The cost of a pyrolysis system varies significantly depending on its scale, technology, and application. Small-scale systems for research or small businesses can cost anywhere from $20,000 to $100,000, while large-scale industrial systems can range from $500,000 to several million dollars. Factors influencing the cost include the type of feedstock, system capacity, automation level, and additional features like emission control systems. Understanding these variables is crucial for making an informed purchasing decision.
Key Points Explained:
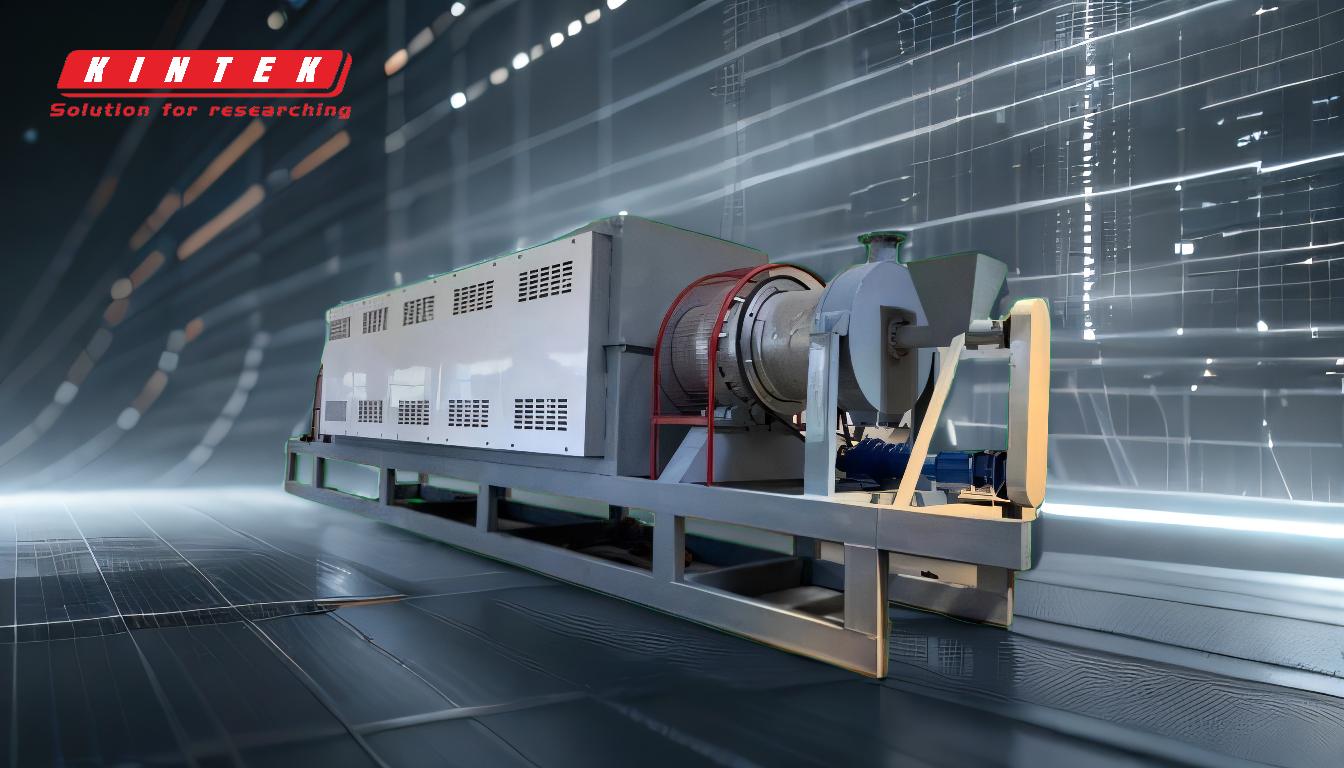
-
Scale and Capacity:
- Small-scale systems: These are typically used for research, pilot projects, or small businesses. They are less expensive, with costs ranging from $20,000 to $100,000. These systems are ideal for processing limited amounts of feedstock, such as agricultural waste or small-scale plastic recycling.
