Vacuum evaporation is a process used in various applications, including wastewater treatment and thin-film deposition, where materials are heated under vacuum conditions to separate or deposit substances. The principle relies on reducing the pressure to lower the boiling point of the material, allowing it to evaporate at lower temperatures. In wastewater treatment, this method separates water from high-boiling-point contaminants. In thin-film deposition, the evaporated material forms a vapor stream that condenses onto a substrate, creating a uniform layer. Advanced systems may incorporate vacuum pumps, heaters, and cold traps to enhance efficiency and prevent contamination.
Key Points Explained:
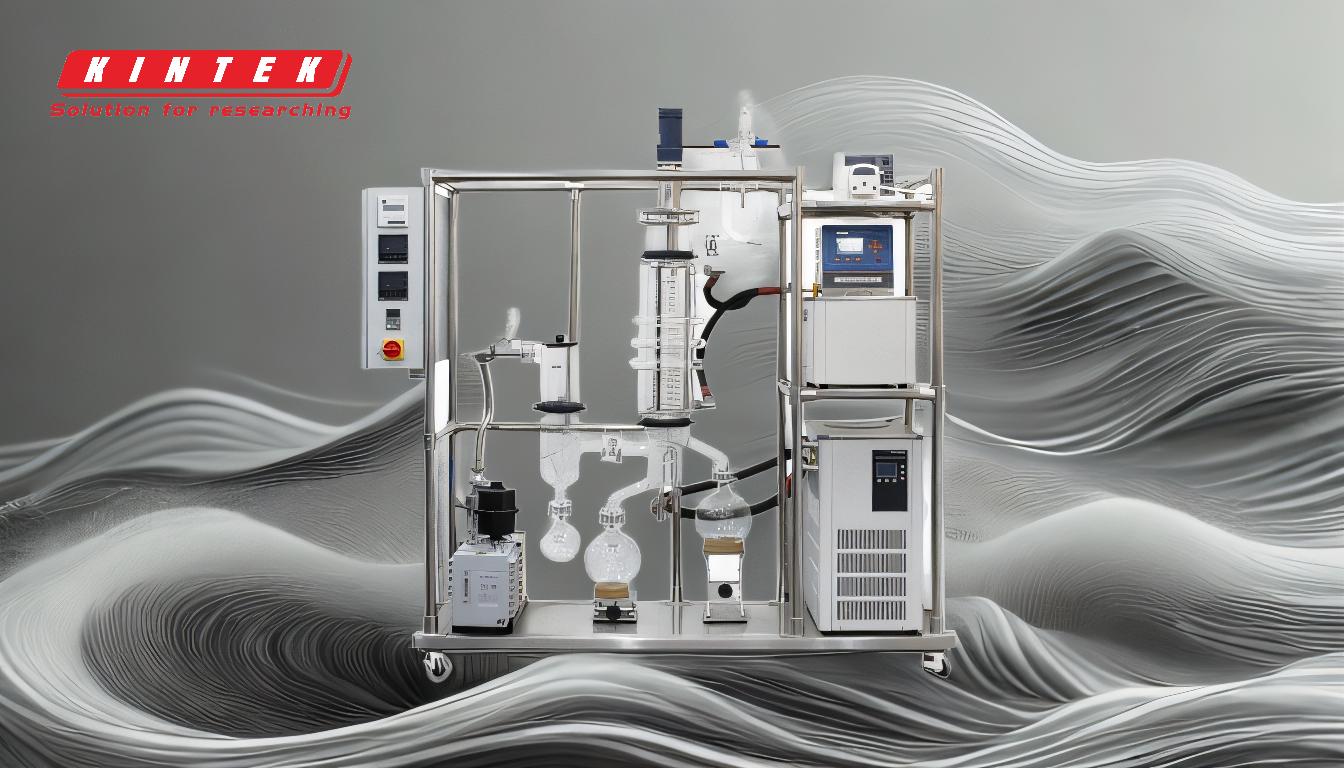
-
Basic Principle of Vacuum Evaporation:
- Vacuum evaporation operates by heating a material in a vacuum, which reduces the surrounding pressure and lowers the material's boiling point. This allows evaporation to occur at temperatures lower than those required at atmospheric pressure.
