The pharmaceutical industry relies on specialized mixers to ensure uniform blending of powders, granules, and other materials, which is critical for product consistency and quality. One of the most commonly used mixers in this industry is the Ribbon Blender, known for its efficiency and reliability in handling pharmaceutical powders. This mixer features a cylindrical design with a ribbon-like paddle that rotates around a central axis, ensuring thorough mixing. Below, we explore the key aspects of the Ribbon Blender and its significance in pharmaceutical applications.
Key Points Explained:
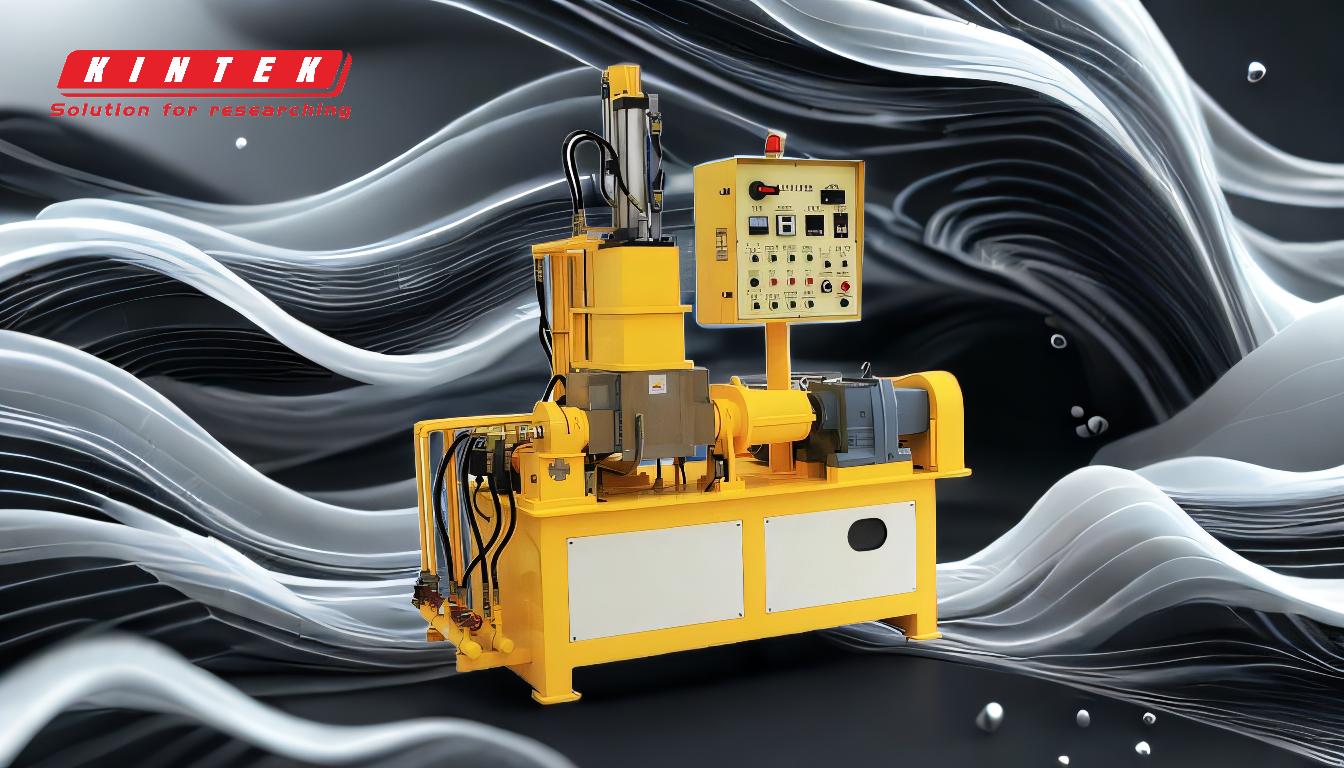
-
Design and Functionality of the Ribbon Blender:
- The Ribbon Blender consists of a horizontal cylindrical vessel with a double-helical ribbon agitator. The outer ribbon moves materials in one direction, while the inner ribbon moves them in the opposite direction, creating a highly efficient mixing action.
- This design ensures that materials are thoroughly blended, minimizing the risk of segregation or uneven distribution, which is crucial for pharmaceutical formulations.
-
Applications in the Pharmaceutical Industry:
- The Ribbon Blender is ideal for blending dry powders, granules, and other solid materials. It is commonly used in the production of tablets, capsules, and other solid dosage forms.
- Its gentle mixing action makes it suitable for fragile or heat-sensitive materials, ensuring that the integrity of the active pharmaceutical ingredients (APIs) is maintained.
-
Advantages of the Ribbon Blender:
- Uniform Mixing: The counter-rotating ribbons ensure consistent blending, even for materials with varying particle sizes or densities.
- Scalability: Ribbon Blenders are available in a wide range of sizes, making them suitable for both small-scale laboratory use and large-scale industrial production.
- Ease of Cleaning: The simple design and smooth surfaces of the blender make it easy to clean and sanitize, which is essential for maintaining compliance with Good Manufacturing Practices (GMP).
-
Considerations for Equipment Purchasers:
- When selecting a Ribbon Blender, factors such as material compatibility, batch size, and regulatory compliance should be considered.
- Stainless steel construction is often preferred for pharmaceutical applications due to its durability, corrosion resistance, and ease of cleaning.
- Additional features, such as jacketed vessels for temperature control or vacuum capabilities, may be required depending on the specific application.
-
Comparison with Other Mixers:
- While the Ribbon Blender is highly effective for dry blending, other mixers like Planetary Mixers or High-Shear Mixers may be more suitable for wet granulation or emulsification processes.
- The choice of mixer depends on the specific requirements of the pharmaceutical formulation and the desired end product.
In summary, the Ribbon Blender is a versatile and reliable mixer widely used in the pharmaceutical industry for its ability to achieve uniform blending of powders and granules. Its design, scalability, and ease of cleaning make it an essential tool for ensuring product quality and compliance with industry standards.
Summary Table:
Aspect | Details |
---|---|
Design | Horizontal cylindrical vessel with double-helical ribbon agitator |
Functionality | Outer and inner ribbons move materials in opposite directions for uniform mixing |
Applications | Blending dry powders, granules, and solid materials for tablets and capsules |
Advantages | Uniform mixing, scalability, ease of cleaning, and GMP compliance |
Key Considerations | Material compatibility, batch size, stainless steel construction, and additional features like jacketed vessels |
Comparison | More suitable for dry blending compared to Planetary or High-Shear Mixers |
Ensure your pharmaceutical formulations meet industry standards—contact us today to learn more about Ribbon Blenders and single tablet press!