Ceramic mold casting is a precision casting process used to create intricate and detailed metal parts. It involves creating a ceramic mold by applying a ceramic slurry to a mold pattern, allowing it to dry, and then removing the dried slurry to form the mold. The mold is then cured by eliminating volatiles through low-temperature heating and hardened in a high-temperature furnace. This process is ideal for producing parts with fine details, smooth surfaces, and high dimensional accuracy. Below is a detailed breakdown of the key steps involved in ceramic mold casting.
Key Points Explained:
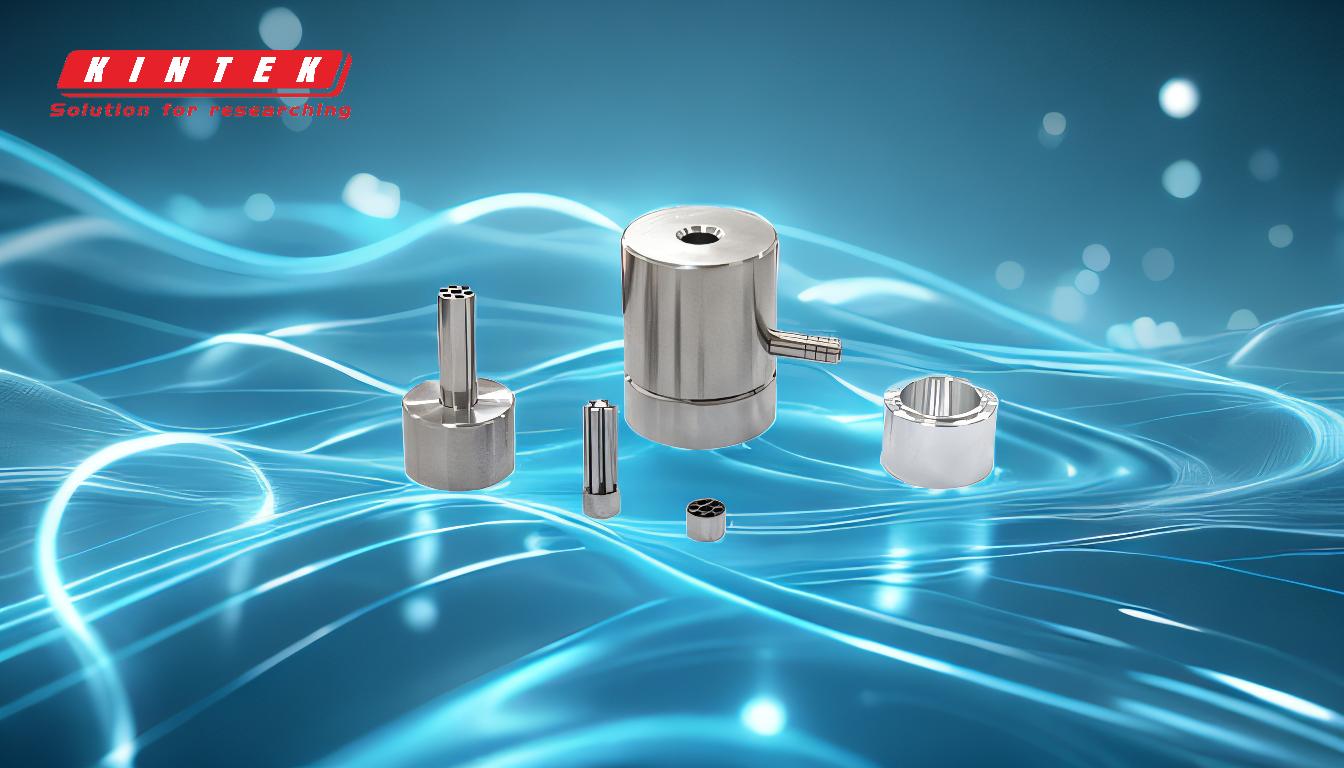
-
Apply and Solidify Ceramic Slurry on the Mold Pattern:
- The process begins with the preparation of a ceramic slurry, which is a mixture of fine ceramic particles and a liquid binder. This slurry is applied to a mold pattern, typically made of wax, plastic, or metal, which is shaped like the final product.
