Vacuum evaporation is a versatile technique used in various industries, primarily for separating water from contaminants, concentrating solutions, and depositing thin films. It operates under reduced pressure to lower the boiling point of liquids, making it suitable for heat-sensitive materials. The process involves heating a material in a vacuum environment, which allows for efficient evaporation and condensation. It is widely applied in wastewater treatment, microelectronics, and laboratory settings. The method is enhanced by advanced technologies like vacuum pumps, condensers, and cold traps to improve efficiency and prevent contamination.
Key Points Explained:
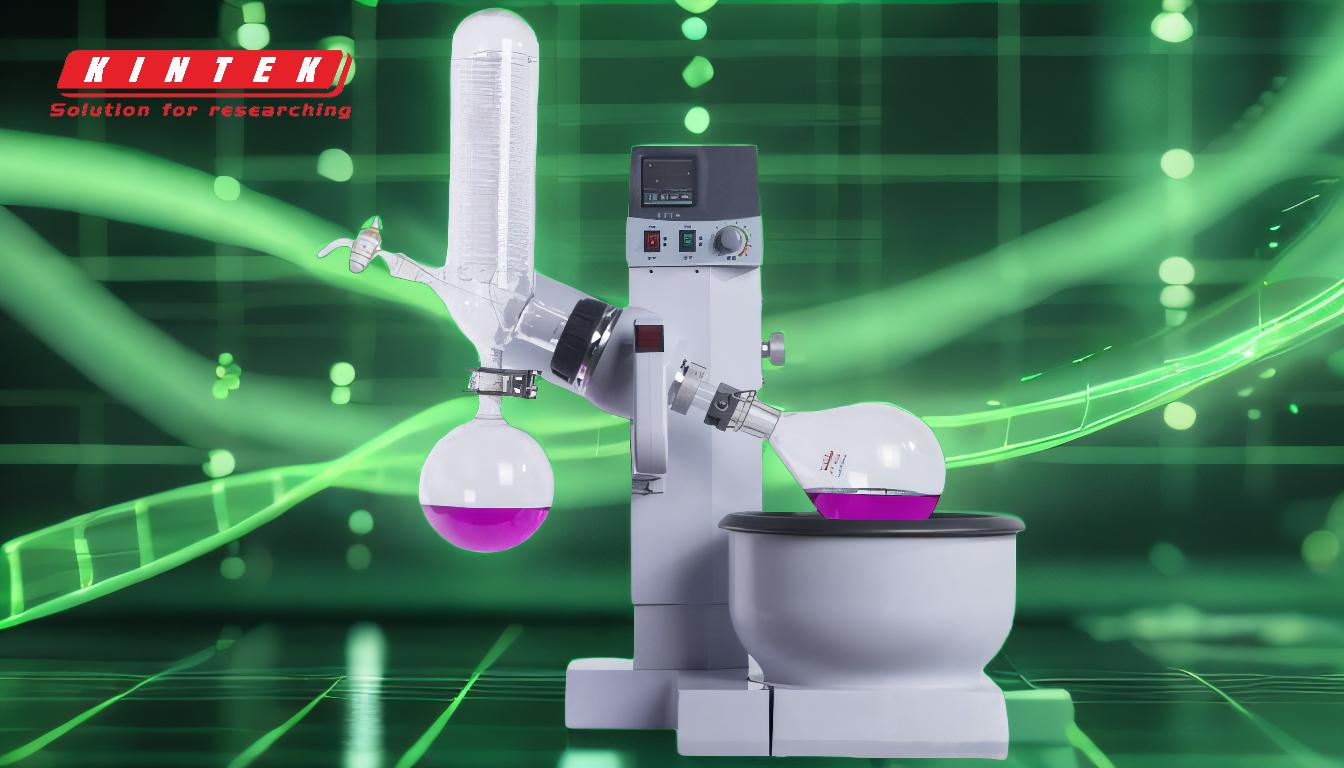
-
Definition and Purpose of Vacuum Evaporation:
- Vacuum evaporation is a process that separates water from contaminants or concentrates solutions by evaporating the liquid under reduced pressure.
- It is used in wastewater treatment to reduce volume and concentrate dissolved substances.
- In microelectronics, it deposits thin films on substrates for creating components like resistors, capacitors, and interconnections.
-
How Vacuum Evaporation Works:
- The process involves reducing the pressure in the system, which lowers the boiling point of the liquid.
- This allows evaporation to occur at lower temperatures, protecting heat-sensitive materials.
- Mechanical or steam jet ejector vacuum pumps are used to create the necessary reduced pressure.
- Condensers are employed to collect and condense the evaporated vapors.
-
Applications of Vacuum Evaporation:
- Wastewater Treatment: Separates water from high-boiling-point contaminants, reducing wastewater volume and concentrating solutions.
- Microelectronics: Deposits thin films for active components, metal interconnections, and insulating dielectrics.
- Laboratory Use: Evaporates heat-sensitive liquids efficiently, often using advanced vortex evaporators with vacuum pumps and cold traps.
-
Advantages of Vacuum Evaporation:
- Lower Boiling Points: Enables evaporation at reduced temperatures, protecting sensitive materials.
- Energy Efficiency: Requires less energy compared to traditional evaporation methods.
- Versatility: Applicable in diverse industries, from wastewater treatment to high-precision electronics.
-
Advanced Techniques and Equipment:
- Vacuum-Vortex Evaporation: Combines swirling motion with vacuum to increase surface area and speed up evaporation. However, it may be prone to sample loss and cross-contamination.
- Cold Traps: Used to collect solvent gases, preventing contamination and improving efficiency.
- Heaters and Vacuum Pumps: Enhance the evaporation process by providing controlled heating and maintaining reduced pressure.
-
Challenges and Considerations:
- Sample Loss: Advanced vortex evaporators may still face issues with sample loss due to insufficient g force.
- Cross-Contamination: Proper design and cold traps are essential to minimize contamination risks.
- Equipment Complexity: Requires specialized equipment like vacuum pumps, condensers, and heaters, which can increase costs.
By understanding these key points, equipment and consumable purchasers can make informed decisions about the suitability of vacuum evaporation methods for their specific applications, ensuring efficient and cost-effective solutions.
Summary Table:
Aspect | Details |
---|---|
Definition | Process of separating water from contaminants or concentrating solutions under reduced pressure. |
Key Applications | Wastewater treatment, microelectronics (thin film deposition), lab use. |
Advantages | Lower boiling points, energy efficiency, versatility across industries. |
Equipment | Vacuum pumps, condensers, cold traps, heaters. |
Challenges | Sample loss, cross-contamination, equipment complexity. |
Discover how vacuum evaporation can optimize your processes—contact us today for expert guidance!