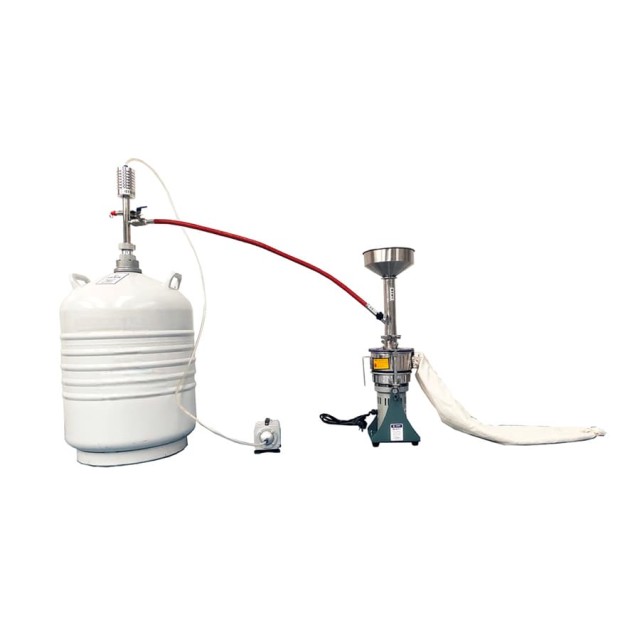
Crushing & Grinding Machine
Liquid Nitrogen Cryogenic Grinder Mill Cryomill Airflow Ultrafine Pulverizer
Item Number : KT-CG03
Price varies based on specs and customizations
- Power
- 1.8kw
- Voltage
- 220V
- Low-temperature crushing fineness
- 40-300 mesh
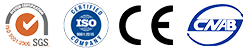
Shipping:
Contact us to get shipping details Enjoy On-time Dispatch Guarantee.
Why Choose Us
Reliable PartnerEasy ordering process, quality products, and dedicated support for your business success.
Product Application
The Liquid Nitrogen Cryogenic Grinding Machine(Cryomilling) Airflow Ultrafine Pulverizer is a specialized equipment designed for the pulverization of plastic raw materials, heat-sensitive materials, and toughness materials in laboratory settings. This machine is particularly effective in maintaining the original properties and state of the materials during the pulverization process. Its applications extend across various industries, including:
- Traditional Chinese Medicine: Ensuring the integrity and effectiveness of herbal samples.
- Western Medicine: Supporting the research and development of pharmaceutical formulations.
- Pesticides: Facilitating the fine grinding of pesticide compounds for better dispersion.
- Biology: Supporting research in genetic and cellular studies.
- Cosmetics: Ensuring the fineness of cosmetic ingredients for better texture and application.
- Food: Supporting the development of food additives and flavorings.
- Feed: Ensuring the uniformity and digestibility of feed materials.
- Chemicals: Supporting the fine grinding of chemical compounds for research and development.
- Ceramics: Facilitating the fine grinding of ceramic materials for better properties.
Detail & Parts
Product Feature
The Liquid Nitrogen Cryogenic Grinding Machine Airflow Ultrafine Pulverizer boasts several unique features that set it apart from traditional pulverizers:
- High Fineness: The machine can achieve pulverization fineness ranging from 40-300 mesh for low-temperature crushing and up to 300 mesh-1000 mesh for brittle materials at room temperature. This high fineness ensures that the materials retain their original properties and are suitable for detailed analysis and research.
- Small Size and Light Weight: Designed with a compact and lightweight structure, this pulverizer can be conveniently placed on laboratory countertops, making it highly accessible for users.
- Cryogenic Pulverization: Utilizing liquid nitrogen as a cooling medium, the machine can achieve ultra-low temperature pulverization, which is particularly beneficial for heat-sensitive and tough materials. This process ensures that the materials do not degrade or change their properties during pulverization.
- Safety and Ease of Use: The machine features a fully enclosed structure, reducing the risk of operator exposure to the pulverizing chamber. Additionally, its continuous feeding type design allows for easy operation with minimal supervision.
- Efficient Material Collection: The cyclone type material collection method ensures efficient and clean material collection, reducing waste and improving overall efficiency.
