Sputter coating is a physical vapor deposition (PVD) process used to apply thin, uniform coatings onto substrates. It involves creating a plasma by electrically charging a sputtering cathode, which ejects target material atoms that then deposit onto the substrate. This process is widely used in applications like Scanning Electron Microscopy (SEM) to improve secondary electron emission, reduce thermal damage, and inhibit charging. Sputter coating can handle a variety of materials, including metals and ceramics, and is essential for creating strong atomic-level bonds between the coating and the substrate. The process requires specialized equipment, including vacuum chambers, cooling systems, and magnetic fields to stabilize the plasma and ensure uniform deposition.
Key Points Explained:
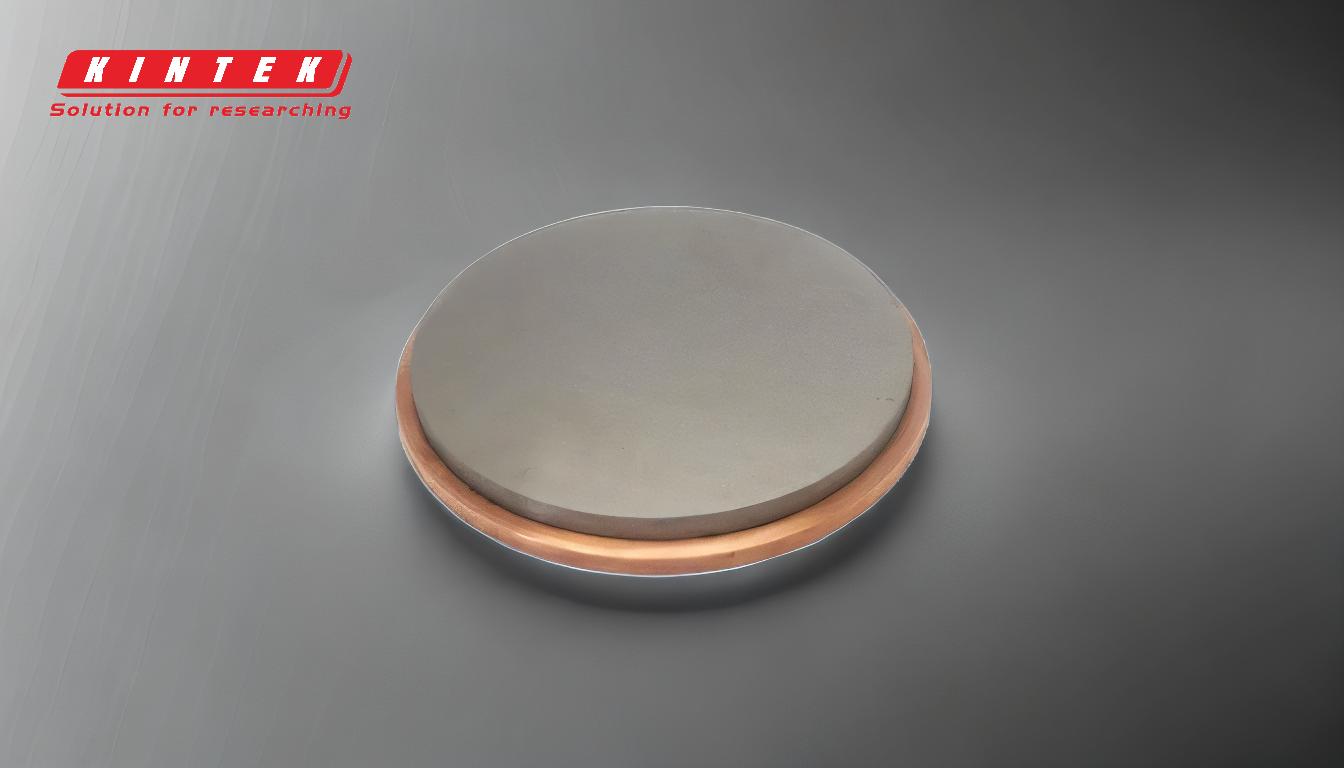
-
Definition and Purpose of Sputter Coating:
- Sputter coating is a physical vapor deposition (PVD) process used to apply thin, functional coatings onto substrates.
