The frequency of servicing a vacuum pump depends on its type, usage, and operating conditions. Regular maintenance is essential to ensure optimal performance, prevent breakdowns, and extend the pump's lifespan. Key maintenance tasks include fluid changes, seal and vane replacements, oil level checks, and monitoring for abnormal noises or vibrations. For oil-sealed pumps, oil changes are typically required every three months, while dry pumps may need tip-seal and bearing replacements. Scroll pumps, though low-maintenance, require frequent spiral seal replacements. Always follow the manufacturer's guidelines and conduct routine inspections to address issues early.
Key Points Explained:
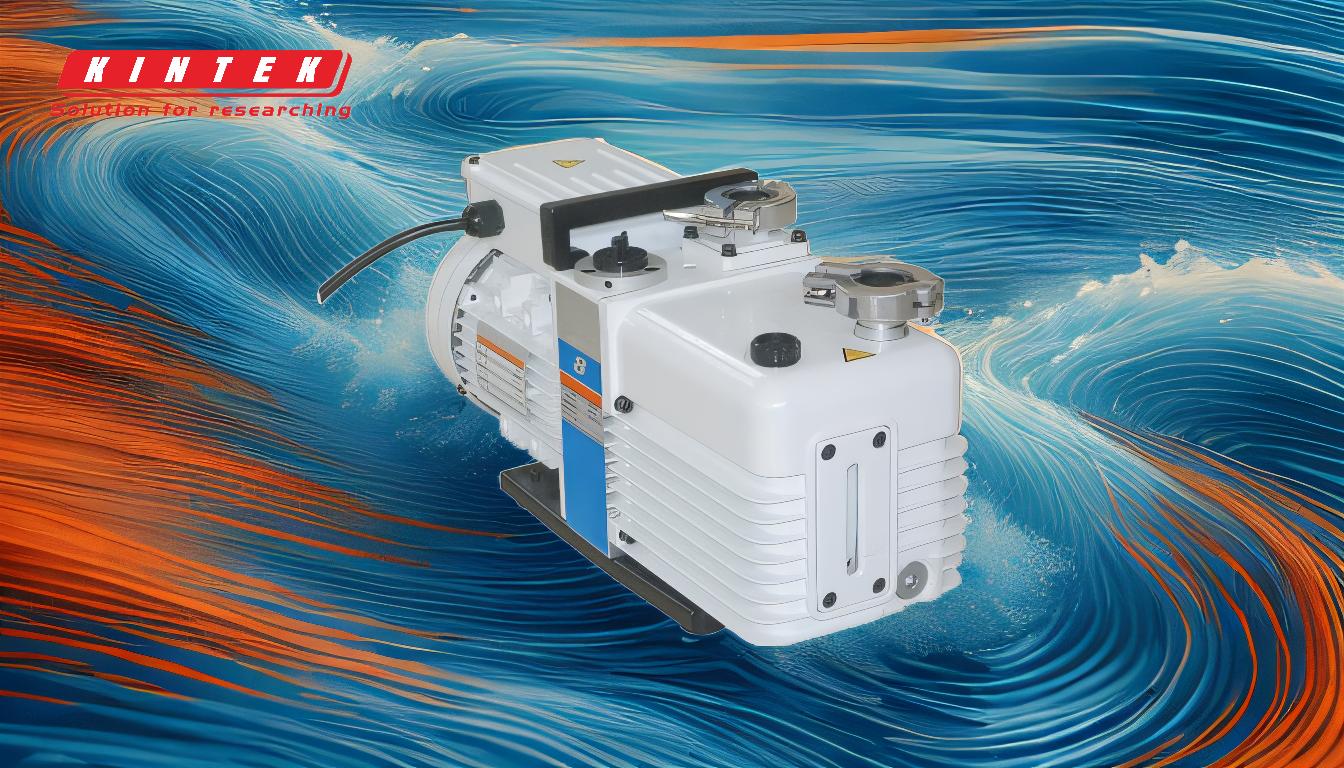
-
Type of Vacuum Pump Determines Maintenance Frequency
- Different types of vacuum pumps have varying maintenance requirements. For example:
- Oil-sealed vane pumps: Require fluid changes every three months (e.g., model HFV-100) and vane and seal replacements to prevent contamination and wear.
- Dry-roughing pumps (e.g., dry scroll pumps): Need tip-seal and bearing replacements to avoid major damage and extend lifespan.
- Scroll pumps: Require frequent spiral seal replacements to maintain airtightness but are generally low-maintenance due to fewer moving parts and no oil requirements.
- Turbo pumps (high-vacuum pumps): Require regular bearing replacements at specific intervals to prevent catastrophic rotor failure.
- Different types of vacuum pumps have varying maintenance requirements. For example:
-
Oil Maintenance for Oil-Sealed Pumps
- Regularly monitor the oil level and condition through the pump oil window.
- Change the oil every three months or when it turns a dark tea color, indicating contamination.
- Ensure the oil level is within the standard window position; adjust by draining excess oil if necessary.
- Use original manufacturer-recommended oil mist filters for optimal performance.
-
Seal and Vane Replacements
- Seals and vanes are critical components that degrade over time due to wear and contamination.
- Replace spiral seals in scroll pumps frequently to prevent leaks caused by debris and particle erosion.
- For oil-sealed pumps, replace vanes and seals during routine maintenance to ensure efficient operation.
-
Temperature and Pressure Monitoring
- Monitor the pump body temperature to ensure it does not exceed 45°C, as overheating can cause wear in the pump chamber and cylinder, affecting vacuum performance.
- Check cooling water temperature before and during operation to prevent overheating.
- Avoid blocking the pump discharge outlet to prevent back pressure, which reduces efficiency and can cause internal damage.
-
Routine Inspections and Checks
- Perform regular inspections for oil leaks, abnormal noises, and vibrations.
- Check mounting bolts for tightness and tighten vibration couplings if necessary.
- Inspect and clean filters in the cooling water pressure reducer and purge gas pressure reducer.
- Verify water flow rates as specified in the manual and inspect water hoses for damage.
- Ensure all guards are installed before running the pump.
-
Operational Best Practices
- Allow the pump to run for 30 minutes before connecting it to your application to ensure proper warm-up.
- Use a cold inlet trap and gas ballast when working with condensable vapors to prevent contamination.
- Consider using an inline oil filter for oil pumps to maintain oil quality.
- After use, allow the pump to keep running to purge solvents and prevent residue buildup.
- Avoid using orange tubing, which may degrade and contaminate the system.
- Always empty the inlet and outlet catch pots to maintain cleanliness.
-
Documentation and Record-Keeping
- Always read the manufacturer’s manual for specific maintenance guidelines and intervals.
- Record oil type, condition, and changes to track maintenance history.
- Document any faults, alarms, or temperature readings from the Frequency Converter (if applicable).
- Maintain a clean operating environment and visually inspect the pump area regularly.
By following these guidelines, you can ensure your vacuum pump operates efficiently, reduces downtime, and achieves its maximum lifespan. Regular servicing tailored to the pump type and usage is key to maintaining performance and avoiding costly repairs.
Summary Table:
Vacuum Pump Type | Key Maintenance Tasks | Frequency |
---|---|---|
Oil-Sealed Vane Pumps | Fluid changes, vane and seal replacements | Every 3 months |
Dry-Roughing Pumps | Tip-seal and bearing replacements | As per manufacturer guidelines |
Scroll Pumps | Spiral seal replacements | Frequent, as needed |
Turbo Pumps | Bearing replacements | Specific intervals to prevent failure |
Ensure your vacuum pump operates at peak efficiency—contact our experts today for tailored maintenance advice!