RF sputtering is widely used for oxide film deposition due to its unique ability to handle insulating materials effectively, reduce charge buildup, and minimize arcing. Unlike DC sputtering, RF sputtering uses an alternating electric field, which prevents the accumulation of charges on insulating targets. This method also operates at lower pressures, enhancing deposition efficiency and film uniformity. Additionally, RF sputtering offers higher sputtering rates, better film quality, and the ability to deposit a wide range of materials, including insulators, metals, and composites. Recent advancements, such as RF diode sputtering, further improve coating uniformity and process stability, making RF sputtering a preferred choice for oxide film deposition.
Key Points Explained:
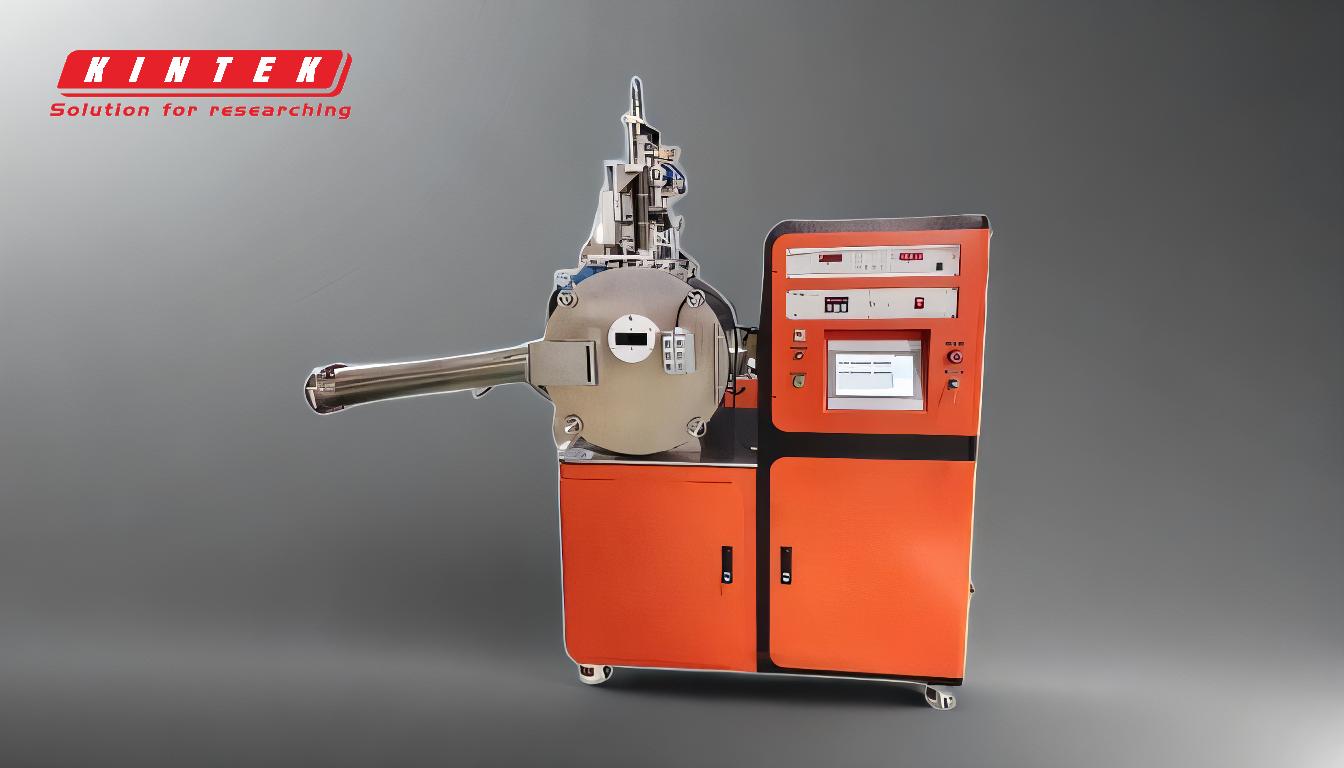
-
Handling Insulating Materials:
- RF sputtering is particularly effective for insulating targets, such as oxides (e.g., aluminum oxide, silicon dioxide). The alternating electric field in RF sputtering prevents charge buildup on the target surface, which is a common issue in DC sputtering. This allows for consistent and stable deposition of insulating films without arcing or target poisoning.
