Casting is a manufacturing process where molten material is poured into a mold to create a desired shape upon solidification. The type of machine used for casting depends on the material being cast, the desired precision, and the production scale. Common casting machines include die casting machines, arc melting systems, open flame casting setups, and induction melting machines. Each machine is designed to handle specific materials and processes, such as high-pressure die casting for metals or induction melting for precious alloys. The choice of machine is critical to achieving the desired quality, efficiency, and cost-effectiveness in the casting process.
Key Points Explained:
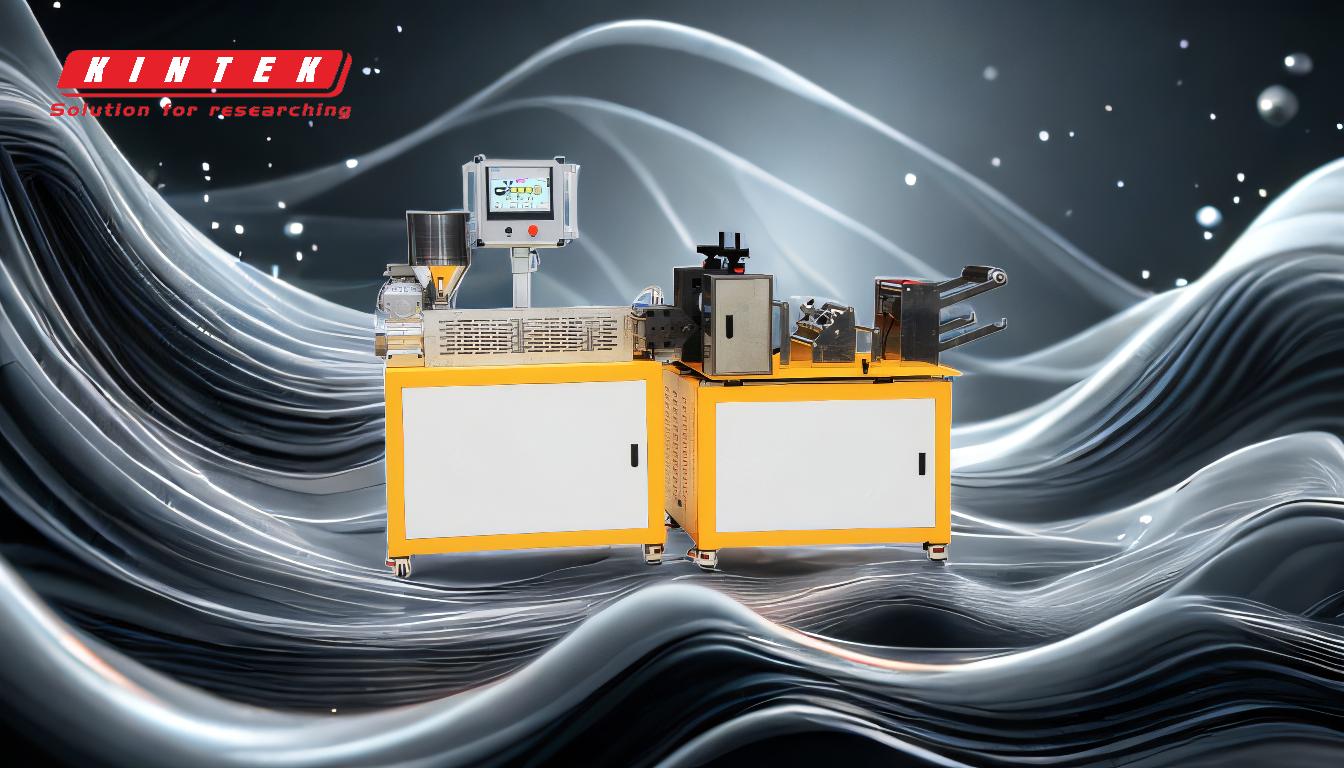
-
Die Casting Machines:
- Function: Die casting machines are used to inject molten metal into a precision mold cavity under high pressure. This process is ideal for producing complex, high-precision metal parts with excellent surface finish and dimensional accuracy.
- Mechanism: These machines use either pneumatic or hydraulic actuators to generate the necessary pressure. The molten metal is forced into the mold at high speed, ensuring it fills every detail of the cavity.
- Applications: Commonly used for casting metals like aluminum, zinc, and magnesium, die casting machines are widely employed in automotive, aerospace, and consumer electronics industries.
-
Arc Melting Systems:
- Function: Arc melting is primarily used for casting high-melting-point metals such as titanium. It involves creating an electric arc between a tungsten electrode and the metal, generating intense heat to melt the material.
- Mechanism: The electric arc is produced by passing a high-current discharge through a gas (usually argon) between the electrode and the metal. This method ensures precise control over the melting process.
- Applications: Arc melting is essential in industries requiring high-purity metals, such as aerospace, medical implants, and advanced manufacturing.
-
Open Flame Casting:
- Function: Open flame casting is used for melting and casting precious and non-precious alloys. It employs a precisely adjusted flame fueled by propane or butane mixed with oxygen.
- Mechanism: The flame directly heats the metal ingots, melting them in a controlled environment. This method is suitable for smaller-scale casting operations.
- Applications: Commonly used in jewelry making and dental laboratories, open flame casting is ideal for working with gold, silver, and other precious metals.
-
Induction Melting Machines:
- Function: Induction melting machines use alternating current (AC) induction coils to generate heat within the metal ingots. This method is highly efficient and provides precise temperature control.
- Mechanism: The AC induction coils create a magnetic field that induces eddy currents in the metal, causing it to heat up and melt. The process is water-cooled to maintain stability and prevent overheating.
- Applications: Induction melting is widely used for casting precious metals, stainless steel, and other alloys in industries such as automotive, aerospace, and electronics.
-
Resistance Heating:
- Function: Resistance heating is typically used for melting precious metals. It involves passing an electric current through a resistive element, which generates heat to melt the metal.
- Mechanism: The resistive element is in direct contact with the metal, ensuring efficient heat transfer. This method is suitable for small-scale operations and provides excellent control over the melting process.
- Applications: Resistance heating is commonly used in jewelry making, dental labs, and other applications requiring precise melting of precious metals.
By understanding the specific functions, mechanisms, and applications of these casting machines, purchasers can make informed decisions based on their material requirements, production scale, and desired outcomes. Each machine offers unique advantages, making it essential to choose the right one for the specific casting process.
Summary Table:
Machine Type | Function | Applications |
---|---|---|
Die Casting Machines | Inject molten metal into molds under high pressure for precision parts | Automotive, aerospace, consumer electronics |
Arc Melting Systems | Melt high-melting-point metals like titanium using electric arcs | Aerospace, medical implants, advanced manufacturing |
Open Flame Casting | Melt precious and non-precious alloys with a controlled flame | Jewelry making, dental labs |
Induction Melting | Generate heat using AC induction coils for precise temperature control | Precious metals, stainless steel, automotive, aerospace, electronics |
Resistance Heating | Melt precious metals by passing electric current through resistive elements | Jewelry making, dental labs |
Need help selecting the right casting machine? Contact our experts today for personalized advice!