Argon gas is widely used in sputtering processes due to its unique properties, which make it highly effective for thin film deposition. Its inert nature ensures that it does not react with the target material or the substrate, preserving the integrity of the deposited film. Additionally, argon's relatively high atomic mass allows it to efficiently transfer kinetic energy during collisions, enhancing the sputtering rate. While other rare gases like krypton and xenon can also be used, argon is preferred due to its balance of performance, availability, and cost-effectiveness. This makes it the go-to choice for sputtering applications across industries.
Key Points Explained:
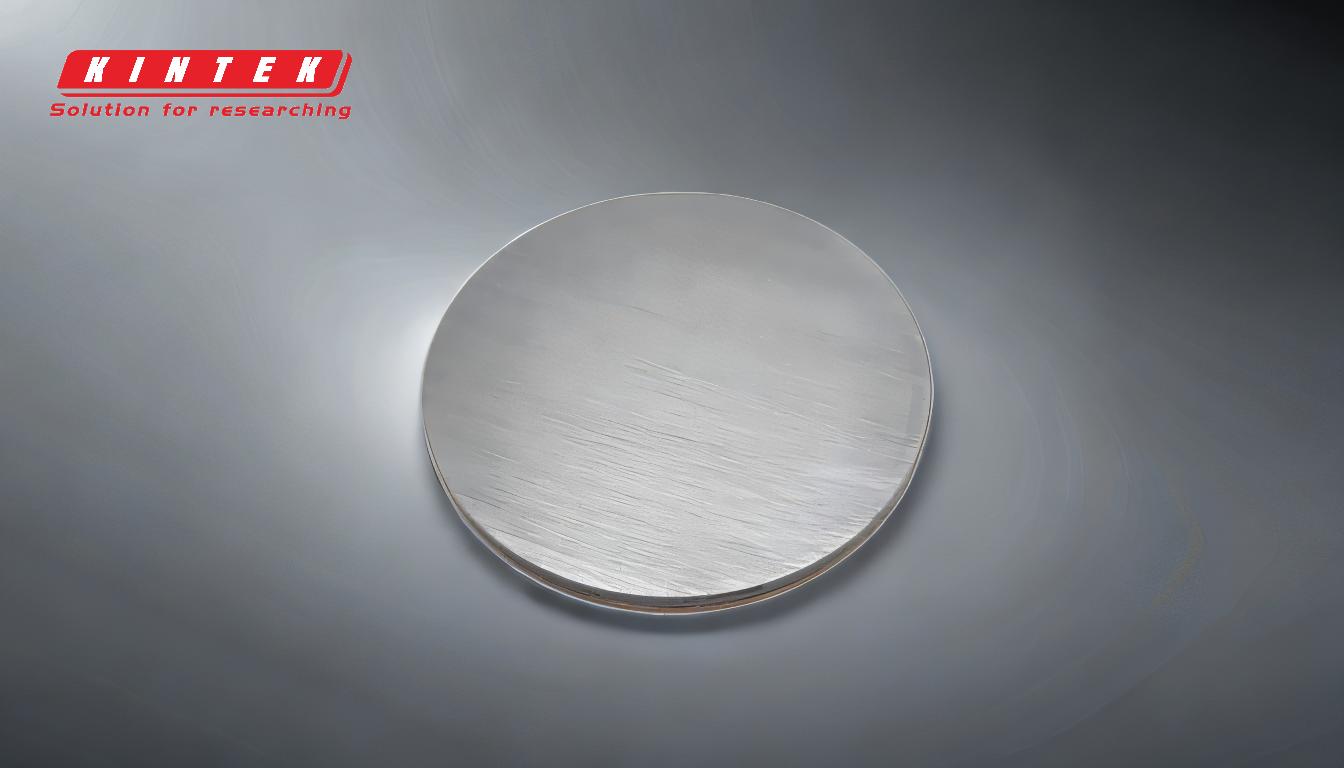
-
Inert Nature of Argon:
- Argon is chemically inert, meaning it does not react with the target material or the substrate during the sputtering process.
- This inertness ensures that the deposited film remains pure and uncontaminated, which is critical for applications requiring high-quality thin films, such as in semiconductor manufacturing or optical coatings.
- For example, in aerospace applications, argon is used to create a non-reactive atmosphere, preventing oxidation or other chemical reactions that could degrade the material.
-
High Sputtering Rate:
- Argon has a relatively high atomic mass (40 amu), which allows it to effectively transfer kinetic energy to the target material during high-energy collisions in the plasma.
- This energy transfer dislodges atoms from the target, enabling efficient sputtering and deposition of thin films.
- Compared to lighter gases like helium or neon, argon's higher mass results in a more effective sputtering process, making it a preferred choice.
-
Cost-Effectiveness and Availability:
- Argon is relatively inexpensive compared to other rare gases like krypton or xenon, which are also used in sputtering but are more costly.
- It is also widely available in high purity, making it easy to source for industrial applications.
- This combination of low cost and high availability makes argon a practical choice for large-scale sputtering operations.
-
Suitability for DC Sputtering:
- In DC sputtering, argon is particularly effective due to its ability to form a stable plasma and generate high-energy ions.
- The typical sputtering pressure range (0.5 mTorr to 100 mTorr) is well-suited for argon, ensuring efficient ion generation and target bombardment.
- The adjustable needle valve used to control argon flow in SEM sputter coaters further highlights its adaptability in maintaining precise gas pressure.
-
Comparison with Other Rare Gases:
- While krypton and xenon are occasionally used for specific applications (e.g., when higher sputtering rates or different energy transfer characteristics are needed), they are less common due to their higher cost and limited availability.
- Argon strikes a balance between performance and practicality, making it the standard choice for most sputtering processes.
-
Applications in Various Industries:
- Argon's properties make it suitable for a wide range of industries, including aerospace, electronics, and optics.
- For instance, in the aerospace industry, argon is used to create non-reactive environments, while in electronics, it is essential for depositing thin films in semiconductor devices.
- Its versatility and effectiveness ensure that it remains a cornerstone of sputtering technology.
By leveraging argon's inertness, high sputtering rate, cost-effectiveness, and adaptability, sputtering processes achieve high-quality thin film deposition efficiently and reliably.
Summary Table:
Property | Advantage |
---|---|
Inert Nature | Prevents reactions with target/substrate, ensuring pure thin film deposition. |
High Atomic Mass | Efficient energy transfer for enhanced sputtering rates. |
Cost-Effectiveness | Affordable and widely available compared to other rare gases. |
Suitability for DC Sputtering | Forms stable plasma, ideal for high-energy ion generation. |
Versatility | Used across industries like aerospace, electronics, and optics. |
Learn how argon gas can optimize your sputtering process—contact us today for expert advice!