A fluidized bed reactor (FBR) is a versatile and efficient system used in various industrial processes, such as chemical reactions, combustion, and material processing. It operates by suspending solid particles in a fluid-like state using a flowing gas or liquid, enabling uniform mixing, temperature control, and continuous operation. While FBRs offer significant advantages like uniform particle mixing, consistent temperature gradients, and continuous production capabilities, they also come with challenges, such as higher energy costs due to increased fluid velocities and pressure drops. Understanding how an FBR works involves examining its operational principles, benefits, and limitations.
Key Points Explained:
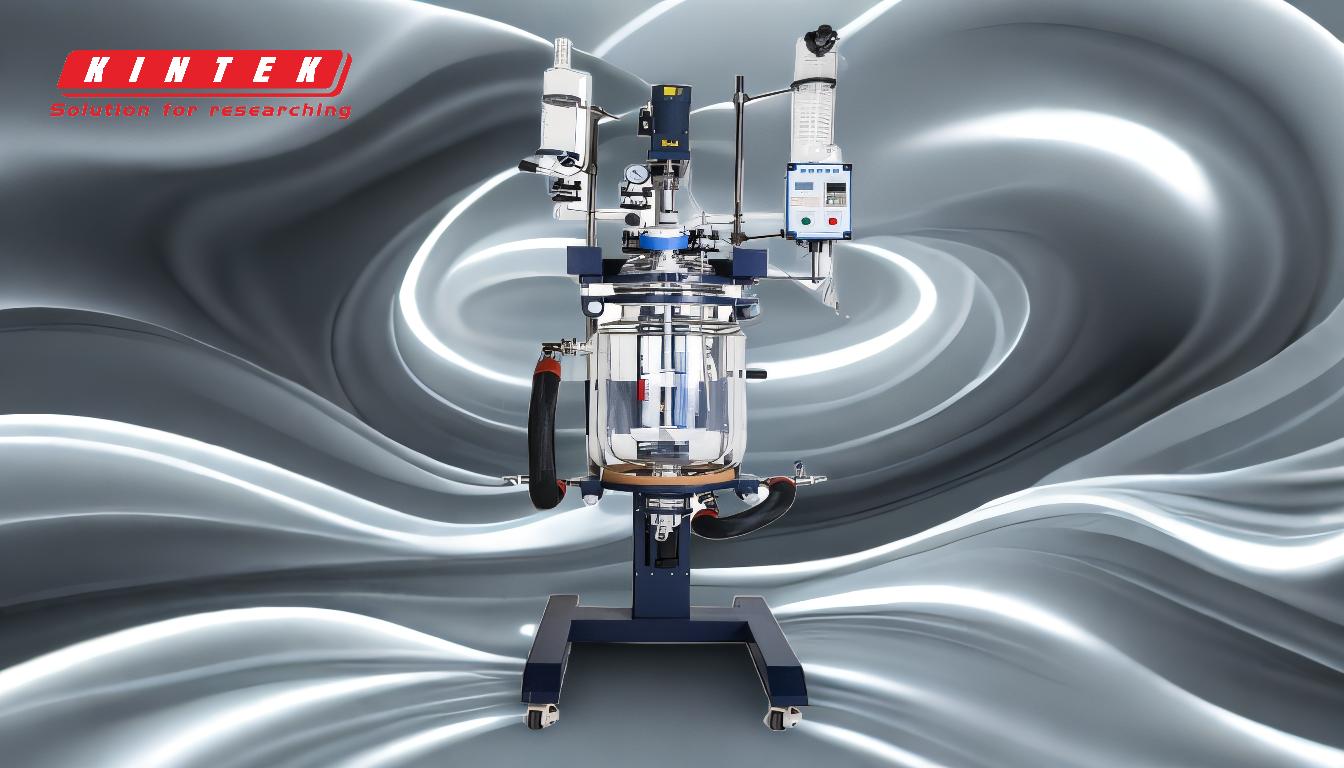
-
Operational Principle of a Fluidized Bed Reactor:
- A fluidized bed reactor suspends solid particles (often catalysts or reactants) in a fluid-like state by passing a gas or liquid through them at high velocities.
- The fluid velocity is adjusted to exceed the minimum fluidization velocity, where the upward drag force balances the weight of the particles, causing them to behave like a fluid.
- This fluidization allows for excellent mixing of particles, ensuring uniform contact between reactants and catalysts, which enhances reaction efficiency.
-
Advantages of Fluidized Bed Reactors:
- Uniform Particle Mixing: The fluid-like state of the particles ensures thorough mixing, eliminating poor mixing and resulting in a consistent product quality. This is particularly beneficial in processes requiring homogeneous reactions.
- Uniform Temperature Gradients: The high heat transfer rates in FBRs prevent localized hot or cold spots, which can degrade products or cause uneven reactions. This feature is crucial for temperature-sensitive processes.
- Continuous Operation: FBRs can operate continuously, allowing for the steady withdrawal of products and the introduction of new reactants. This makes them highly efficient for large-scale industrial applications.
-
Challenges of Fluidized Bed Reactors:
- Higher Fluid Velocities: To maintain the fluidized state, higher fluid velocities are required, which increases pumping power and energy costs. This can make FBRs less energy-efficient compared to other reactor types.
- Pressure Drop in Deep Beds: In reactors with deep beds of particles, the pressure drop across the bed can be significant, further increasing the need for additional pumping power and energy consumption.
-
Applications of Fluidized Bed Reactors:
- FBRs are widely used in industries such as petrochemicals, pharmaceuticals, and energy production. For example, they are employed in catalytic cracking of petroleum, combustion of coal, and production of polymers.
- Their ability to handle large volumes of materials and provide uniform conditions makes them ideal for processes requiring scalability and consistency.
-
Design Considerations:
- The design of an FBR must account for factors like particle size, fluid velocity, and bed depth to optimize performance and minimize energy consumption.
- Advanced control systems are often integrated to monitor and adjust parameters such as temperature, pressure, and flow rates in real-time, ensuring efficient and stable operation.
In summary, fluidized bed reactors are highly effective systems that leverage fluid dynamics to achieve uniform mixing, temperature control, and continuous operation. While they offer significant advantages in terms of product quality and process efficiency, their energy requirements and operational complexities must be carefully managed. Understanding these principles and trade-offs is essential for optimizing their use in industrial applications.
Summary Table:
Aspect | Details |
---|---|
Operational Principle | Suspends solid particles in a fluid-like state using gas or liquid flow. |
Advantages | Uniform mixing, consistent temperature, and continuous operation. |
Challenges | Higher energy costs due to fluid velocities and pressure drops. |
Applications | Petrochemicals, pharmaceuticals, energy production, and material processing. |
Discover how a fluidized bed reactor can optimize your industrial processes—contact our experts today!