Sintering is a process that involves heating powdered materials to temperatures below their melting point, allowing particles to bond and form a solid structure. While sintering typically requires high temperatures—often greater than 0.6 times the material's melting temperature (Tm)—it is indeed possible to sinter aluminum, albeit with some challenges. Aluminum's relatively low melting point (660°C) and its tendency to form a stable oxide layer make sintering more complex compared to other metals. However, advancements in powder metallurgy and specialized techniques, such as vacuum or controlled atmosphere sintering, have made it feasible to sinter aluminum effectively.
Key Points Explained:
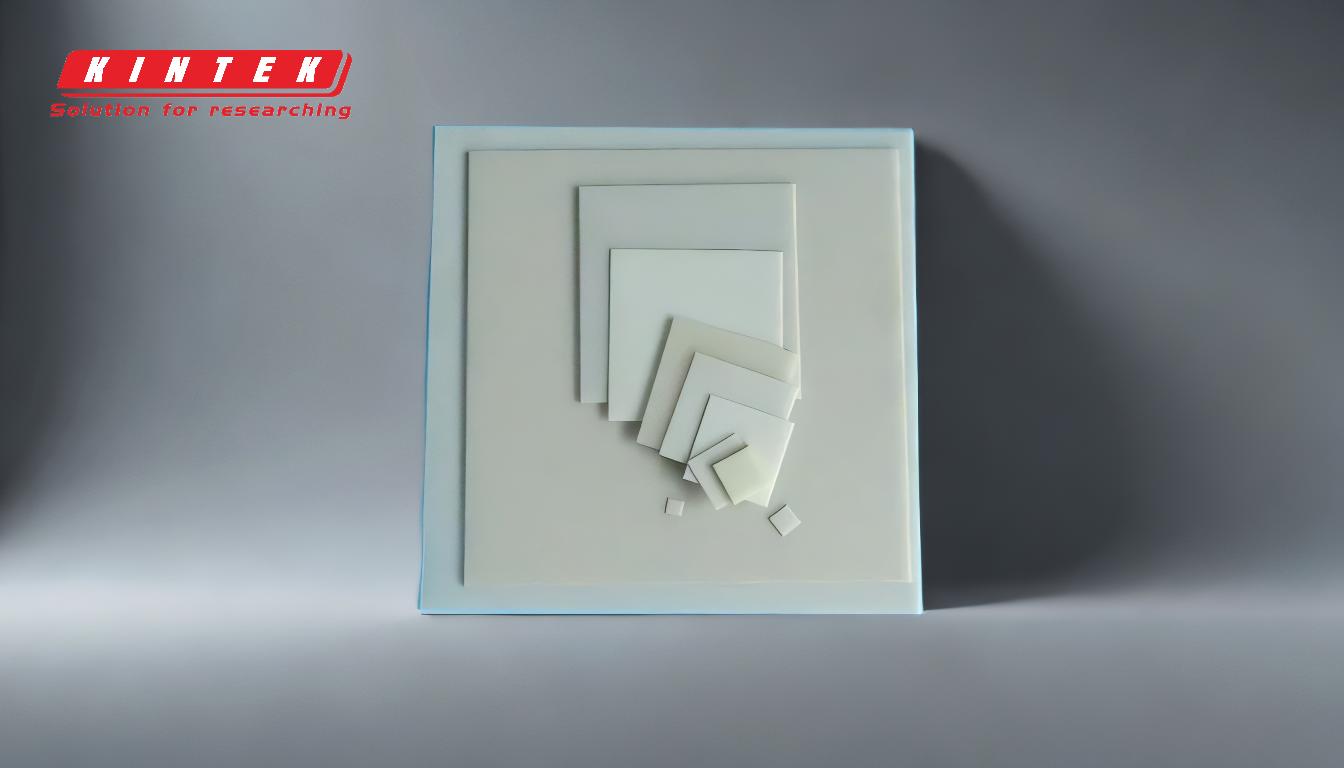
-
Sintering Basics:
- Sintering involves heating powdered materials to temperatures below their melting point to facilitate particle bonding.
- The process relies on diffusion mechanisms to reduce surface area and local curvature, leading to densification and consolidation of the powder.
-
Temperature Requirements:
- Sintering typically requires temperatures greater than 0.6 times the material's melting temperature (Tm).
- For aluminum, which has a melting point of 660°C, this translates to sintering temperatures above approximately 400°C.
-
Challenges with Aluminum Sintering:
- Oxide Layer Formation: Aluminum readily forms a stable oxide layer (Al₂O₃) on its surface, which can hinder particle bonding during sintering.
- Low Melting Point: Aluminum's relatively low melting point limits the temperature range available for sintering, making it more susceptible to deformation or melting if temperatures are not carefully controlled.
-
Overcoming Challenges:
- Controlled Atmosphere Sintering: Using inert or reducing atmospheres (e.g., nitrogen or hydrogen) can minimize oxide formation and improve sintering outcomes.
- Vacuum Sintering: Sintering in a vacuum environment helps prevent oxidation and enhances particle bonding.
- Additives and Alloys: Incorporating sintering aids or alloying elements can improve the sinterability of aluminum powders.
-
Applications of Sintered Aluminum:
- Sintered aluminum is used in lightweight structural components, heat exchangers, and automotive parts due to its high strength-to-weight ratio and thermal conductivity.
- The ability to produce complex shapes through powder metallurgy makes sintered aluminum attractive for various industries.
-
Advantages of Sintering Aluminum:
- Lightweight: Aluminum's low density makes it ideal for applications requiring lightweight materials.
- Cost-Effective: Powder metallurgy allows for near-net-shape manufacturing, reducing material waste and machining costs.
- Customizability: Sintering enables the production of parts with tailored properties by adjusting powder composition and processing parameters.
In summary, while sintering aluminum presents challenges due to its oxide layer and low melting point, specialized techniques and controlled environments make it a viable and valuable process for producing high-performance components.
Summary Table:
Aspect | Details |
---|---|
Sintering Basics | Heating powdered materials below melting point to bond particles. |
Temperature Required | >0.6 times melting point (Tm); >400°C for aluminum. |
Challenges | Oxide layer formation, low melting point. |
Solutions | Controlled atmosphere, vacuum sintering, additives, and alloys. |
Applications | Lightweight structural components, heat exchangers, automotive parts. |
Advantages | Lightweight, cost-effective, customizable properties. |
Unlock the potential of sintered aluminum for your projects—contact our experts today!