-
Reduction of Charge Buildup and Arcing:
- The alternating nature of the RF electric field ensures that the polarity of the target surface changes rapidly, neutralizing any accumulated charges. This reduces the likelihood of arcing, which can damage the film and the target. The absence of arcing leads to smoother and more uniform films.
-
Higher Sputtering Rates:
- RF sputtering achieves higher sputtering rates compared to DC sputtering, especially at the same chamber pressure. The oscillating electrons in the plasma increase the ionization of the sputtering gas, leading to more efficient deposition. This is particularly beneficial for producing thin films with precise control over thickness and microstructure.
-
Operation at Lower Pressures:
- RF sputtering can sustain plasma at lower pressures (1-15 mTorr), which reduces collisions between ionized gas particles and improves deposition efficiency. Lower pressure operation also minimizes contamination and enhances film purity, making it ideal for high-quality oxide film deposition.
-
Improved Film Quality and Uniformity:
- The process results in highly uniform films with excellent step coverage. RF sputtering avoids issues like "racetrack erosion" seen in DC sputtering, where uneven target erosion can lead to inconsistent film thickness. The uniform target erosion in RF sputtering ensures consistent film properties across the substrate.
-
Versatility in Material Deposition:
- RF sputtering can deposit a wide range of materials, including insulators, metals, alloys, and composites. This versatility makes it suitable for various applications, from semiconductor manufacturing to optical coatings.
-
Advancements in RF Diode Sputtering:
- Recent developments in RF diode sputtering have further enhanced the process. This technology eliminates the need for magnetic confinement, simplifies the setup, and improves coating uniformity. It also reduces arcing and target poisoning, making the process more stable and reliable.
-
Avoidance of Disappearing Anode Effect:
- Unlike DC sputtering, RF sputtering does not suffer from the disappearing anode effect, where the anode becomes coated and ineffective over time. This ensures continuous and stable operation, particularly important for long deposition runs.
-
Applications in Research and Industry:
- RF sputtering is widely used in both research and industrial settings due to its ability to deposit high-quality oxide films. It is particularly advantageous for producing highly insulating films, such as those used in microelectronics and optical coatings.
In summary, RF sputtering is favored for oxide film deposition because it overcomes the limitations of DC sputtering, such as charge buildup and arcing, while offering higher deposition rates, better film quality, and greater versatility. Its ability to handle insulating materials and operate at lower pressures makes it an ideal choice for producing high-performance oxide films.
Summary Table:
Key Advantage | Description |
---|---|
Handling Insulating Materials | Prevents charge buildup on insulating targets, ensuring stable deposition. |
Reduced Charge Buildup & Arcing | Alternating electric field neutralizes charges, minimizing arcing and damage. |
Higher Sputtering Rates | Achieves faster deposition rates compared to DC sputtering. |
Operation at Lower Pressures | Enhances deposition efficiency and film purity at 1-15 mTorr. |
Improved Film Quality | Produces highly uniform films with excellent step coverage. |
Versatility in Material Deposition | Deposits insulators, metals, alloys, and composites for diverse applications. |
Advancements in RF Diode Sputtering | Improves coating uniformity, stability, and reduces arcing. |
Avoids Disappearing Anode Effect | Ensures continuous operation without anode degradation. |
Applications in Research & Industry | Widely used for high-quality oxide films in microelectronics and optics. |
Unlock the benefits of RF sputtering for your oxide film projects—contact our experts today!