Heat transfer in agitated vessels is a critical aspect of many industrial processes, particularly in chemical, pharmaceutical, and food industries. It involves the transfer of heat between the vessel's contents and an external heat source or sink, facilitated by agitation. The agitation enhances heat transfer by improving fluid mixing, reducing temperature gradients, and increasing the contact area between the fluid and the heat transfer surface. The efficiency of heat transfer in agitated vessels depends on factors such as the type of agitator, the properties of the fluid, the geometry of the vessel, and the operating conditions. Understanding these factors is essential for optimizing heat transfer processes in industrial applications.
Key Points Explained:
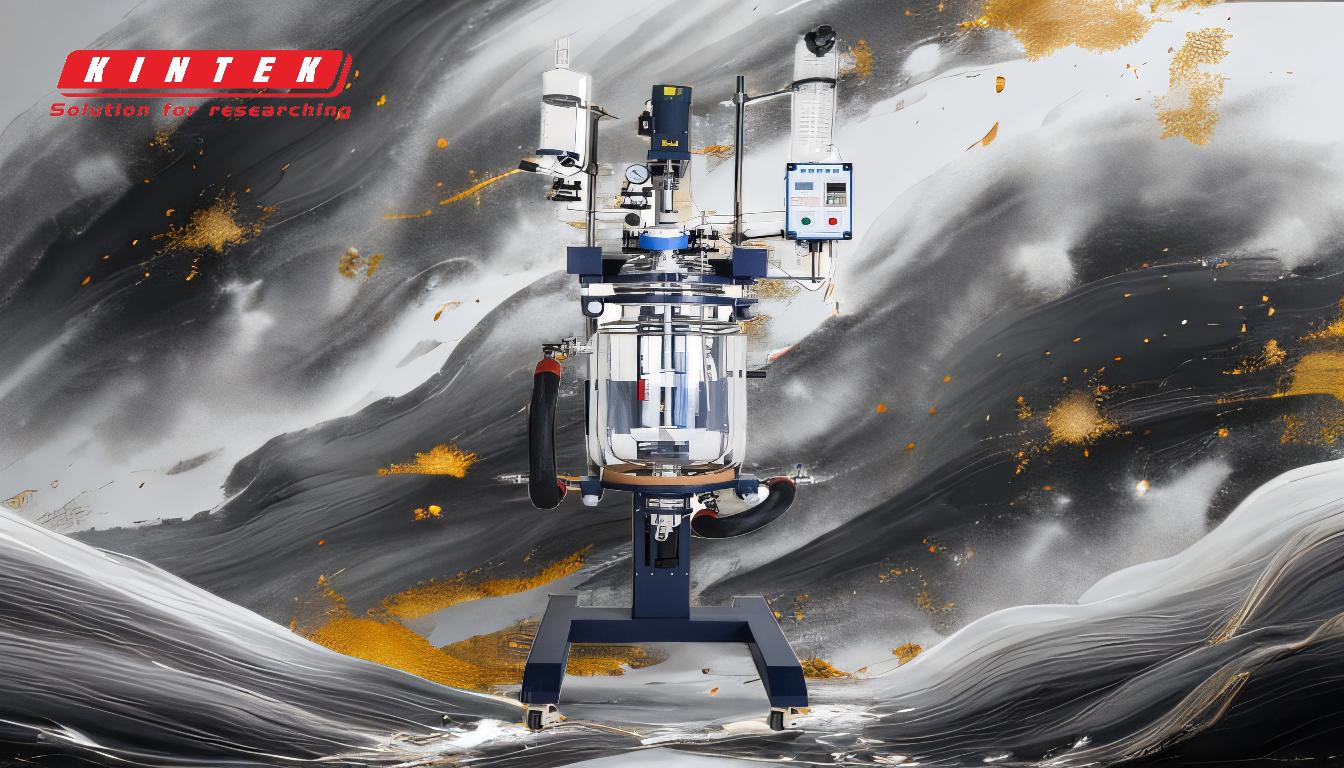
-
Mechanisms of Heat Transfer in Agitated Vessels:
- Conduction: Heat transfer through direct contact between particles within the fluid. In agitated vessels, conduction is less significant compared to convection due to the enhanced mixing.
- Convection: The primary mechanism of heat transfer in agitated vessels. Convection involves the movement of fluid particles, which carry heat from one part of the vessel to another. Agitation enhances convective heat transfer by ensuring uniform temperature distribution and reducing thermal gradients.
