To deposit ZnO thin films, a magnetron sputtering system is commonly used due to its efficiency, uniformity, and ability to produce high-quality films. Magnetron sputtering is a physical vapor deposition (PVD) technique that uses a magnetic field to confine electrons near the target surface, enhancing ionization and sputtering efficiency. The working principle involves bombarding a ZnO target with energetic ions (usually argon) in a vacuum chamber, causing atoms to be ejected from the target and deposited onto a substrate. This process is highly controllable, allowing for precise thickness and composition of the ZnO thin film. Below, the key points of the magnetron sputtering system and its working principle are explained in detail, along with a conceptual diagram.
Key Points Explained:
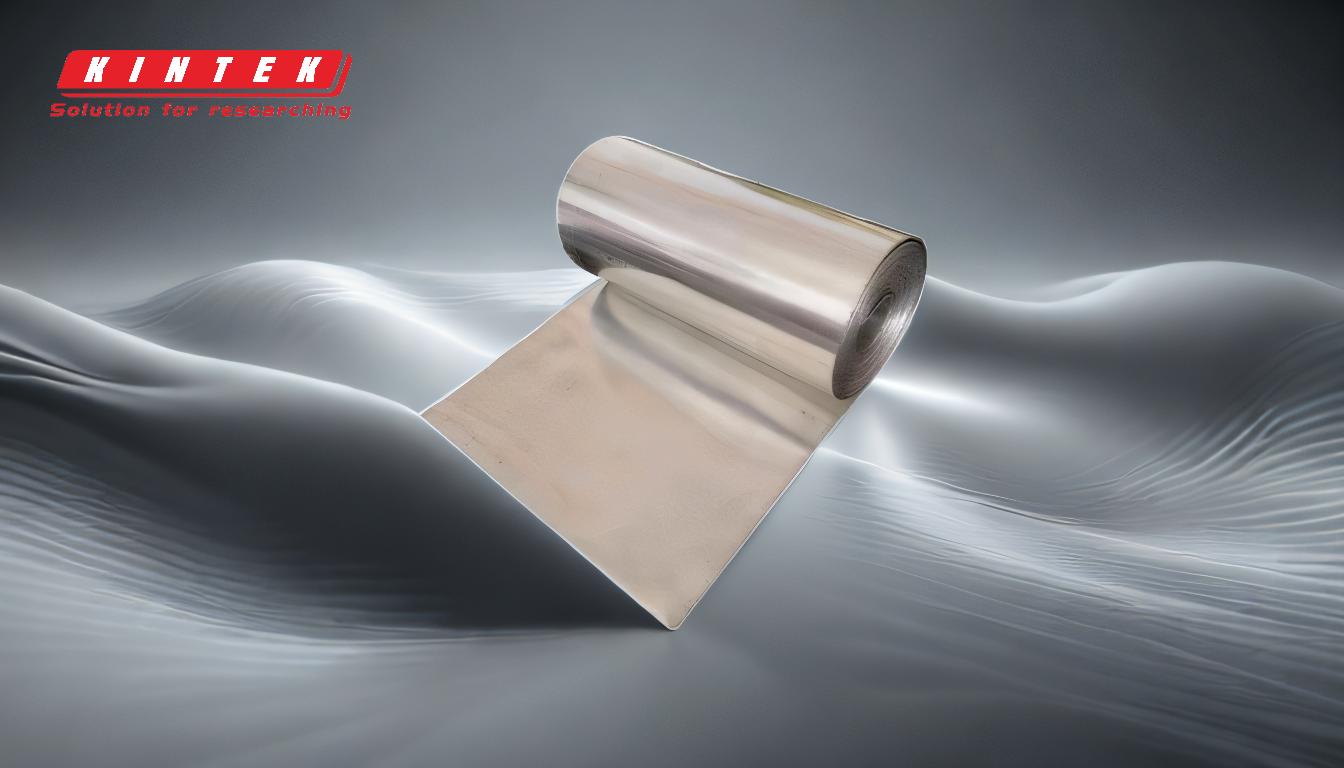
-
Overview of Magnetron Sputtering System:
- Magnetron sputtering is a widely used technique for depositing thin films, including ZnO, due to its high deposition rates, excellent film uniformity, and ability to operate at relatively low temperatures.
