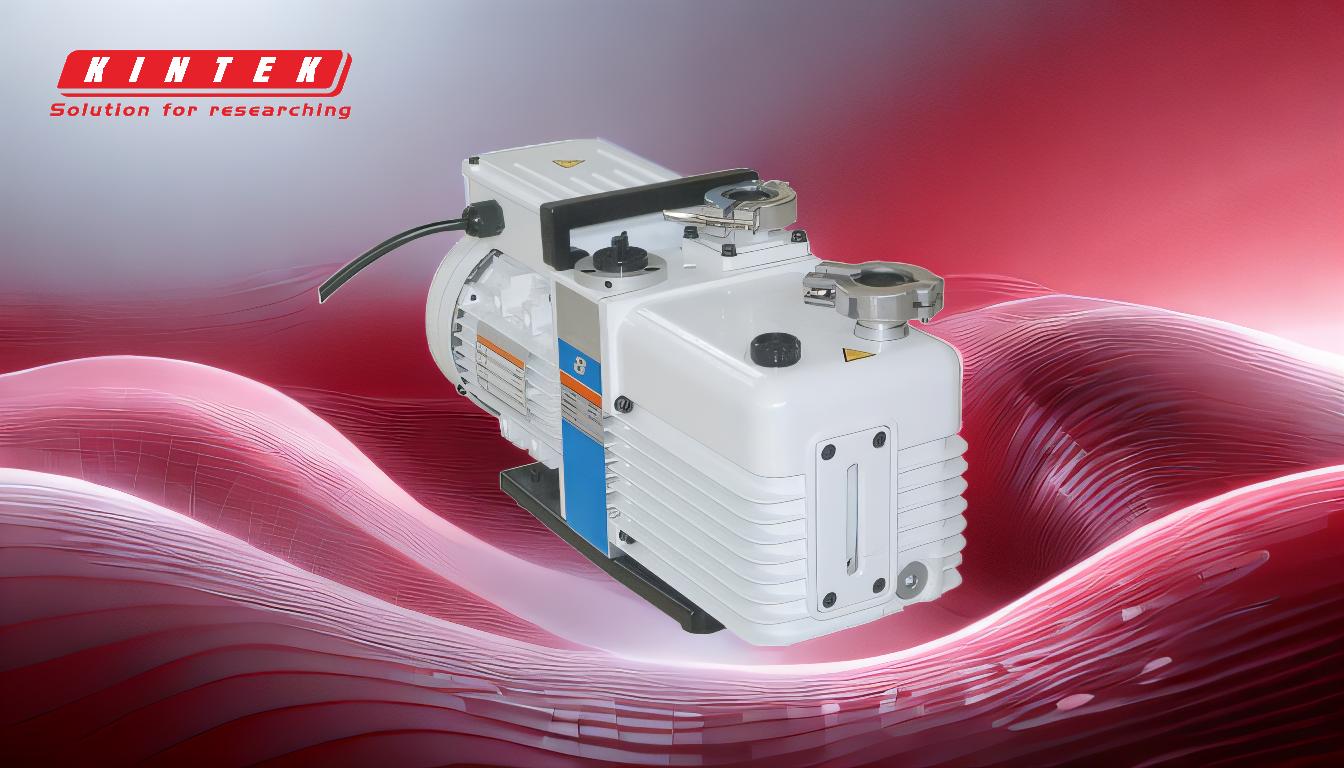
-
Design and Mechanism:
-
Single Screw Extruder:
- Utilizes a single rotating screw within a barrel to transport, melt, and push materials through the die.
- The screw design is relatively simple, with fewer moving parts, making it easier to maintain and operate.
-
Twin Screw Extruder:
- Employs two intermeshing screws that rotate either co-rotating (same direction) or counter-rotating (opposite directions).
- The dual-screw design provides better control over material flow, shear, and mixing.
-
Single Screw Extruder:
-
Mixing and Compounding Capabilities:
-
Single Screw Extruder:
- Limited mixing ability due to the single-screw design, making it less effective for applications requiring precise material blending.
- Suitable for simpler tasks like melting and shaping polymers.
-
Twin Screw Extruder:
- Offers excellent mixing and compounding capabilities due to the intermeshing screws, which create multiple shear zones and enhance material interaction.
- Ideal for applications requiring precise blending of additives, fillers, or multiple polymers.
-
Single Screw Extruder:
-
Throughput and Productivity:
-
Single Screw Extruder:
- Generally has a lower throughput capacity, making it less suitable for high-volume production.
- More cost-effective for small-scale or less demanding operations.
-
Twin Screw Extruder:
- Provides higher throughput capacity, enabling increased productivity and efficiency.
- Better suited for large-scale production and complex material processing.
-
Single Screw Extruder:
-
Material Versatility:
-
Single Screw Extruder:
- Best suited for processing standard polymers and materials that do not require extensive mixing or compounding.
-
Twin Screw Extruder:
- Capable of handling a wider range of materials, including heat-sensitive polymers, composites, and materials requiring precise formulation control.
-
Single Screw Extruder:
-
Cost and Maintenance:
-
Single Screw Extruder:
- Lower initial cost and simpler maintenance due to fewer components and straightforward design.
-
Twin Screw Extruder:
- Higher initial investment and more complex maintenance due to the dual-screw mechanism and advanced features.
-
Single Screw Extruder:
-
Applications:
-
Single Screw Extruder:
- Commonly used in basic extrusion processes such as pipe, sheet, and film production.
-
Twin Screw Extruder:
- Preferred for advanced applications like compounding, reactive extrusion, and processing of specialty materials.
-
Single Screw Extruder:
In summary, the choice between single screw and twin screw extruders depends on the specific requirements of the application. Single screw extruders are cost-effective and suitable for simpler tasks, while twin screw extruders excel in complex material processing and high-volume production. Understanding these differences is crucial for selecting the right equipment to meet production goals and material requirements.
Summary Table:
Aspect | Single Screw Extruder | Twin Screw Extruder |
---|---|---|
Design and Mechanism | Single rotating screw; simpler design, fewer moving parts | Dual intermeshing screws; better control over material flow, shear, and mixing |
Mixing and Compounding | Limited mixing ability; suitable for simple tasks | Excellent mixing and compounding; ideal for precise blending of additives or polymers |
Throughput | Lower throughput capacity; cost-effective for small-scale operations | Higher throughput capacity; better for high-volume production |
Material Versatility | Best for standard polymers and simple materials | Handles heat-sensitive polymers, composites, and complex formulations |
Cost and Maintenance | Lower initial cost; simpler maintenance | Higher initial investment; more complex maintenance |
Applications | Basic extrusion processes (e.g., pipe, sheet, film production) | Advanced applications (e.g., compounding, reactive extrusion, specialty materials) |
Need help choosing the right extruder for your application? Contact our experts today for personalized advice!