Vacuum evaporation is a process used in various applications, including wastewater treatment, thin-film deposition, and solvent removal. It involves reducing the pressure in a system to lower the boiling point of a liquid, allowing it to evaporate at a lower temperature. This method is particularly useful for separating water from contaminants with high boiling points or for depositing thin films in a controlled environment. The process can be enhanced with techniques like thermal evaporation or vacuum-vortex evaporation, depending on the specific application. Below, the key aspects of vacuum evaporation are explained in detail.
Key Points Explained:
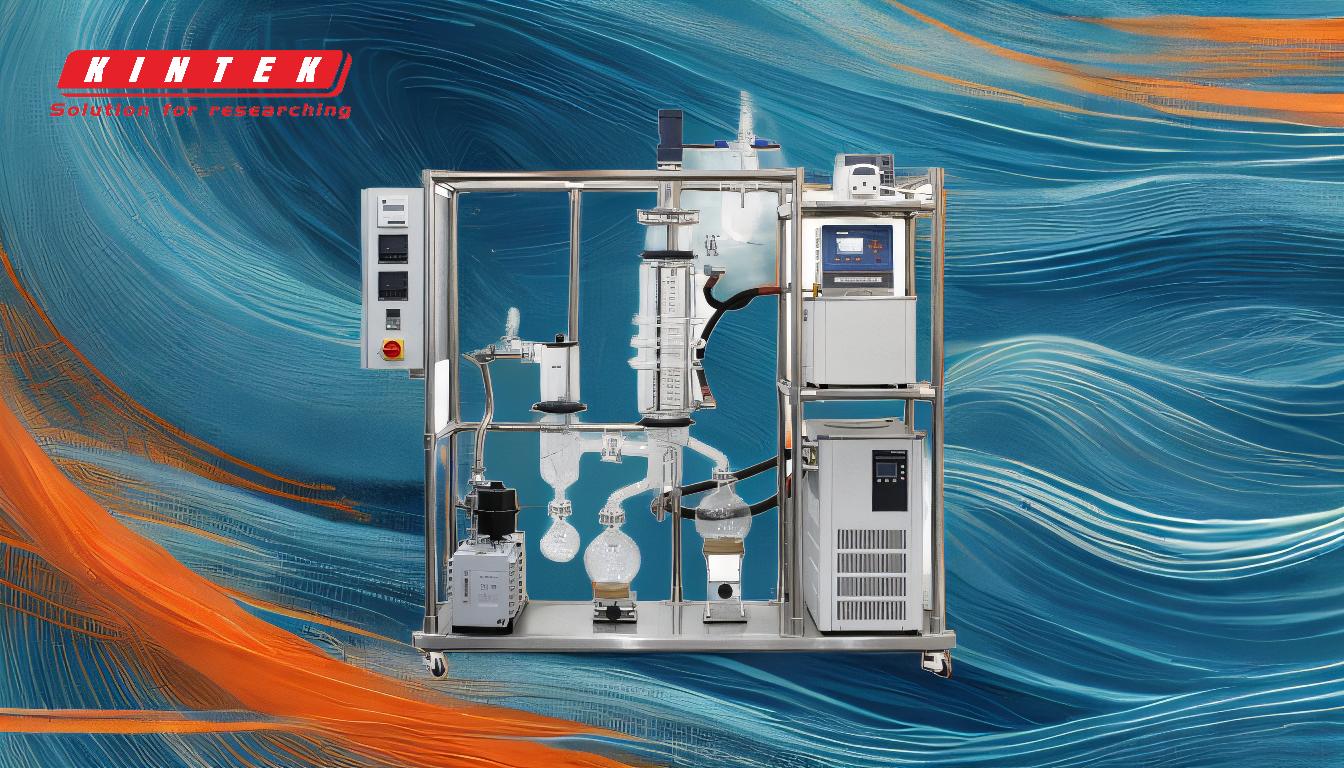
-
Principle of Vacuum Evaporation:
- Vacuum evaporation relies on reducing the pressure in a system to lower the boiling point of a liquid. By creating a vacuum, the liquid can evaporate at a lower temperature, which is especially beneficial for heat-sensitive materials or substances with high boiling points. This principle is widely used in applications like wastewater treatment, where water is separated from contaminants, and in thin-film deposition, where materials are evaporated and condensed onto a substrate.