- The process is governed by the relationship between pressure and boiling point: as pressure decreases, the boiling point of the material also decreases.
-
Applications of Vacuum Evaporation:
- Wastewater Treatment: In this context, vacuum evaporation separates water from contaminants with high boiling points. The water evaporates at reduced pressure, leaving behind the contaminants, which can then be collected or disposed of.
- Thin-Film Deposition: In manufacturing and material science, vacuum evaporation is used to deposit thin films onto substrates. The material is heated until it evaporates, forming a vapor stream that condenses onto the substrate, creating a uniform layer.
-
Thermal Activation and Vapor Formation:
- When materials are heated in a vacuum, thermal energy activates the atomic structure, increasing the internal energy of the material. Once sufficient energy is reached to break atomic bonds, individual atoms or molecules are freed from the material matrix.
- These freed particles form a vapor stream, which can be directed to condense onto a substrate or collected for further processing.
-
Importance of Vacuum Conditions:
- The vacuum environment is crucial for preventing contamination and ensuring uniform deposition or separation. It eliminates the presence of air or other gases that could react with the material or interfere with the process.
- Vacuum conditions also ensure that the evaporated material travels unimpeded to the substrate or collection surface.
-
Advanced Techniques in Vacuum Evaporation:
- Vacuum-Vortex Evaporation: This technique involves swirling sample tubes to create a vortex, which increases the surface area of the sample and accelerates evaporation. However, it may be prone to sample loss and cross-contamination due to insufficient g forces.
- Incorporation of Vacuum Pumps and Heaters: Advanced systems use vacuum pumps and heaters to further enhance the evaporation process. A cold trap is often included to collect solvent gases, improving efficiency and reducing contamination.
-
Components of a Vacuum Evaporation System:
- Heat Source: Provides the necessary thermal energy to evaporate the material.
- Vacuum Chamber: Maintains the low-pressure environment required for the process.
- Cold Trap: Collects evaporated solvents or gases, preventing them from contaminating the system or the environment.
- Substrate or Collection Surface: The target surface where the evaporated material condenses or is collected.
-
Advantages of Vacuum Evaporation:
- Energy Efficiency: Lower boiling points reduce the energy required for evaporation.
- Precision and Uniformity: The vacuum environment ensures precise control over the deposition or separation process, resulting in uniform layers or clean separations.
- Versatility: Applicable in various fields, including wastewater treatment, semiconductor manufacturing, and material science.
-
Challenges and Considerations:
- Sample Loss and Contamination: In techniques like vacuum-vortex evaporation, insufficient g forces can lead to sample loss or cross-contamination.
- System Complexity: Advanced systems with vacuum pumps, heaters, and cold traps require careful design and maintenance.
- Material Compatibility: Not all materials are suitable for vacuum evaporation, as some may decompose or react under the required conditions.
By understanding these key points, one can appreciate the versatility and efficiency of vacuum evaporation as a method for separating or depositing materials in various industrial and scientific applications.
Summary Table:
Key Aspect | Description |
---|---|
Basic Principle | Heating materials in a vacuum lowers boiling points, enabling low-temperature evaporation. |
Applications | Wastewater treatment, thin-film deposition in manufacturing and material science. |
Thermal Activation | Heat breaks atomic bonds, freeing particles to form a vapor stream. |
Vacuum Importance | Prevents contamination and ensures uniform deposition or separation. |
Advanced Techniques | Vacuum-vortex evaporation, use of vacuum pumps, heaters, and cold traps. |
System Components | Heat source, vacuum chamber, cold trap, substrate/collection surface. |
Advantages | Energy efficiency, precision, uniformity, and versatility. |
Challenges | Sample loss, system complexity, and material compatibility issues. |
Discover how vacuum evaporation can optimize your processes—contact us today to learn more!