Sputtering targets are essential components in various industries, including microelectronics, renewable energy, and decorative coatings. They are manufactured by specialized companies using a wide range of materials, such as pure metals, alloys, and compounds like oxides or nitrides. One notable manufacturer is American Elements, which produces sputtering targets from advanced magnetic materials like samarium cobalt and neodymium iron boron alloy. The choice of material depends on the specific application, with metals like aluminum, copper, and titanium being commonly used. These targets are critical for depositing thin films onto substrates, enabling the production of semiconductors, solar cells, and low-radiation coated glass.
Key Points Explained:
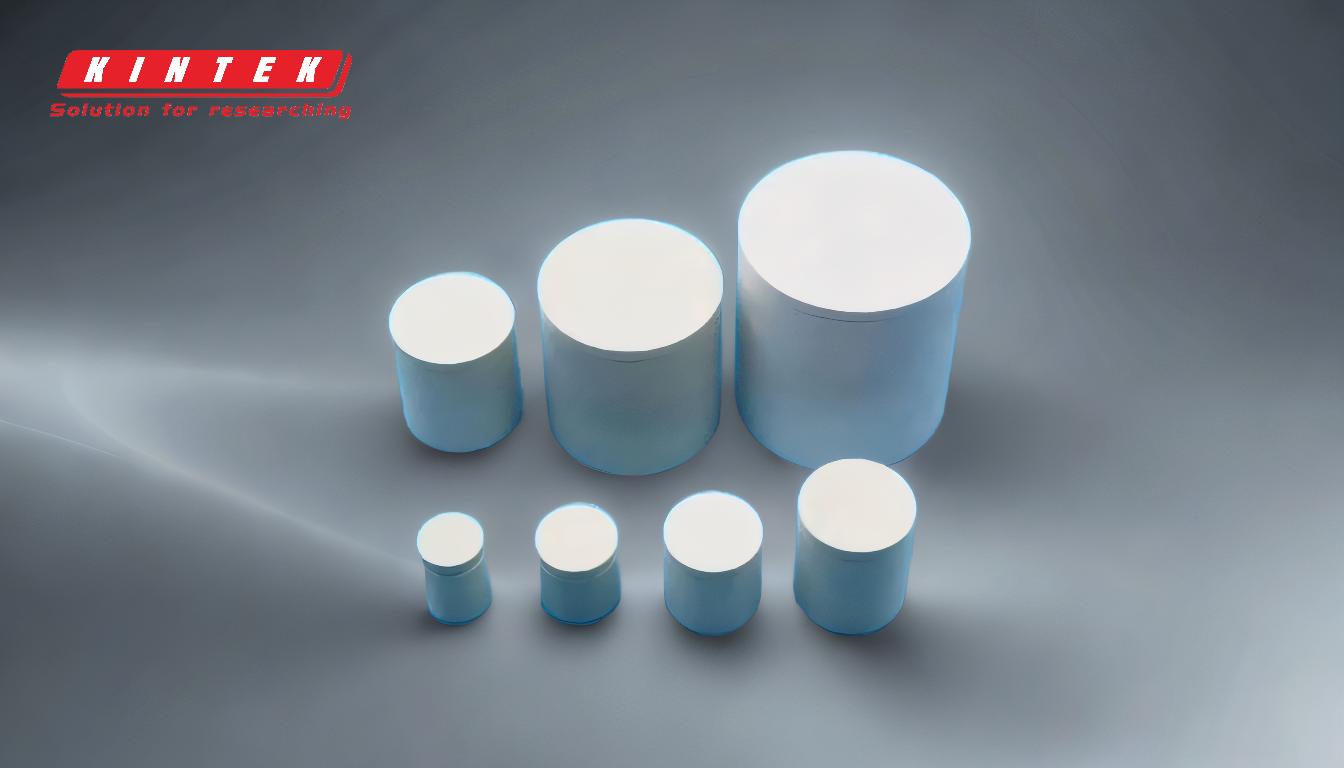
-
Manufacturers of Sputtering Targets
- American Elements: A prominent manufacturer of sputtering targets, producing them from advanced magnetic materials such as samarium cobalt and neodymium iron boron alloy.
- Other Manufacturers: While the references focus on American Elements, there are numerous other companies globally that specialize in producing sputtering targets. These manufacturers cater to industries like microelectronics, renewable energy, and decorative coatings.
-
Materials Used in Sputtering Targets
- Pure Metals: Common metals used include aluminum, copper, titanium, gold, silver, and chrome. These are chosen for their specific properties, such as conductivity, reflectivity, or durability.
- Alloys: Materials like samarium cobalt and neodymium iron boron are used for their advanced magnetic properties, making them suitable for specialized applications.
- Compounds: Oxides and nitrides are also used, particularly for applications requiring specific optical, electrical, or mechanical properties.
-
Applications of Sputtering Targets
- Semiconductors: Sputtering targets are crucial in the production of semiconductors, where thin films are deposited to create electronic components.
- Low-E Glass: Used in the production of low-radiation coated glass, which improves energy efficiency in buildings.
- Thin-Film Solar Cells: Sputtering targets enable the deposition of thin films in solar cells, contributing to renewable energy technologies.
- Decorative Coatings: They are also used to create decorative finishes on various surfaces, enhancing aesthetics and durability.
-
Importance of Material Selection
- The choice of material for sputtering targets is critical and depends on the desired properties of the thin film. For example:
- Conductivity: Metals like copper and silver are chosen for their excellent electrical conductivity.
- Reflectivity: Gold and aluminum are often used for their reflective properties.
- Durability: Titanium and chrome are selected for their strength and resistance to corrosion.
- The material must also align with the specific application, ensuring optimal performance in the final product.
- The choice of material for sputtering targets is critical and depends on the desired properties of the thin film. For example:
-
Manufacturing Process
- Sputtering targets are typically solid slabs, manufactured through processes like casting, rolling, or sintering, depending on the material and application.
- Advanced techniques are used to ensure uniformity, purity, and precise dimensions, which are critical for consistent thin-film deposition.
-
Industry Relevance
- Sputtering targets play a vital role in modern technology, enabling advancements in electronics, energy efficiency, and renewable energy.
- Their versatility and adaptability make them indispensable in industries that rely on thin-film deposition for innovation and product development.
In summary, sputtering targets are manufactured by specialized companies like American Elements, using a variety of materials tailored to specific applications. Their role in industries such as microelectronics, renewable energy, and decorative coatings highlights their importance in modern technology. The careful selection of materials and precise manufacturing processes ensure that these targets meet the demanding requirements of their applications.
Summary Table:
Key Aspect | Details |
---|---|
Manufacturers | American Elements, global specialized companies |
Materials | Pure metals (Al, Cu, Ti), alloys (SmCo, NdFeB), compounds (oxides, nitrides) |
Applications | Semiconductors, low-E glass, solar cells, decorative coatings |
Material Selection | Based on conductivity, reflectivity, durability, and application needs |
Manufacturing Process | Casting, rolling, sintering for uniformity and precision |
Industry Relevance | Critical for electronics, energy efficiency, and renewable energy |
Need high-quality sputtering targets for your applications? Contact us today to learn more!