Working Principle
The Liquid Nitrogen Cryogenic Grinding Machine Airflow Ultrafine Pulverizer operates on a sophisticated principle that combines high-speed impact and airflow vortex pulverization. Here’s a detailed breakdown of its working mechanism:
- Liquid Nitrogen Cooling: The material to be pulverized is first cooled using liquid nitrogen, which reduces its temperature to as low as -196°C. This cooling process embrittles the material, making it easier to pulverize without causing thermal degradation.
- High-Speed Rotation: The cooled material enters the pulverizing chamber where it is subjected to high-speed rotation of blades (up to 25,000 r/min). The high-speed rotation creates a vortex of airflow that further aids in the pulverization process.
- Impact and Shearing: The material is subjected to repeated impact, collision, shearing, and friction between the blades, toothed disc, and other materials within the chamber. This multi-faceted action ensures thorough and efficient pulverization.
- Airflow Classification: The pulverized material is then classified by an airflow sieve classifier. Materials that meet the required fineness are collected, while those that do not are returned to the chamber for further pulverization.
- Closed-Circuit Circulation: The system operates in a closed-circuit circulation, ensuring that energy is fully utilized and energy consumption is minimized. This also helps in maintaining a consistent environment within the chamber, further enhancing the pulverization process.
Product Advantage
The Liquid Nitrogen Cryogenic Grinding Machine Airflow Ultrafine Pulverizer offers several advantages that make it a superior choice for laboratory and industrial applications:
- Increased Productivity: The optimized particle size and increased throughput ensure higher production rates, reducing overall production times and maximizing output.
- Elimination of Caking: The use of liquid nitrogen prevents the formation of caked product within the mill, ensuring a continuous and smooth pulverization process.
- Decreased Wear on Equipment: The ultra-low temperature pulverization reduces wear on grinding equipment, extending its operational life and reducing maintenance costs.
- Separation of Composite Materials: The machine is capable of separating composite materials within the mill, ensuring that each component is pulverized to the required fineness.
- Lower Energy Consumption: The closed-circuit circulation system and the use of liquid nitrogen as a grinding medium result in lower energy consumption, making the machine more cost-effective.
- Fine Particle Size: The machine can achieve pulverization fineness ranging from 10-700 mesh, or even micron-level fineness, ensuring that the materials are finely ground and suitable for detailed analysis.
- Uniform Particle Distribution: The cryogenic milling process generates ultra-fine particles within narrow distribution ranges, ensuring uniformity and consistency in the final product.
- Improved Pouring Properties: The finely ground materials improve the pouring properties, making them easier to handle and process in downstream applications.
- Reduction in Microbial Load: The low-temperature pulverization process also helps in reducing the microbial load, making the machine suitable for applications requiring sterile conditions.
In summary, the Liquid Nitrogen Cryogenic Grinding Machine Airflow Ultrafine Pulverizer is a versatile and efficient tool for the fine grinding of a wide range of materials. Its unique features and advantages make it an indispensable asset for laboratories and industries requiring precise and consistent pulverization.
Technical specifications
Parameter | Specification |
---|---|
Name | Laboratory cryogenic freezer pulverizer |
Model | KT-CG03 |
Power | 1.8kw |
Voltage | 220V |
Low-temperature crushing fineness | 40-300 mesh |
Output | 1-3kg/h |
Speed | 25000r/min |
Pulverizer weight | 10kg |
Overall dimensions | 480 * 290 * 280 |
Cooling | Liquid nitrogen freezing |
Knife Type | Multilateral warped head knife |
Crushing principle | High-speed impact |
Screening | Wind selection (no sieve) |
Fibrous materials crushed at room temperature fineness | 120 mesh-500 mesh |
Brittle materials crushed at room temperature fineness | 300 mesh-1000 mesh |
Note | Equipment plus liquid nitrogen use air humidity should not be greater than 50% RH |
FAQ
What Is A Cryogenic Grinder And How Does It Work?
What Is CVD (Chemical Vapor Deposition) And What Are Its Key Advantages?
