Sputter coating thickness typically ranges from angstroms to microns, depending on the specific application and process parameters. The thickness is influenced by factors such as sputtering time, power applied to the target, material properties, and process conditions like vacuum pressure and target-to-sample distance. Coatings can be single-layered or multi-layered, with materials chosen based on their conductivity, grain size, and secondary electron emission properties. The process is highly customizable, allowing for precise control over the thickness and quality of the deposited film.
Key Points Explained:
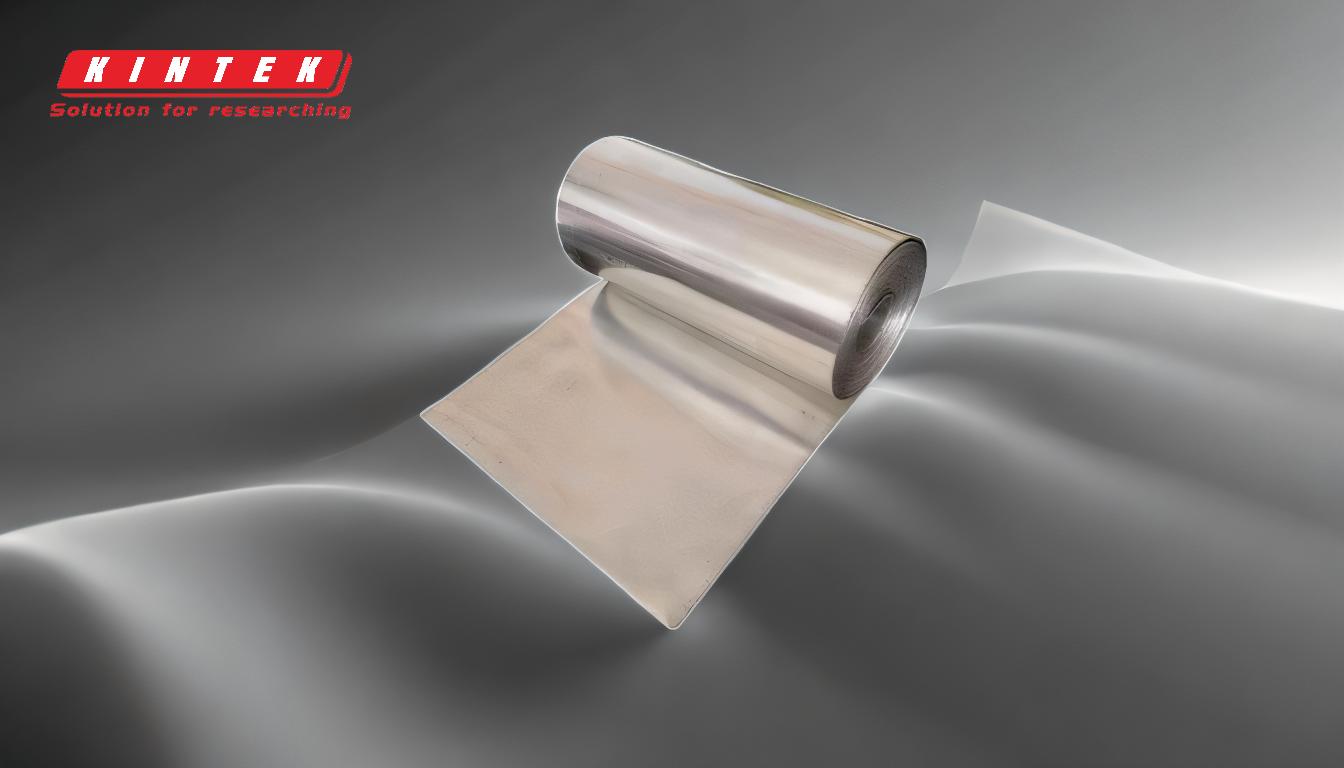
-
Typical Thickness Range:
- Sputter coatings generally range from angstroms (Å) to microns (µm).
- Angstroms (Å): 1 Å = 0.1 nanometers (nm). This range is used for ultra-thin coatings, often in applications requiring high precision, such as semiconductor manufacturing or nanotechnology.
- Microns (µm): 1 µm = 1000 nm. This range is used for thicker coatings, such as in protective layers or optical coatings.
-
Factors Influencing Thickness:
- Sputtering Time: The longer the sputtering process, the thicker the coating. This is a direct relationship, as more material is deposited over time.
- Power Applied to the Target: Higher power levels increase the energy of the sputtered particles, leading to a higher deposition rate and potentially thicker coatings.
- Material Properties: The mass and energy level of the coating particles affect how they deposit on the substrate. Heavier materials or higher-energy particles may deposit more material per unit time.
-
Process Conditions:
- Vacuum Pressure: Lower pressure in the sample chamber can lead to a more controlled and uniform deposition.
- Target-to-Sample Distance: A shorter distance can increase the deposition rate, while a longer distance may lead to more uniform coatings.
- Sputter Gas: The type of gas used (e.g., argon) can influence the energy and direction of the sputtered particles.
-
Single vs. Multi-Layered Coatings:
- Single Material Coatings: These are straightforward, with a uniform layer of one material. The thickness is controlled by the sputtering parameters.
- Multi-Layered Coatings: These involve alternating layers of different materials. Each layer can have a different thickness, depending on the desired properties (e.g., conductivity, reflectivity, or durability). The total thickness is the sum of the individual layers.
-
Material Selection:
- Materials like Gold/Palladium (Au/Pd), Platinum (Pt), and Silver (Ag) are commonly used due to their specific properties:
- Conductivity: Essential for applications like electron microscopy, where the coating needs to conduct electricity to prevent charging.
- Grain Size: Smaller grain sizes can lead to smoother coatings, which are important for high-resolution imaging.
- Secondary Electron Emission: This property is crucial for enhancing the signal in techniques like scanning electron microscopy (SEM).
- Materials like Gold/Palladium (Au/Pd), Platinum (Pt), and Silver (Ag) are commonly used due to their specific properties:
-
Key Parameters Affecting the Sputter Coating Process:
- Sputter Current and Voltage: These control the energy and rate of particle emission from the target.
- Pressure in the Sample Chamber: A high vacuum is typically required to minimize contamination and control the deposition environment.
- Target Thickness and Material: The target's properties influence the sputtering rate and the quality of the deposited film.
- Sample Material: The substrate material can affect how well the coating adheres and its final properties.
-
Applications and Customization:
- Precision Applications: In fields like semiconductor manufacturing, coatings may need to be extremely thin (angstroms) and uniform.
- Protective Coatings: For applications requiring durability, thicker coatings (microns) may be used.
- Optical Coatings: These often involve multi-layered structures to achieve specific reflectance or transmittance properties.
In summary, the thickness of sputter coatings is highly variable and depends on a range of factors, including process parameters, material properties, and the specific application. The ability to control these factors allows for the creation of coatings that meet precise requirements, whether for ultra-thin layers in nanotechnology or thicker, more durable coatings in industrial applications.
Summary Table:
Aspect | Details |
---|---|
Thickness Range | Angstroms (Å) to microns (µm) |
Key Influencing Factors | Sputtering time, power, material properties, vacuum pressure, and distance |
Coating Types | Single-layered or multi-layered |
Common Materials | Gold/Palladium, Platinum, Silver |
Applications | Semiconductor manufacturing, protective layers, optical coatings |
Need precise sputter coatings for your application? Contact our experts today to get started!