RF sputtering, or Radio Frequency sputtering, is a thin-film deposition technique widely used in industries such as semiconductors and electronics. It involves using a high-frequency alternating current (typically 13.56 MHz) to ionize an inert gas in a vacuum chamber, creating a plasma. The ions in the plasma bombard the target material, causing atoms to be ejected and deposited onto a substrate. Unlike DC sputtering, RF sputtering is particularly effective for insulating (non-conductive) materials because the alternating electrical potential prevents charge buildup on the target surface. This process consists of two cycles: the positive cycle, where electrons are attracted to the target, and the negative cycle, where ion bombardment continues, ensuring efficient sputtering of both conductive and non-conductive materials.
Key Points Explained:
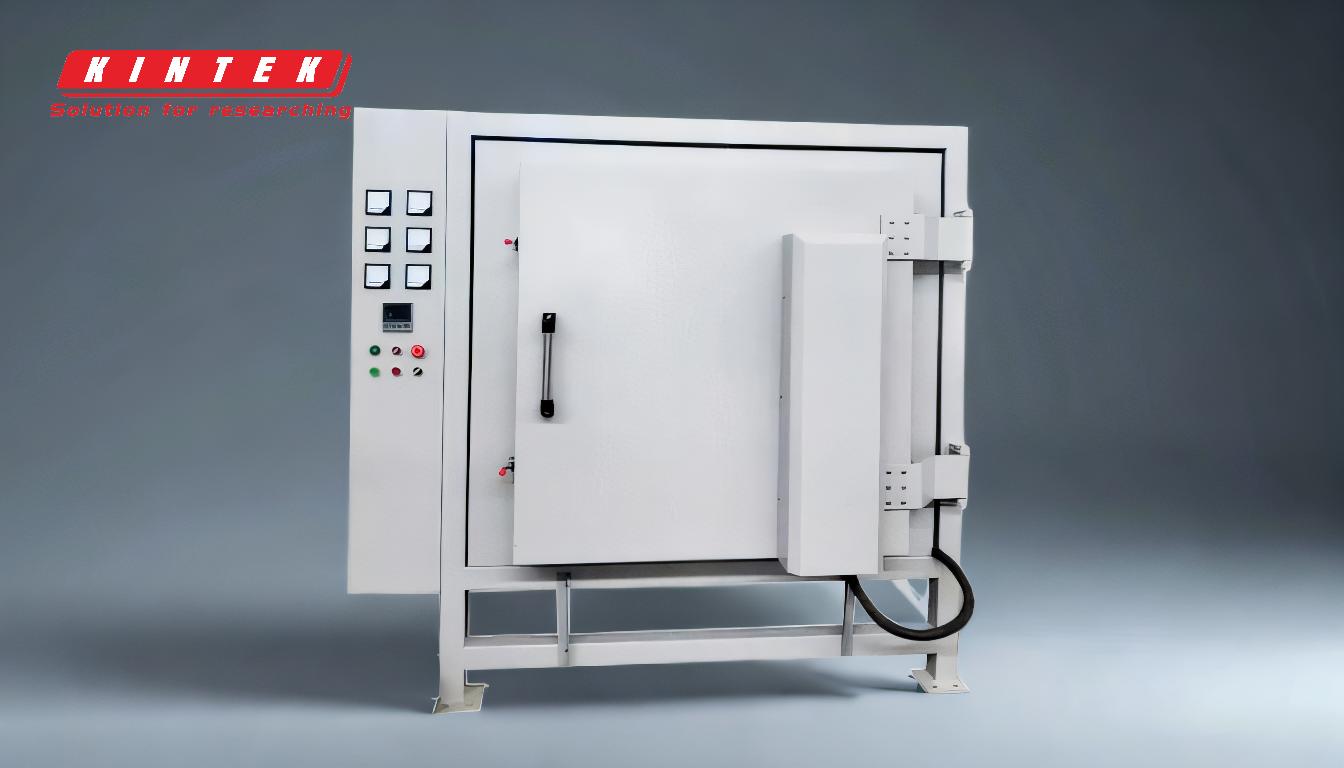
-
Basic Principle of RF Sputtering:
- RF sputtering uses radio frequency (RF) power, typically at 13.56 MHz, to create a plasma in a vacuum chamber filled with inert gas (e.g., argon).