What Are The Main Applications Of Cryogenic Grinders?
What Are Some Common Applications Of CVD Materials?
What Are The Advantages Of Using A Cryogenic Grinder?
What Types Of CVD Materials Are Available?
Why Is Liquid Nitrogen Used In Cryogenic Grinding?
How Does CVD Diamond Enhance The Performance Of Cutting Tools?
What Types Of Materials Can Be Processed Using A Cryogenic Grinder?
What Makes CVD Diamond Domes Suitable For High-performance Loudspeakers?
How Does Cryogenic Grinding Improve Material Properties?
How Does CVD Diamond Improve Thermal Management In Electronic Devices?
4.8
out of
5
Exceptional value for money. The machine's durability and technological advancements make it a must-have for our lab.
4.7
out of
5
Speedy delivery and top-notch quality. This pulverizer has significantly improved our research efficiency.
4.9
out of
5
Impressive technological advancement. The cryogenic grinding feature is a game-changer for our materials.
4.6
out of
5
Superb durability and ease of use. This machine has exceeded our expectations in every aspect.
4.8
out of
5
Outstanding performance and energy efficiency. The closed-circuit system is a brilliant innovation.
4.7
out of
5
Quick delivery and excellent value. The pulverizer's fine particle size control is unparalleled.
4.9
out of
5
Remarkable technological features. The cryogenic grinding process is precise and efficient.
4.8
out of
5
Durable and user-friendly. This machine has revolutionized our material processing capabilities.
Products
Liquid Nitrogen Cryogenic Grinder Mill Cryomill Airflow Ultrafine Pulverizer
REQUEST A QUOTE
Our professional team will reply to you within one business day. Please feel free to contact us!
Related Products
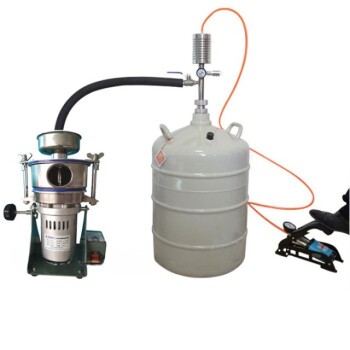
Small Cryogenic Grinder Cryomill Cryogrinder with Liquid Nitrogen for Laboratory Use
Our KINTEK Cryomilling is perfect for small runs and R&D trials. With a versatile cryogenic system, it can handle a variety of materials, including plastics, rubber, pharmaceuticals, and food grades. Plus, our specialized hydraulic laboratory crushers ensure accurate results through multiple passes, making it suitable for XRF analysis. Get finely-powdered samples with ease!
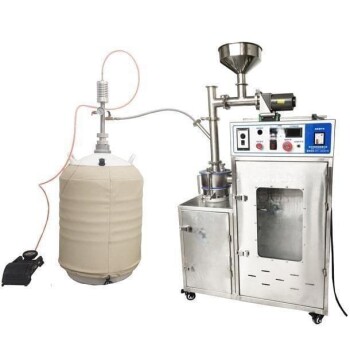
Liquid Nitrogen Cryogenic Grinder Mill Cryomill with Screw Feeder
Discover the Liquid Nitrogen Cryogenic Pulverizer with Screw Feeder, perfect for fine material processing. Ideal for plastics, rubber, and more. Boost your lab efficiency now!
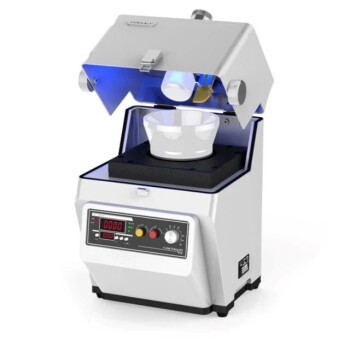
Laboratory Grinding Mill Mortar Grinder for Sample Preparation
KT-MG200 mortar grinder can be used for mixing and homogenizing powder, suspension, paste and even viscous samples. It can help users realize the ideal operation of sample preparation with more regularization and higher repeatability.
