Sputtering is a physical vapor deposition (PVD) process used to deposit thin films of materials onto a substrate. It involves bombarding a target material with high-energy ions, typically from an inert gas like argon, in a vacuum chamber. The collision of these ions with the target causes atoms or molecules to be ejected from the target's surface. These ejected particles then travel through the vacuum and deposit onto a substrate, forming a thin film. The process is widely used in industries such as semiconductor manufacturing, optics, and surface finishing due to its ability to produce highly uniform, dense, and adherent thin films.
Key Points Explained:
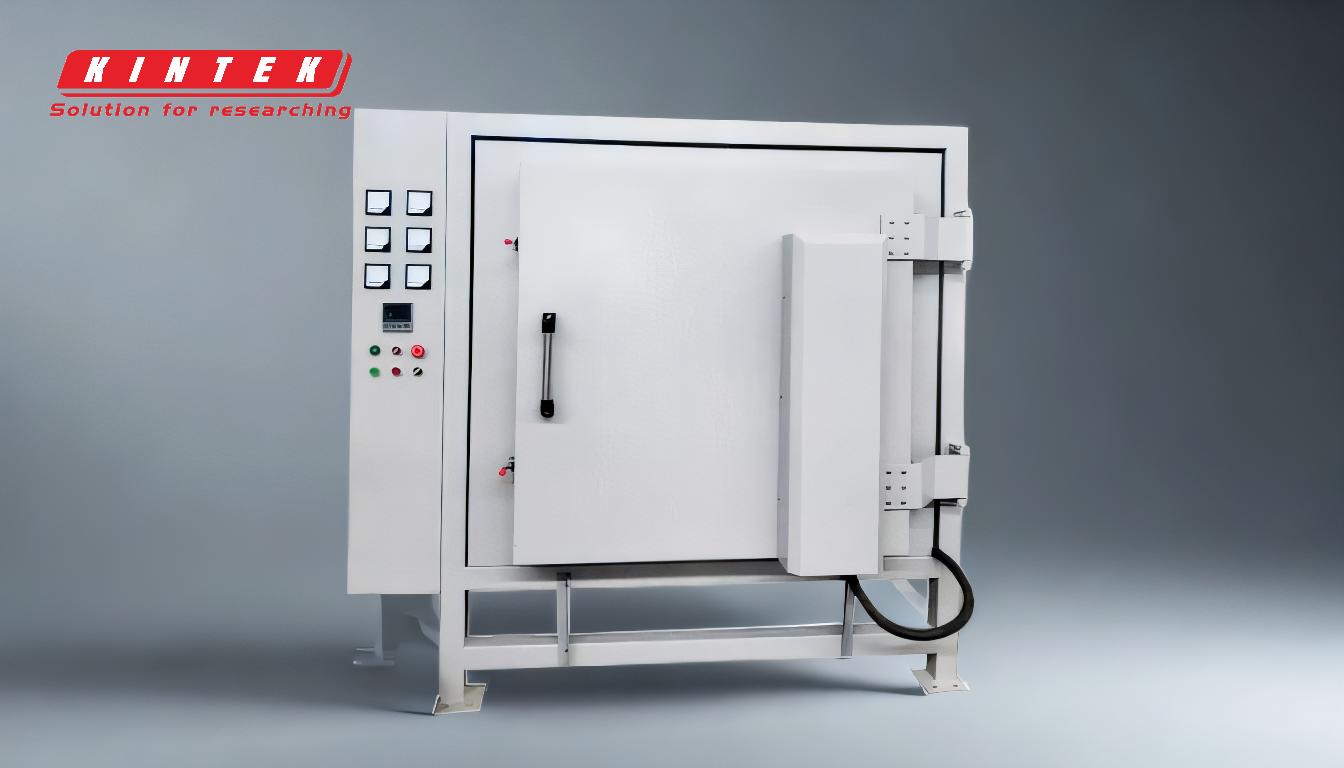
-
Definition and Purpose of Sputtering:
- Sputtering is a physical vapor deposition (PVD) technique used to deposit thin films of materials onto a substrate.
- The primary purpose is to create thin films with excellent uniformity, density, and adhesion, making it ideal for applications in semiconductor processing, precision optics, and surface finishing.
