The mold press process is a manufacturing technique used to shape materials into desired forms using heat and pressure. It involves placing a material, often a thermosetting or thermoplastic resin, into a mold cavity. The mold is then closed, and pressure is applied to ensure the material conforms to the mold's shape. Heat and pressure are maintained until the material cures or solidifies, resulting in a finished product. This process is widely used in industries such as automotive, aerospace, and consumer goods for producing high-strength, durable components.
Key Points Explained:
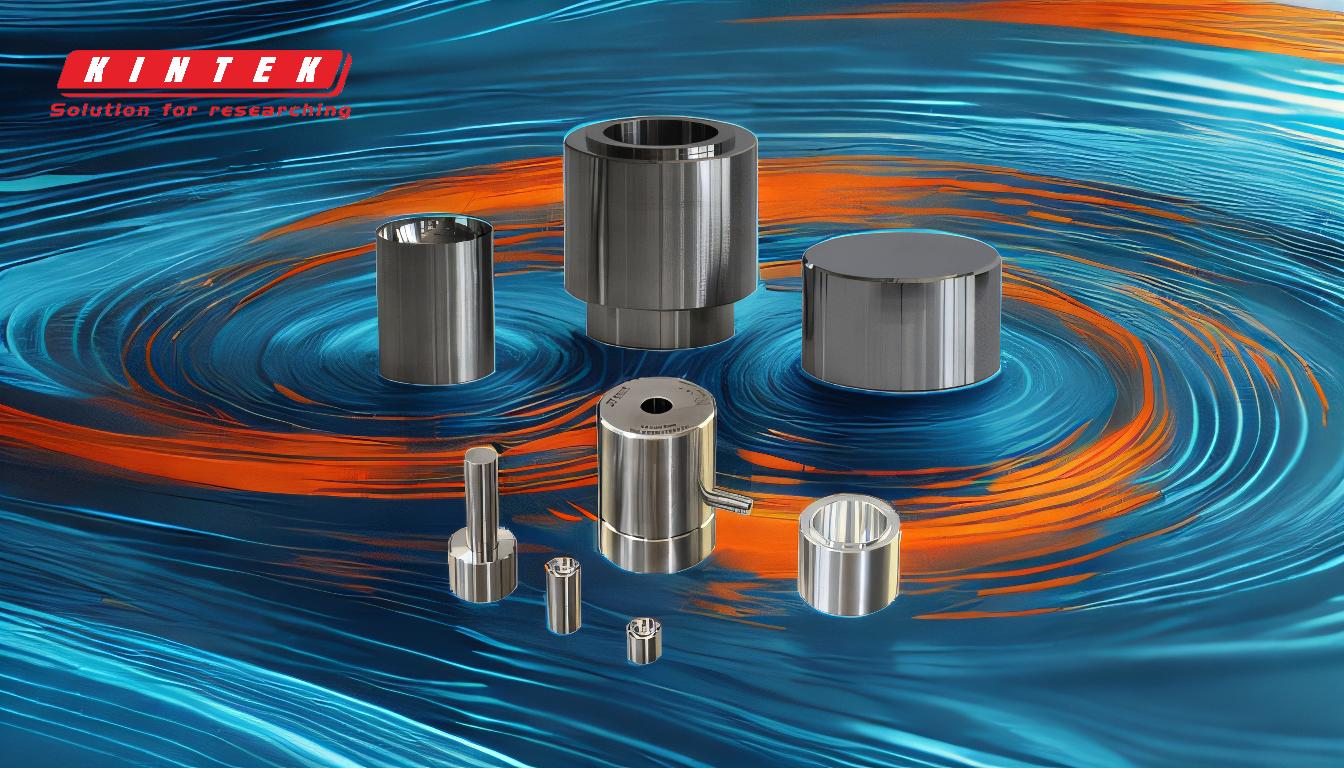
-
Mold Preparation:
- The mold is designed to match the desired shape of the final product. It typically consists of two halves that can be opened and closed.
- The mold cavity is cleaned and prepared to ensure the material flows evenly and adheres properly.
-
Material Selection:
- Thermosetting Resins: These are partially cured materials that harden permanently when heated. They are commonly used in mold pressing due to their high strength and durability.
- Thermoplastic Resins: These materials can be melted and reshaped multiple times. They are used when flexibility or recyclability is required.
- Other materials, such as composites or rubber, may also be used depending on the application.
-
Material Placement:
- The selected material is placed into the mold cavity. This can be in the form of pellets, sheets, or preforms, depending on the material type and the complexity of the part.
-
Mold Closure:
- The mold is closed, and pressure is applied to ensure the material fills the entire cavity. This step is crucial for achieving the desired shape and surface finish.
-
Application of Heat and Pressure:
- Heat is applied to the mold to soften or cure the material. The temperature and duration depend on the material type and thickness.
- Pressure is maintained to ensure the material conforms to the mold's contours and to eliminate any air pockets or voids.
-
Curing or Solidification:
- For thermosetting resins, the heat causes a chemical reaction that hardens the material permanently.
- For thermoplastics, the material solidifies as it cools.
- The curing or solidification process ensures the final product has the required mechanical properties and dimensional stability.
-
Mold Opening and Part Removal:
- Once the material has cured or solidified, the mold is opened, and the finished part is removed.
- The part may undergo additional post-processing steps, such as trimming, painting, or surface finishing, depending on the application.
-
Quality Control:
- The finished part is inspected for defects, such as warping, voids, or surface imperfections.
- Dimensional accuracy and mechanical properties are verified to ensure the part meets specifications.
-
Advantages of Mold Pressing:
- High Precision: Mold pressing allows for the production of complex shapes with tight tolerances.
- Material Efficiency: The process minimizes material waste, as excess material can often be reused.
- Scalability: Mold pressing is suitable for both low-volume and high-volume production.
-
Applications:
- Automotive: Used for manufacturing dashboards, bumpers, and interior trim.
- Aerospace: Produces lightweight, high-strength components for aircraft.
- Consumer Goods: Used for items such as kitchenware, electronic housings, and toys.
By following this structured process, mold pressing enables the production of high-quality, durable components across a wide range of industries.
Summary Table:
Key Step | Description |
---|---|
Mold Preparation | Design and clean the mold to ensure proper material flow and adhesion. |
Material Selection | Choose thermosetting or thermoplastic resins based on strength and flexibility. |
Material Placement | Place material (pellets, sheets, or preforms) into the mold cavity. |
Mold Closure | Close the mold and apply pressure for proper shaping. |
Heat & Pressure | Apply heat and pressure to cure or solidify the material. |
Curing/Solidification | Harden thermosetting resins or cool thermoplastics for final strength. |
Part Removal | Open the mold and remove the finished part. |
Quality Control | Inspect for defects and verify dimensional accuracy. |
Advantages | High precision, material efficiency, and scalability. |
Applications | Automotive, aerospace, and consumer goods manufacturing. |
Discover how the mold press process can optimize your production—contact our experts today!