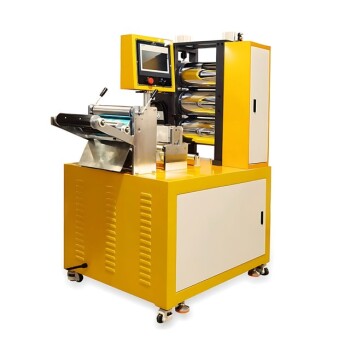
Small Lab Rubber Calendering Machine
Small lab rubber calendering machine is used for producing thin, continuous sheets of plastic or rubber materials. It is commonly employed in laboratories, small-scale production facilities, and prototyping environments to create films, coatings, and laminates with precise thickness and surface finish.
Related Articles
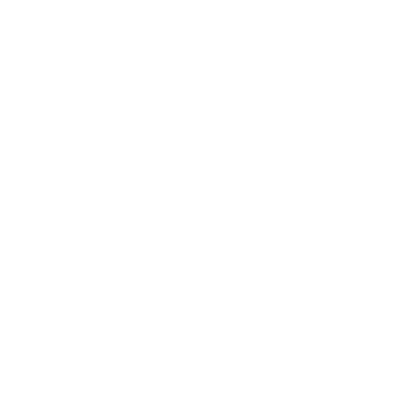
Cryogenic Pulverization Technology and Its Applications
Explores the process, advantages, disadvantages, and applications of cryogenic pulverization in various fields.
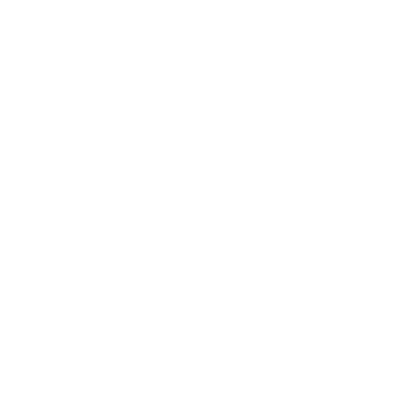
Application of Ultra-Micro Pulverization Technology in the Food Industry
Explores the benefits and applications of ultra-micro pulverization technology in enhancing food processing and nutrient absorption.
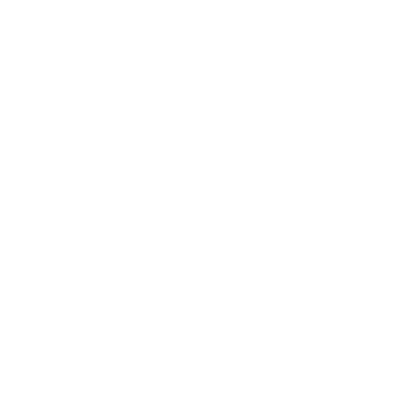
Development and Principles of Frozen Tissue Crushers
Explore the history, classification, and principles of frozen tissue crushers, including grinding ball selection and how to choose the right crusher.
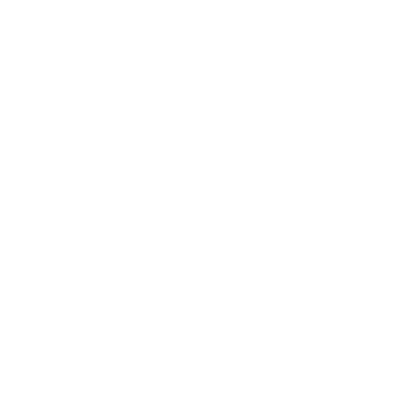
Application of Liquid Nitrogen in Food Freezing
Explores the use of liquid nitrogen in food freezing, its advantages, methods, equipment, and safety considerations.
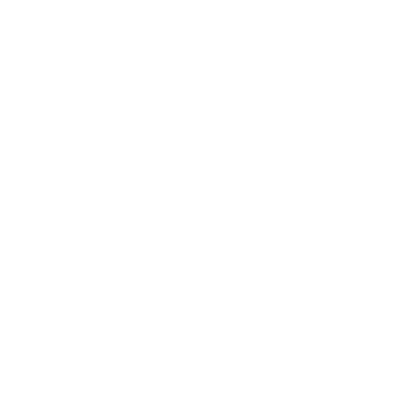
Understanding Cold Traps in Lyophilizers: Key Factors and Evaluation Methods
Explores the role, evaluation, and common misconceptions of cold traps in lyophilizers, emphasizing the importance of water capture efficiency.