- The alternating current alternates the electrical potential, which prevents charge buildup on insulating target materials, a common issue in DC sputtering.
- The process involves two cycles: the positive cycle and the negative cycle, which work together to enable efficient sputtering.
-
The Two Cycles of RF Sputtering:
-
Positive Cycle:
- During the positive half-cycle, the target material acts as an anode and attracts electrons from the plasma.
- This creates a negative bias on the target surface, preparing it for ion bombardment.
-
Negative Cycle:
- In the negative half-cycle, the target becomes positively charged and acts as a cathode.
- High-energy ions from the plasma bombard the target, ejecting atoms that travel to the substrate and form a thin film.
-
Positive Cycle:
-
Advantages for Insulating Materials:
- RF sputtering is particularly effective for depositing insulating (dielectric) materials because the alternating current prevents charge accumulation on the target surface.
- In DC sputtering, insulating materials would accumulate charge, leading to arcing and process termination. RF sputtering avoids this issue by alternating the electrical potential.
-
Role of Inert Gas and Plasma:
- An inert gas, such as argon, is introduced into the vacuum chamber and ionized by the RF power source.
- The ionized gas forms a plasma, which contains positively charged ions and free electrons.
- These ions are accelerated toward the target material, where they sputter off atoms for deposition.
-
RF Magnetron Sputtering:
- RF magnetron sputtering uses magnets to trap electrons near the target material, increasing the ionization efficiency of the gas.
- This results in higher deposition rates compared to standard RF sputtering, making it suitable for industrial applications.
-
Process Parameters:
- RF sputtering operates at a peak-to-peak voltage of around 1000 V and a chamber pressure of 0.5 to 10 mTorr.
- The electron density in the plasma ranges from 10^9 to 10^11 cm^-3, ensuring sufficient ionization for sputtering.
- While RF sputtering is slower than DC sputtering, it is preferred for its ability to handle insulating materials and produce high-quality thin films.
-
Applications of RF Sputtering:
- RF sputtering is widely used in the semiconductor and electronics industries to deposit thin films of insulating materials, such as oxides and nitrides.
- It is also used in the production of optical coatings, solar cells, and other advanced materials.
-
Comparison with DC Sputtering:
- RF sputtering is more versatile than DC sputtering because it can deposit both conductive and non-conductive materials.
- However, RF sputtering has a lower deposition rate and is more expensive, making it less suitable for large-scale production compared to DC sputtering.
By understanding these key points, one can appreciate the unique capabilities of RF sputtering, particularly its ability to handle insulating materials and produce high-quality thin films for advanced applications.
Summary Table:
Key Aspect | Details |
---|---|
Principle | Uses RF power (13.56 MHz) to ionize inert gas, creating plasma for sputtering. |
Two Cycles | Positive cycle (attracts electrons) and negative cycle (ion bombardment). |
Advantages | Effective for insulating materials, prevents charge buildup. |
Inert Gas & Plasma | Argon gas ionized to form plasma, enabling efficient sputtering. |
RF Magnetron Sputtering | Uses magnets to increase ionization efficiency and deposition rates. |
Process Parameters | 1000 V peak-to-peak voltage, 0.5–10 mTorr pressure, 10^9–10^11 cm^-3 density. |
Applications | Semiconductors, electronics, optical coatings, solar cells. |
Comparison with DC Sputtering | Versatile for non-conductive materials but slower and more expensive. |
Discover how RF sputtering can enhance your thin-film deposition process—contact our experts today!