The rubber mixing process is a critical step in determining the physical and chemical properties of vulcanized rubber. It begins with rubber mastication, where raw rubber is softened and plasticized to make it easier to process. This is followed by the incorporation of rubber chemicals and fillers, which are mixed into the rubber to achieve the desired properties. Internal mixers are commonly used in this process due to their ability to handle viscous mixtures efficiently. These mixers use rotating rotors to shear and rub the material, increasing its temperature and reducing viscosity, which ensures thorough mixing and uniform dispersion of additives. The process is essential for producing high-quality rubber products with consistent performance characteristics.
Key Points Explained:
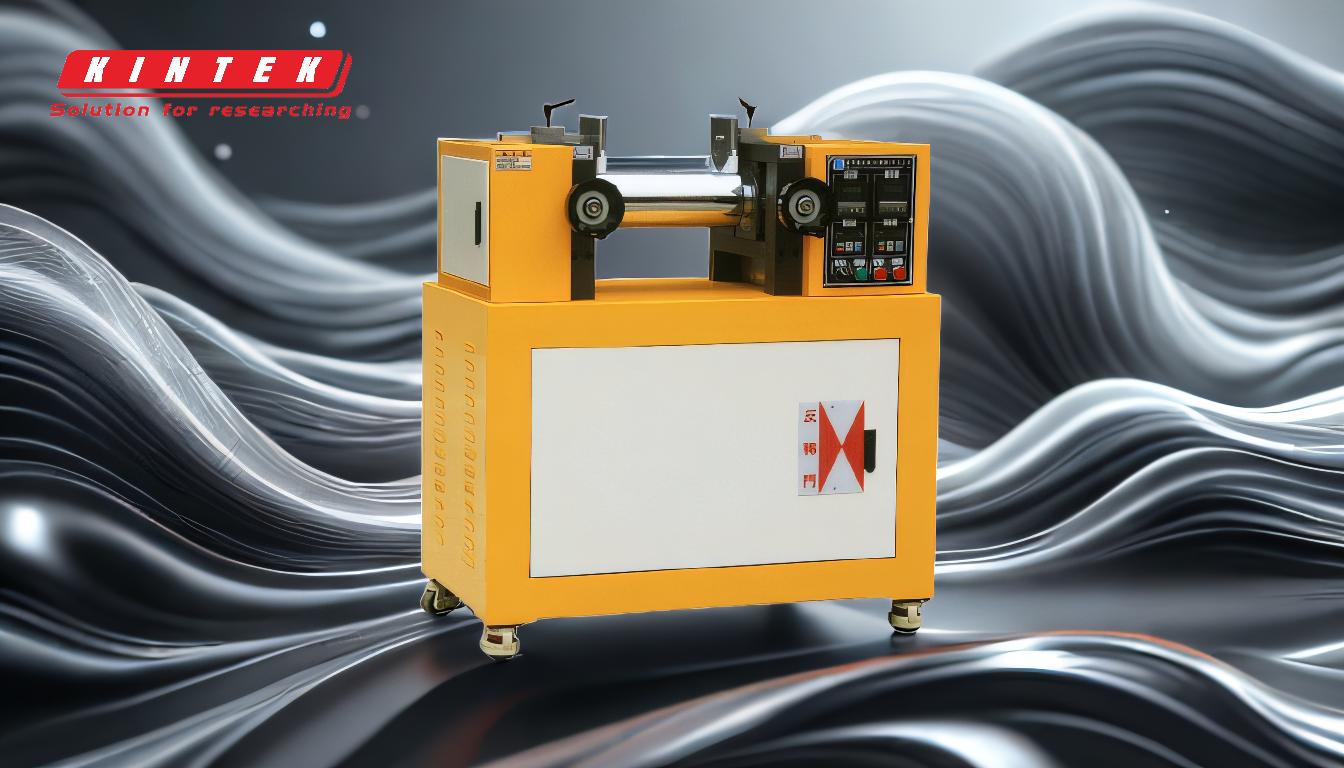
-
Rubber Mastication:
- Purpose: The first step in the rubber mixing process is mastication, where raw rubber is softened and plasticized. This makes the rubber more pliable and easier to work with in subsequent steps.
- Process: Mastication involves mechanically working the rubber to break down its molecular structure, reducing its viscosity and making it more receptive to additives.
-
Incorporation of Chemicals and Fillers:
- Purpose: After mastication, rubber chemicals and fillers are added to the rubber. These additives are essential for imparting specific properties to the rubber, such as strength, elasticity, and resistance to wear and tear.
- Process: The chemicals and fillers are mixed into the rubber using internal mixers. The goal is to achieve a uniform dispersion of these additives throughout the rubber matrix.
-
Use of Internal Mixers:
- Advantages: Internal mixers are the most commonly used equipment in rubber mixing due to their ability to handle highly viscous mixtures. They are equipped with powerful motors and gearboxes to maintain a consistent mixing process.
- Mechanism: The mixers use two rotors that rotate relative to each other. This action shears and rubs the rubber material, increasing its temperature and reducing its viscosity. The heat generated helps in better wetting of the rubber on the compounding agent's surface, ensuring thorough mixing.
-
Temperature and Viscosity Control:
- Importance: The temperature of the rubber material rises during mixing, which decreases its viscosity. This is crucial for ensuring that the compounding agents are uniformly dispersed throughout the rubber.
- Effect: Lower viscosity allows for better flow and mixing, leading to a more homogeneous mixture. This is essential for achieving consistent properties in the final rubber product.
-
Uniform Dispersion of Additives:
- Goal: The primary objective of the mixing process is to achieve a uniform dispersion of all additives within the rubber matrix.
- Achievement: This is facilitated by the continuous stirring and shearing action of the rotor ridges in the internal mixer. The mechanical action ensures that all parts of the rubber are equally exposed to the additives, leading to a consistent mixture.
-
Challenges and Considerations:
- Downtime: If the internal mixers fail, it can be difficult to clear blockages and restart production, leading to significant downtime. This highlights the importance of regular maintenance and the use of reliable equipment.
- Quality Control: Ensuring that the mixing process is carried out correctly is vital for the quality of the final product. Any inconsistencies in mixing can lead to defects in the rubber, affecting its performance.
In summary, the rubber mixing process is a complex but essential step in rubber manufacturing. It involves several stages, from mastication to the incorporation of additives, all aimed at producing a high-quality, uniform rubber product. The use of internal mixers plays a crucial role in this process, ensuring efficient and thorough mixing of all components. Proper control of temperature and viscosity, along with regular maintenance of equipment, are key to achieving consistent results.
Summary Table:
Step | Purpose | Process |
---|---|---|
Rubber Mastication | Softens and plasticizes raw rubber for easier processing. | Mechanically breaks down molecular structure, reducing viscosity. |
Additive Incorporation | Imparts properties like strength, elasticity, and wear resistance. | Mixes chemicals and fillers uniformly using internal mixers. |
Internal Mixers | Handles viscous mixtures efficiently for thorough mixing. | Rotors shear and rub material, increasing temperature and reducing viscosity. |
Temperature Control | Ensures uniform dispersion of additives. | Heat reduces viscosity, improving flow and mixing. |
Uniform Dispersion | Achieves consistent properties in the final product. | Continuous stirring and shearing ensure even exposure to additives. |
Challenges | Minimizes downtime and maintains product quality. | Regular maintenance and reliable equipment are essential. |
Optimize your rubber mixing process for high-quality results—contact our experts today!