- It is commonly used in applications like Scanning Electron Microscopy (SEM) to improve imaging quality by enhancing secondary electron emission, reducing thermal damage, and preventing charging effects.
-
How Sputter Coating Works:
- The process begins by electrically charging a sputtering cathode, which generates a plasma.
- The plasma consists of gas atoms, free electrons, and positively charged ions, typically using argon gas.
- High-energy ions bombard the target material (e.g., gold, metals, or ceramics), causing atoms to be ejected from the target surface in a process called "sputtering."
- These ejected atoms are then deposited onto the substrate, forming a thin, uniform coating.
-
Key Components of a Sputter Coater:
- Vacuum Chamber: Maintains a controlled environment to facilitate the sputtering process.
- Target Material: The material to be deposited, which is bonded or clamped to the cathode.
- Cooling Systems: Manage the heat generated during the process to ensure stable operation.
- Magnetic Fields: Concentrate the plasma and ensure uniform erosion of the target material, leading to consistent coating deposition.
-
Advantages of Sputter Coating:
- Uniform Coating: The omni-directional nature of sputtered atoms ensures even coverage on complex surfaces.
- Strong Atomic Bonds: The high-energy deposition process creates strong atomic-level bonds between the coating and the substrate.
- Versatility: Can be used with a wide range of materials, including metals, ceramics, and insulating materials.
- Improved SEM Performance: Reduces charging effects and enhances secondary electron emission, making it ideal for SEM applications.
-
Challenges and Limitations:
- Low Deposition Rates: Early sputtering methods, like DC diode sputtering, had low deposition rates, though advancements like DC triple sputtering and quadrupole sputtering have improved efficiency.
- Heat Generation: The process generates significant heat, requiring specialized cooling systems to manage thermal effects.
- Complexity: The equipment and process are more complex compared to other coating methods, requiring precise control of vacuum, plasma, and magnetic fields.
-
Applications of Sputter Coating:
- SEM and Microscopy: Enhances imaging quality by improving secondary electron emission and reducing charging effects.
- Electronics: Used to deposit thin films for semiconductors, solar panels, and other electronic components.
- Optics: Applied to create reflective or anti-reflective coatings on lenses and mirrors.
- Decorative Coatings: Used in industries like automotive and jewelry to create durable, aesthetically pleasing finishes.
-
Evolution of Sputter Coating Technology:
- Early methods, such as DC diode sputtering, were simple but had limitations like low deposition rates and inability to handle insulating materials.
- Advances like DC triple sputtering and quadrupole sputtering improved ionization and discharge stability, though challenges like low deposition rates remain.
- Modern sputter coaters incorporate magnetic fields and advanced cooling systems to enhance performance and reliability.
-
Importance of Target Material and Gas:
- The choice of target material (e.g., gold, metals, or ceramics) determines the properties of the coating.
- Argon gas is commonly used due to its inert nature and ability to efficiently ionize, facilitating the sputtering process.
By understanding these key points, equipment and consumable purchasers can make informed decisions about selecting sputter coaters and materials for their specific applications.
Summary Table:
Key Aspect | Details |
---|---|
Definition | Physical vapor deposition (PVD) process for applying thin, uniform coatings. |
How It Works | Uses plasma to eject target material atoms, depositing them on substrates. |
Key Components | Vacuum chamber, target material, cooling systems, magnetic fields. |
Advantages | Uniform coating, strong atomic bonds, versatility, improved SEM performance. |
Applications | SEM, electronics, optics, decorative coatings. |
Challenges | Low deposition rates, heat generation, process complexity. |
Discover how sputter coating can elevate your projects—contact us today for expert guidance!