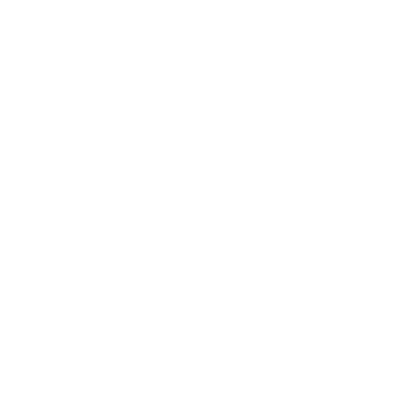
Exploring the World of Molecular Gastronomy
A deep dive into the innovative culinary techniques of molecular gastronomy, its history, and its impact on modern cuisine.
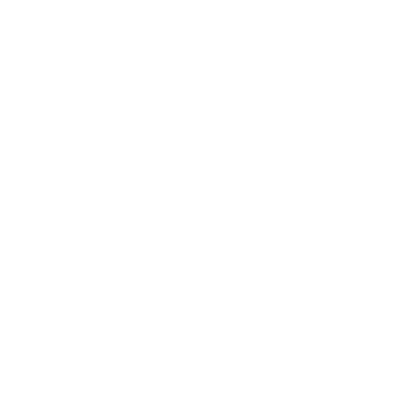
Exploring the World of Molecular Cuisine
Delve into the innovative techniques and surprising flavors of molecular cuisine.
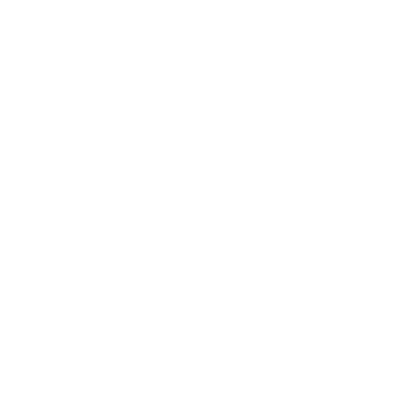
Why Ultra-Low Temps are Non-Negotiable: The Science Behind Preserving Critical Biological Materials
Discover why ultra-low temperature freezers (-86°C) are vital for preserving cells, proteins, and vaccines. Learn the science behind ULT storage best practices.
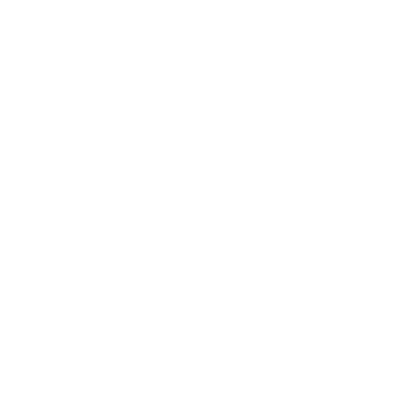
Preserving the Irreplaceable: How ULT Freezers Protect Critical Samples Across Industries
ULT freezers at -80°C protect biological samples, vaccines, and research materials from degradation, ensuring long-term viability across industries.
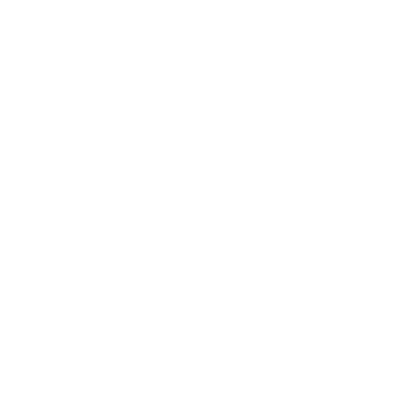
How ULT Freezers Protect Scientific Discoveries in Genetics and Drug Development
ULT freezers safeguard genetic and pharmaceutical research by maintaining -80°C storage for DNA, proteins, and cell lines—preventing sample degradation and ensuring research validity.