Batch reactors are versatile and widely used in laboratory and small-scale production settings. They operate by adding all reactants, catalysts, and necessary components at the start, allowing the reaction to proceed for a fixed time under controlled conditions, and then removing the products. The pressure in a batch reactor depends on factors such as the reaction type, temperature, and volume of reactants. Since batch reactors do not reach a steady state, controlling pressure and temperature is critical to ensure safety and optimal reaction conditions. They are ideal for small-scale production, high flexibility, and reactions requiring precise control.
Key Points Explained:
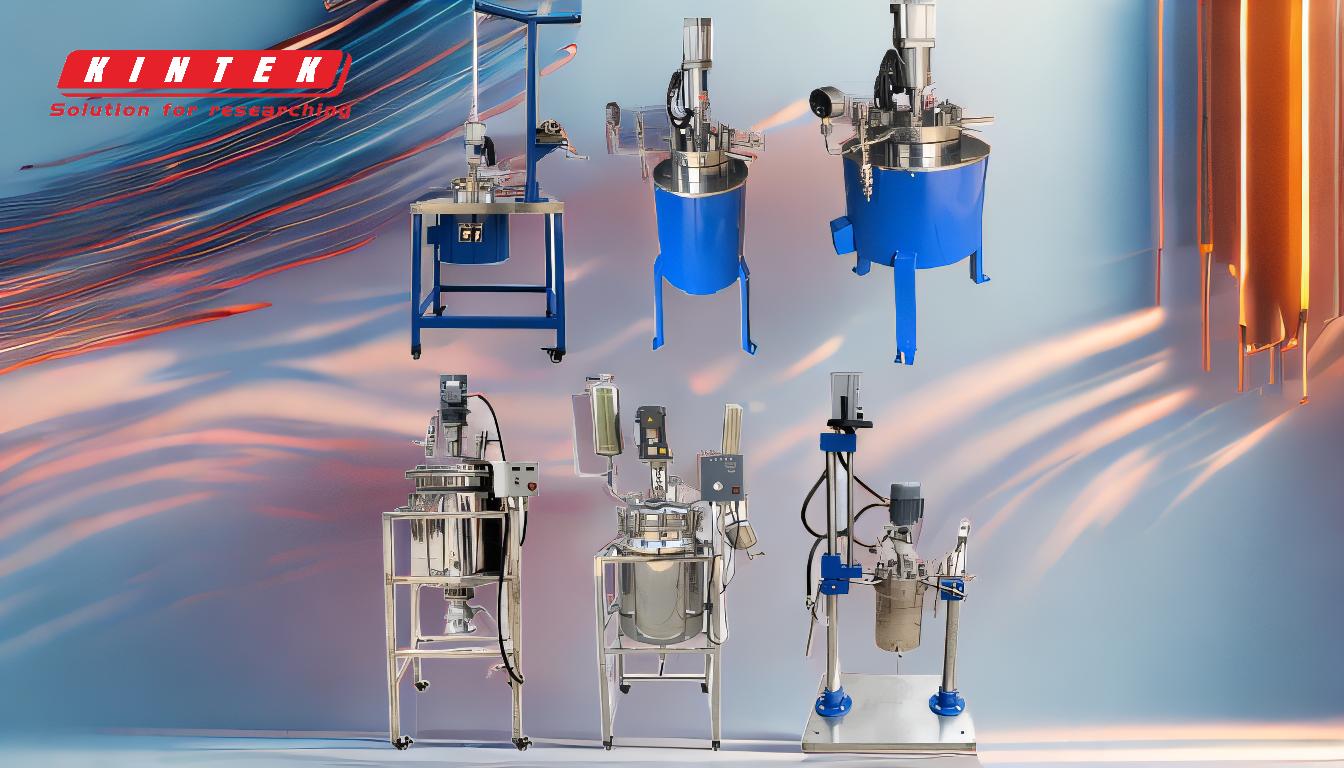
-
Definition and Operation of Batch Reactors:
- A batch reactor is a closed system where reactants are added at the start, allowed to react for a specific time, and products are removed at the end.
- It operates under non-continuous conditions, meaning no additional reactants or products flow in or out during the reaction.
- This setup is ideal for reactions requiring precise control over time, temperature, and pressure.
-
Factors Influencing Pressure in Batch Reactors:
- Reaction Type: Exothermic reactions (releasing heat) or reactions producing gases can increase internal pressure.
- Temperature: Higher temperatures can increase pressure due to gas expansion or increased reaction rates.
- Volume of Reactants: The amount of reactants and their phase (liquid, gas, or solid) affects pressure. For example, gas-phase reactions are more sensitive to pressure changes.
- Reactor Design: The strength and sealing of the reactor vessel determine the maximum allowable pressure.
-
Pressure Control in Batch Reactors:
- Batch reactors often include pressure relief valves or sensors to monitor and control pressure.
- Temperature regulation is critical, as it directly impacts pressure. Heating or cooling systems are used to maintain desired conditions.
- Proper sealing and material selection for the reactor vessel ensure it can withstand the expected pressure range.
-
Applications and Advantages of Batch Reactors:
- Small-Scale Production: Ideal for producing small quantities of high-value products, such as pharmaceuticals or specialty chemicals.
- Flexibility: Suitable for reactions requiring varying conditions, such as different temperatures or pressures.
- Ease of Cleaning and Versatility: Batch reactors can be easily cleaned and adapted for different reactions, making them cost-effective for laboratory and pilot-scale operations.
-
Safety Considerations:
- Batch reactors must be designed to handle the maximum expected pressure to prevent explosions or leaks.
- Pressure sensors and relief systems are essential for safe operation, especially in reactions involving gases or volatile compounds.
- Operators must monitor pressure and temperature closely, particularly in exothermic reactions, to avoid runaway reactions.
-
Comparison with Other Reactor Types:
- Unlike continuous reactors, batch reactors do not reach a steady state, requiring careful control of input and output materials.
- They are simpler in design and operation compared to continuous or semi-batch reactors, making them suitable for small-scale and experimental applications.
By understanding these key points, purchasers and operators of batch reactors can make informed decisions about their use, ensuring safe and efficient operation while achieving desired reaction outcomes.
Summary Table:
Aspect | Details |
---|---|
Operation | Closed system; reactants added at start, products removed after reaction. |
Pressure Factors | Reaction type, temperature, volume of reactants, and reactor design. |
Pressure Control | Relief valves, sensors, temperature regulation, and proper sealing. |
Applications | Small-scale production, pharmaceuticals, specialty chemicals. |
Advantages | Flexibility, precise control, ease of cleaning, and cost-effectiveness. |
Safety Considerations | Pressure sensors, relief systems, and monitoring for exothermic reactions. |
Discover how batch reactors can optimize your lab or production process—contact us today for expert advice!