- The slurry is carefully coated onto the pattern to ensure even coverage and to capture all the fine details of the pattern. Once applied, the slurry is allowed to dry and solidify, forming a ceramic shell around the pattern.
-
Remove the Dried Slurry to Create a Mold for the Desired Item:
- After the ceramic slurry has dried and solidified, the next step is to remove the mold pattern. This is typically done by melting, burning, or dissolving the pattern material, leaving behind a hollow ceramic mold that replicates the shape of the original pattern.
- This step is crucial as it ensures that the mold accurately represents the final product's shape and details. The removal process must be done carefully to avoid damaging the delicate ceramic mold.
-
Eliminate Volatiles by Placing the Mold in a Low-Temperature Oven or Using a Flame Torch:
- Once the mold pattern is removed, the ceramic mold may still contain volatile substances, such as residual moisture or organic binders, which need to be eliminated before the mold can be used for casting.
- The mold is placed in a low-temperature oven or exposed to a flame torch to slowly drive off these volatiles. This step, known as dewaxing or burnout, ensures that the mold is free from any substances that could cause defects in the final cast part.
-
Harden the Mold in a High-Temperature Furnace:
- After the volatiles have been removed, the ceramic mold is further hardened by heating it in a high-temperature furnace. This step, known as sintering, strengthens the ceramic material and prepares it to withstand the high temperatures of the molten metal during casting.
- The sintering process also helps to eliminate any remaining porosity in the ceramic mold, ensuring a smooth and defect-free surface on the final cast part.
-
Pouring Molten Metal into the Ceramic Mold:
- Once the ceramic mold is fully prepared, it is ready for the casting process. Molten metal is poured into the mold, filling the cavity and taking on the shape of the original pattern.
- The mold is designed to withstand the high temperatures of the molten metal, ensuring that the final part retains all the intricate details and dimensions of the original pattern.
-
Cooling and Removing the Cast Part:
- After the molten metal has been poured into the mold, it is allowed to cool and solidify. Once the metal has cooled, the ceramic mold is carefully broken away to reveal the final cast part.
- The ceramic mold is typically destroyed during this process, as it is designed to be a single-use mold. However, the high level of detail and precision achieved with ceramic mold casting makes it a valuable process for producing complex and high-quality metal parts.
-
Post-Casting Finishing:
- After the cast part is removed from the mold, it may undergo additional finishing processes, such as grinding, polishing, or heat treatment, to achieve the desired surface finish and mechanical properties.
- These finishing steps ensure that the final part meets the required specifications and is ready for use in its intended application.
In summary, ceramic mold casting is a highly precise and detailed casting process that involves creating a ceramic mold from a pattern, curing and hardening the mold, and then casting molten metal into the mold to produce a final part. The process is ideal for creating complex and intricate parts with high dimensional accuracy and smooth surfaces.
Summary Table:
Step | Description |
---|---|
1. Apply Ceramic Slurry | Coat a mold pattern with ceramic slurry to capture fine details. |
2. Remove Mold Pattern | Melt or dissolve the pattern to leave a hollow ceramic mold. |
3. Eliminate Volatiles | Use low-temperature heating or a flame torch to remove residual substances. |
4. Harden Mold | Sinter the mold in a high-temperature furnace for strength and smoothness. |
5. Pour Molten Metal | Fill the ceramic mold with molten metal to form the final part. |
6. Cool and Remove Part | Break away the ceramic mold to reveal the finished cast part. |
7. Post-Casting Finishing | Grind, polish, or heat-treat the part for desired properties. |
Discover how ceramic mold casting can elevate your production—contact our experts today!