Controlling temperature in a reactor is a critical aspect of ensuring efficient and safe chemical processes. Temperature control methods vary depending on the reactor type, process requirements, and desired outcomes. Common approaches include regulating fuel flow, using proportional systems for fuel and air supply, and employing advanced techniques like pulse control systems. Additionally, heating and cooling methods such as oil baths, low-temperature solutions, and refrigerants are used to maintain precise temperatures. Stirring is often incorporated to enhance uniformity and efficiency. Below, we explore the key methods and considerations for temperature control in reactors.
Key Points Explained:
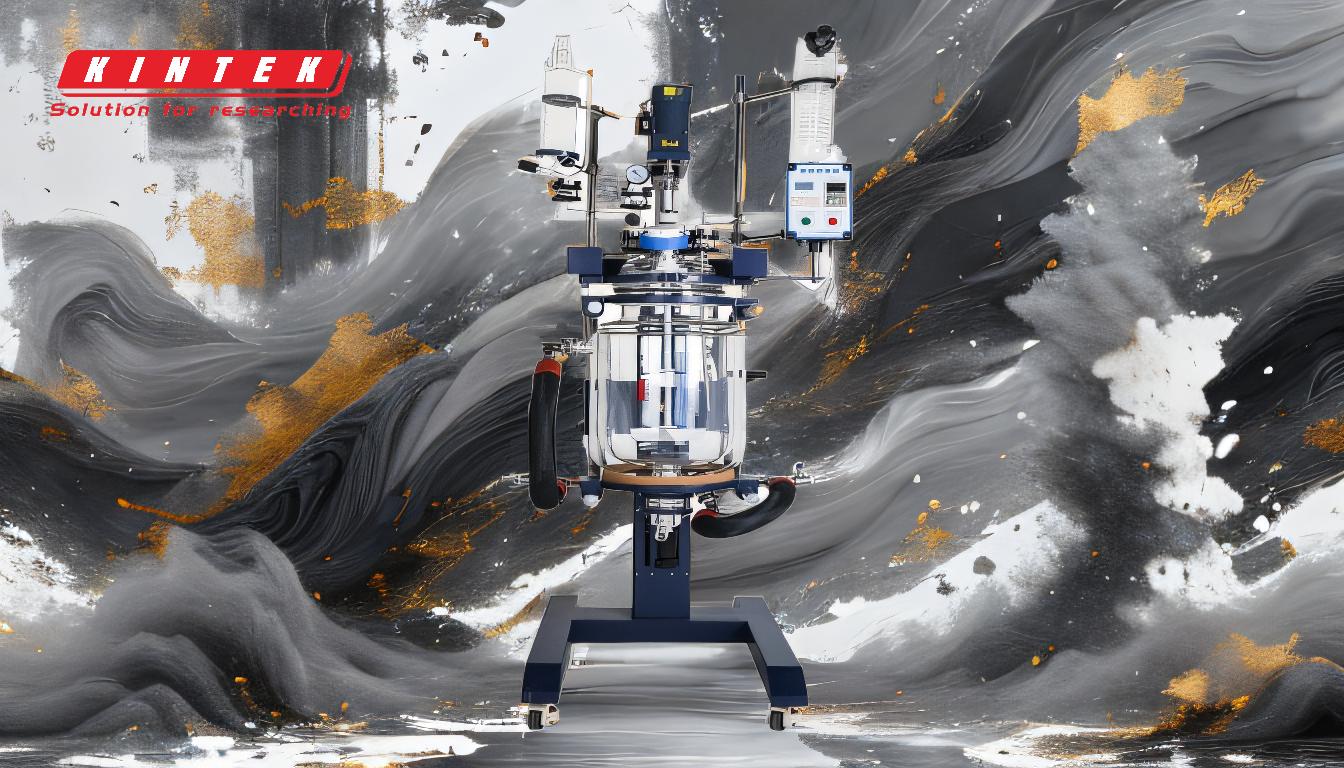
-
Fuel Flow Regulation
- Basic Systems: Simple and cost-effective, these systems regulate temperature by controlling the flow of fuel. However, they are less efficient and may lead to uneven temperature distribution.
- Applications: Suitable for processes where precise temperature control is not critical or where cost constraints are a priority.
- Limitations: Inefficient fuel usage and potential temperature fluctuations can affect process consistency.
-
Proportional Control Systems
- Dual Regulation: These systems control both fuel and air supply, maintaining an optimal ratio for combustion. This improves fuel efficiency and reduces operating costs.
- Benefits: Enhanced temperature stability, reduced emissions, and better process control.
- Applications: Ideal for processes requiring consistent and precise temperature management.
-
Pulse Control Systems
- High Flame Velocity: These systems maintain a fixed ratio of fuel and air, ensuring consistent temperatures throughout the process cycle.
- Advantages: High efficiency, uniform temperature distribution, and reduced energy consumption.
- Applications: Suitable for high-precision processes where temperature consistency is critical.
-
Heating Methods
- Oil Bath Reactors: Used to maintain a constant high temperature. The oil bath provides uniform heating and can handle a wide range of temperatures.
- Low-Temperature Heat Solutions: Ideal for processes requiring moderate heating. These solutions are energy-efficient and cost-effective.
-
Cooling Methods
- Refrigerants: Used to lower temperatures in reactors, especially for exothermic reactions or processes requiring low temperatures.
- Stirring: Enhances heat transfer and ensures uniform temperature distribution throughout the reactor.
-
Stirring for Temperature Uniformity
- Purpose: Stirring facilitates heat transfer and prevents localized hot or cold spots.
- Methods: Mechanical stirrers, magnetic stirrers, or impellers can be used depending on the reactor design.
- Benefits: Improved process efficiency, reduced reaction times, and better product quality.
-
Advanced Temperature Control Technologies
- Automated Systems: Modern reactors often incorporate automated temperature control systems with sensors and feedback loops for real-time adjustments.
- Integration with Process Control: These systems can be integrated with broader process control networks for seamless operation.
By combining these methods, reactor temperature can be precisely controlled to meet the specific requirements of various chemical processes. The choice of method depends on factors such as process complexity, energy efficiency goals, and the desired level of precision.
Summary Table:
Method | Description | Applications |
---|---|---|
Fuel Flow Regulation | Controls fuel flow; cost-effective but less efficient. | Suitable for non-critical processes or cost-sensitive applications. |
Proportional Control Systems | Regulates fuel and air supply for better efficiency and stability. | Ideal for processes requiring consistent and precise temperature management. |
Pulse Control Systems | Maintains fixed fuel-air ratio for uniform temperature distribution. | Best for high-precision processes with critical temperature consistency needs. |
Heating Methods | Includes oil baths and low-temperature solutions for uniform heating. | Used for processes requiring moderate to high temperatures. |
Cooling Methods | Utilizes refrigerants and stirring to lower and maintain low temperatures. | Essential for exothermic reactions or low-temperature processes. |
Stirring | Enhances heat transfer and prevents temperature inconsistencies. | Improves process efficiency and product quality. |
Advanced Technologies | Automated systems with sensors and feedback loops for real-time adjustments. | Integrated into modern reactors for seamless and precise temperature control. |
Need expert advice on reactor temperature control? Contact us today to optimize your chemical processes!