- The system consists of a vacuum chamber, a ZnO target, a substrate holder, a magnetron (with permanent magnets or electromagnets), a power supply (DC or RF), and a gas inlet for introducing argon gas.
-
Working Principle of Magnetron Sputtering:
- Vacuum Chamber: The process begins by evacuating the chamber to create a high-vacuum environment, reducing contamination and ensuring efficient sputtering.
- Introduction of Argon Gas: Argon gas is introduced into the chamber at a controlled pressure. Argon is chosen because it is inert and does not react with the target material.
- Ionization of Argon Gas: A high-voltage power supply is applied between the target (cathode) and the substrate holder (anode), creating a plasma. Electrons collide with argon atoms, ionizing them and forming positively charged argon ions.
- Magnetic Field Confinement: The magnetron generates a magnetic field near the target surface, trapping electrons in a circular path. This increases the probability of collisions between electrons and argon atoms, enhancing ionization and sputtering efficiency.
- Sputtering of ZnO Target: The energized argon ions are accelerated toward the ZnO target, striking it with high energy. This causes atoms from the ZnO target to be ejected (sputtered) due to momentum transfer.
- Deposition on Substrate: The ejected ZnO atoms travel through the vacuum and deposit onto the substrate, forming a thin film. The substrate can be heated or cooled depending on the desired film properties.
-
Advantages of Magnetron Sputtering for ZnO Thin Films:
- High Deposition Rate: The magnetic field increases the density of the plasma, leading to faster deposition rates.
- Uniform Film Thickness: The system allows for precise control over deposition parameters, ensuring uniform film thickness.
- Low Substrate Temperature: Magnetron sputtering can deposit high-quality ZnO films at relatively low temperatures, making it suitable for temperature-sensitive substrates.
- Scalability: The process is scalable for industrial applications, allowing for large-area deposition.
-
Diagram of Magnetron Sputtering System: Below is a conceptual diagram of a magnetron sputtering system:
+---------------------------+ | Vacuum Chamber | | | | +-------------------+ | | | ZnO Target | | | | (Cathode) | | | +-------------------+ | | | | | | Magnetic Field | | | (Circular Path)| | | | | +-------------------+ | | | Substrate | | | | (Anode) | | | +-------------------+ | | | | Argon Gas Inlet | +---------------------------+
-
Key Parameters for ZnO Thin Film Deposition:
- Power Supply: DC or RF power is used to generate the plasma. RF power is preferred for insulating targets like ZnO.
- Gas Pressure: The argon gas pressure is optimized to balance sputtering efficiency and film quality.
- Substrate Temperature: The temperature can be adjusted to control crystallinity and stress in the ZnO film.
- Target-to-Substrate Distance: This distance affects the energy of the sputtered atoms and the uniformity of the film.
-
Applications of ZnO Thin Films:
- Optoelectronics: ZnO films are used in solar cells, LEDs, and transparent conductive electrodes.
- Sensors: ZnO’s piezoelectric properties make it ideal for gas and biosensors.
- Coatings: ZnO films are used for anti-reflective and protective coatings.
In summary, magnetron sputtering is the preferred method for depositing ZnO thin films due to its efficiency, controllability, and ability to produce high-quality films. The system’s working principle involves creating a plasma, confining electrons with a magnetic field, and sputtering ZnO atoms onto a substrate. This process is widely used in various applications, from optoelectronics to sensors, making it a versatile and essential technique in thin film deposition.
Summary Table:
Key Aspect | Details |
---|---|
System Components | Vacuum chamber, ZnO target, substrate holder, magnetron, power supply, gas inlet |
Working Principle | Ionization of argon gas, magnetic field confinement, sputtering of ZnO target |
Advantages | High deposition rate, uniform film thickness, low substrate temperature, scalability |
Key Parameters | Power supply (DC/RF), gas pressure, substrate temperature, target-to-substrate distance |
Applications | Optoelectronics, sensors, anti-reflective coatings |
Interested in magnetron sputtering for ZnO thin films? Contact us today to learn more!