-
Applications of Vacuum Evaporation:
- Wastewater Treatment: In wastewater treatment, vacuum evaporation is used to separate water from contaminants with high boiling points. The process allows for the efficient removal of water, leaving behind concentrated contaminants for disposal or further treatment.
- Thin-Film Deposition: In industries like electronics and optics, vacuum evaporation is used to deposit thin films of materials onto substrates. The process involves heating the material in a vacuum chamber until it evaporates, forming a vapor stream that condenses onto the substrate.
- Solvent Removal: In laboratories, vacuum evaporation is used to remove solvents from samples. Techniques like vacuum-vortex evaporation enhance the process by creating a vortex to increase the surface area for faster evaporation.
-
Process of Vacuum Evaporation:
- Pressure Reduction: The first step involves reducing the pressure in the system, typically using a vacuum pump. This lowers the boiling point of the liquid, allowing it to evaporate at a lower temperature.
- Evaporation: Once the pressure is reduced, the liquid begins to evaporate. In thermal evaporation, the material is heated to produce vapor pressure, while in vacuum-vortex evaporation, a vortex is created to increase the surface area for faster evaporation.
- Condensation: The evaporated material is then condensed, either in a separate chamber or on a substrate. In wastewater treatment, the condensed water is collected, while in thin-film deposition, the material forms a thin layer on the substrate.
-
Techniques to Enhance Vacuum Evaporation:
- Thermal Evaporation: This technique involves heating the material in a high vacuum chamber until it evaporates. It is commonly used in thin-film deposition and requires precise control of temperature and pressure.
- Vacuum-Vortex Evaporation: This technique uses a vortex to increase the surface area of the sample, promoting faster evaporation. Advanced systems incorporate vacuum pumps and heaters to accelerate the process and include cold traps to collect solvent gases.
-
Advantages of Vacuum Evaporation:
- Lower Temperature Evaporation: By reducing the pressure, vacuum evaporation allows liquids to evaporate at lower temperatures, minimizing the risk of thermal degradation.
- Energy Efficiency: The process reduces or eliminates the need for external heat, making it more energy-efficient compared to traditional evaporation methods.
- Versatility: Vacuum evaporation can be applied to a wide range of materials and processes, from wastewater treatment to thin-film deposition.
-
Challenges and Considerations:
- Equipment Complexity: Vacuum evaporation systems require specialized equipment, including vacuum pumps, heaters, and cold traps, which can be costly and complex to operate.
- Sample Loss and Contamination: In techniques like vacuum-vortex evaporation, there is a risk of sample loss or cross-contamination if the system is not properly designed.
- Precision Control: Achieving the desired results in applications like thin-film deposition requires precise control of pressure, temperature, and evaporation rates.
In summary, vacuum evaporation is a versatile and efficient process used in various industries for separating liquids, depositing thin films, and removing solvents. By reducing pressure and lowering the boiling point of liquids, it enables operations at lower temperatures, making it ideal for heat-sensitive materials. However, the process requires specialized equipment and careful control to achieve optimal results.
Summary Table:
Key Aspect | Details |
---|---|
Principle | Reduces pressure to lower boiling point, enabling low-temperature evaporation. |
Applications | Wastewater treatment, thin-film deposition, solvent removal. |
Techniques | Thermal evaporation, vacuum-vortex evaporation. |
Advantages | Lower temperature evaporation, energy efficiency, versatility. |
Challenges | Equipment complexity, sample loss, precision control. |
Learn how vacuum evaporation can optimize your processes—contact us today for expert advice!