- Radiation: Generally negligible in most industrial applications involving agitated vessels, as the temperatures are not high enough for significant radiative heat transfer.
-
Factors Influencing Heat Transfer:
- Agitator Type: Different agitators (e.g., paddle, turbine, propeller) create varying flow patterns and mixing intensities, which directly affect heat transfer efficiency. For example, turbine agitators are known for their high shear and mixing capabilities, making them suitable for processes requiring rapid heat transfer.
- Fluid Properties: The thermal conductivity, viscosity, and specific heat capacity of the fluid play a crucial role in determining the rate of heat transfer. High thermal conductivity and low viscosity generally enhance heat transfer.
- Vessel Geometry: The shape and size of the vessel, as well as the presence of baffles, influence the flow patterns and, consequently, the heat transfer. Baffles, for instance, prevent vortex formation and improve mixing, thereby enhancing heat transfer.
- Operating Conditions: Parameters such as agitation speed, temperature difference between the fluid and the heat transfer surface, and the presence of multiple phases (e.g., gas-liquid systems) significantly impact heat transfer rates.
-
Heat Transfer Coefficients:
- The overall heat transfer coefficient (U) is a measure of the heat transfer efficiency in agitated vessels. It is influenced by the individual heat transfer coefficients on the fluid side (h_fluid) and the heat transfer surface side (h_surface), as well as the thermal resistance of the vessel wall.
- Correlations are often used to estimate the heat transfer coefficients in agitated vessels. These correlations take into account factors such as the Reynolds number (Re), Prandtl number (Pr), and Nusselt number (Nu), which are dimensionless numbers that describe the flow regime, fluid properties, and heat transfer characteristics, respectively.
-
Applications of Heat Transfer in Agitated Vessels:
- Chemical Reactors: In exothermic or endothermic reactions, efficient heat transfer is crucial to maintain the desired reaction temperature and ensure optimal reaction rates.
- Pharmaceutical Manufacturing: Heat transfer is essential in processes such as crystallization, where precise temperature control is required to achieve the desired product properties.
- Food Processing: Agitated vessels are used in processes like pasteurization and sterilization, where heat transfer is necessary to ensure product safety and quality.
-
Optimization of Heat Transfer:
- Agitator Design: Selecting the appropriate agitator type and design can significantly enhance heat transfer. For example, using a high-shear agitator in a highly viscous fluid can improve mixing and heat transfer.
- Baffle Installation: Installing baffles in the vessel can prevent the formation of dead zones and improve overall mixing, leading to better heat transfer.
- Control of Operating Parameters: Adjusting parameters such as agitation speed and temperature difference can optimize heat transfer. For instance, increasing the agitation speed can enhance convective heat transfer, but it may also increase energy consumption.
-
Challenges and Considerations:
- Scaling Up: Heat transfer characteristics can change significantly when scaling up from laboratory to industrial-scale vessels. It is essential to consider factors such as geometric similarity and power input per unit volume.
- Fouling: The accumulation of deposits on heat transfer surfaces can reduce heat transfer efficiency. Regular cleaning and maintenance are necessary to mitigate fouling.
- Energy Consumption: Agitation requires energy, and optimizing heat transfer often involves balancing energy consumption with process requirements. Energy-efficient agitator designs and operating strategies can help reduce costs.
In conclusion, heat transfer in agitated vessels is a complex process influenced by various factors, including agitator design, fluid properties, vessel geometry, and operating conditions. Understanding these factors and their interactions is crucial for optimizing heat transfer in industrial applications. By carefully selecting agitator types, installing baffles, and controlling operating parameters, it is possible to enhance heat transfer efficiency, ensuring optimal process performance and product quality.
Summary Table:
Key Factor | Impact on Heat Transfer |
---|---|
Agitator Type | Influences flow patterns and mixing intensity; e.g., turbine agitators enhance rapid heat transfer. |
Fluid Properties | High thermal conductivity and low viscosity improve heat transfer efficiency. |
Vessel Geometry | Shape, size, and baffles affect flow patterns and mixing, enhancing heat transfer. |
Operating Conditions | Agitation speed, temperature difference, and multi-phase systems impact heat transfer rates. |
Heat Transfer Coefficients | Overall heat transfer coefficient (U) depends on fluid-side and surface-side coefficients. |
Optimize your industrial heat transfer processes today—contact our experts for tailored solutions!