- Large-scale systems: Designed for industrial applications, these systems can process large volumes of feedstock, such as municipal solid waste or industrial by-products. Costs for these systems range from $500,000 to several million dollars, depending on capacity and complexity.
-
Technology and Design:
- Batch vs. Continuous systems: Batch systems are generally less expensive but require manual loading and unloading, making them less efficient. Continuous systems, which automate the feeding and discharge processes, are more costly but offer higher throughput and efficiency.
- Advanced features: Systems with advanced features like real-time monitoring, automated controls, and integrated emission control systems will cost more. These features enhance operational efficiency and ensure compliance with environmental regulations.
-
Feedstock Type:
- The type of feedstock being processed significantly impacts the system's design and cost. For example, systems designed for plastic waste may require additional preprocessing equipment like shredders, which increases the overall cost. Similarly, systems handling biomass may need drying units to reduce moisture content before pyrolysis.
-
Emission Control and Environmental Compliance:
- Modern pyrolysis systems must comply with stringent environmental regulations, necessitating the inclusion of emission control systems. These systems, which may include scrubbers, filters, and condensers, add to the overall cost but are essential for minimizing environmental impact and ensuring regulatory compliance.
-
Installation and Operational Costs:
- Installation: The cost of installing a pyrolysis system can vary based on site preparation, utility connections, and local labor rates. Large-scale systems may require significant infrastructure upgrades, adding to the initial investment.
- Operational costs: These include energy consumption, maintenance, labor, and feedstock procurement. While operational costs are ongoing, they should be factored into the total cost of ownership to ensure the system's long-term viability.
-
Return on Investment (ROI):
- The potential ROI from a pyrolysis system depends on the end products (e.g., bio-oil, syngas, char) and their market value. For example, systems producing high-quality bio-oil for fuel or chemical production may offer quicker returns compared to those producing char for soil amendment. Understanding the market demand and pricing for these products is crucial for assessing the system's economic feasibility.
-
Customization and Vendor Support:
- Customized systems tailored to specific feedstock and operational needs will generally cost more than off-the-shelf models. However, customization can optimize performance and yield, potentially improving ROI. Additionally, vendor support, including training, maintenance services, and warranties, can add to the upfront cost but provide long-term benefits.
-
Market Trends and Innovations:
- The pyrolysis market is evolving, with new technologies and innovations continually emerging. Staying informed about the latest advancements can help identify cost-effective solutions and avoid investing in outdated technology. For instance, modular pyrolysis systems are gaining popularity due to their scalability and lower initial investment requirements.
In conclusion, the cost of a pyrolysis system is influenced by multiple factors, including scale, technology, feedstock type, and environmental compliance. Potential buyers should conduct a thorough cost-benefit analysis, considering both upfront and operational expenses, to determine the most suitable system for their needs. For more detailed information on pyrolysis reactor, you can explore further resources.
Summary Table:
Factor | Description | Cost Impact |
---|---|---|
Scale and Capacity | Small-scale: $20K-$100K; Large-scale: $500K-$millions | Higher capacity = higher cost |
Technology and Design | Batch vs. continuous systems; Advanced features (e.g., automation, monitoring) | Continuous systems & advanced features = higher cost |
Feedstock Type | Plastic, biomass, etc.; Preprocessing equipment (e.g., shredders, drying units) | Complex feedstock = higher cost |
Emission Control | Scrubbers, filters, condensers for environmental compliance | Emission control systems = higher cost |
Installation & Operation | Site prep, labor, energy, maintenance | Large-scale systems = higher installation costs; ongoing operational expenses |
ROI | Market value of end products (e.g., bio-oil, syngas, char) | High-quality products = faster ROI |
Customization | Tailored systems for specific needs | Customization = higher upfront cost but optimized performance |
Ready to find the perfect pyrolysis system for your needs? Contact our experts today for a customized solution!