-
Components Involved in the Sputtering Process:
- Target Material: The material that will be deposited as a thin film. It is typically a metallic or oxide material.
- Substrate: The surface onto which the thin film is deposited. Common substrates include glass, silicon wafers, and other solid materials.
- Vacuum Chamber: The environment where the sputtering process takes place. It is essential to maintain a vacuum to prevent contamination and allow the free movement of particles.
- Inert Gas (usually Argon): Introduced into the vacuum chamber to create a plasma when a high voltage is applied.
-
Mechanism of Sputtering:
- Ion Generation: A high voltage is applied to the inert gas (e.g., argon) in the vacuum chamber, ionizing the gas and creating a plasma of positively charged ions (e.g., Ar+).
- Ion Bombardment: The positively charged ions are accelerated towards the negatively charged target material (cathode) due to the applied electric field.
- Ejection of Target Atoms: When the ions collide with the target, they transfer their kinetic energy to the target atoms, causing them to be ejected from the surface in the form of neutral particles (atoms, clusters, or molecules).
- Deposition on Substrate: The ejected particles travel through the vacuum and deposit onto the substrate, forming a thin film.
-
Key Advantages of Sputtering:
- Uniformity: Sputtering produces thin films with excellent uniformity, which is crucial for applications requiring precise thickness control.
- Density and Adhesion: The films deposited via sputtering are dense and have strong adhesion to the substrate, making them durable and long-lasting.
- Material Versatility: Sputtering can be used with a wide range of materials, including metals, alloys, oxides, and compounds, allowing for diverse applications.
- High Purity: The process can achieve ultra-high purity films, which is essential for semiconductor and optical applications.
-
Applications of Sputtering:
- Semiconductor Industry: Sputtering is used to deposit thin films of metals and dielectrics onto silicon wafers for the fabrication of integrated circuits.
- Optical Coatings: The process is employed to create anti-reflective, reflective, and protective coatings on lenses, mirrors, and other optical components.
- Surface Finishing: Sputtering is used to apply decorative and functional coatings on various products, including automotive parts, jewelry, and consumer electronics.
- Magnetic Storage: Thin films deposited via sputtering are used in the production of magnetic storage media, such as hard drives.
-
Process Conditions and Control:
- Vacuum Environment: Sputtering requires a high vacuum to minimize contamination and ensure the free movement of particles.
- Gas Pressure: The pressure of the inert gas (e.g., argon) must be carefully controlled to optimize the sputtering rate and film quality.
- Voltage and Power: The applied voltage and power influence the energy of the ions and the rate at which target atoms are ejected.
- Substrate Temperature: The temperature of the substrate can affect the film's microstructure and properties, so it is often controlled during the deposition process.
-
Challenges and Considerations:
- Target Erosion: Continuous bombardment of the target can lead to its erosion, requiring periodic replacement or maintenance.
- Film Stress: The deposited films may experience stress, which can affect their adhesion and mechanical properties. Proper process control is necessary to minimize stress.
- Contamination: Maintaining a clean vacuum environment is crucial to prevent contamination, which can degrade the quality of the thin film.
In summary, sputtering is a versatile and precise method for depositing thin films with excellent uniformity, density, and adhesion. It involves bombarding a target material with high-energy ions in a vacuum chamber, causing atoms to be ejected and deposited onto a substrate. The process is widely used in industries such as semiconductor manufacturing, optics, and surface finishing, where high-quality thin films are essential.
Summary Table:
Key Aspect | Details |
---|---|
Definition | Physical vapor deposition (PVD) technique for thin film deposition. |
Purpose | Creates uniform, dense, and adherent thin films for precision applications. |
Key Components | Target material, substrate, vacuum chamber, inert gas (e.g., argon). |
Mechanism | High-energy ions bombard target, ejecting atoms that deposit on substrate. |
Advantages | Uniformity, density, adhesion, material versatility, high purity. |
Applications | Semiconductors, optical coatings, surface finishing, magnetic storage. |
Process Conditions | Vacuum environment, controlled gas pressure, voltage, power, temperature. |
Challenges | Target erosion, film stress, contamination control. |
Discover how sputtering can enhance your precision applications—contact our experts today!