When deciding between an oil-sealed vacuum pump and a dry vacuum pump, the choice largely depends on the specific application, budget, and operational priorities. Dry vacuum pumps are increasingly favored due to their low maintenance, environmental benefits, and lack of contamination risks. However, oil-sealed pumps remain a reliable and cost-effective option for certain applications, particularly where deeper vacuums are required. Below, we explore the key differences, advantages, and considerations to help determine which type of pump is better suited for your needs.
Key Points Explained:
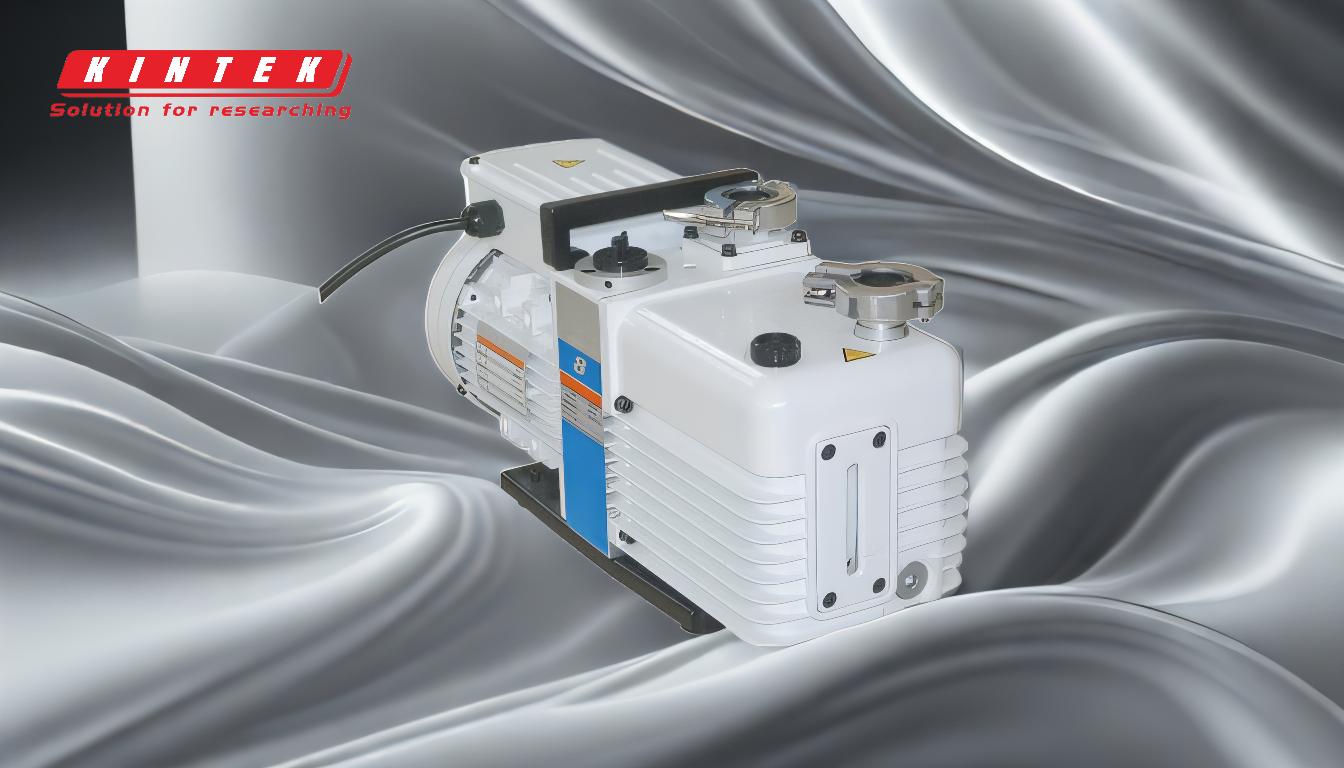
-
Contamination Risks
- Dry Pumps: Do not use oil, eliminating the risk of oil contamination in the process gases or surrounding environment. This is critical in sensitive applications such as semiconductor manufacturing, food processing, or laboratories where purity is essential.
- Oil-Sealed Pumps: Use oil as a sealing and cooling medium, which can lead to contamination if oil escapes into the gas stream or environment. This requires additional measures to manage oil disposal and prevent contamination.
-
Maintenance and Operational Costs
- Dry Pumps: Require minimal maintenance due to the absence of oil. There is no need for oil changes, disposal of contaminated oil, or frequent servicing. This reduces long-term operational costs and downtime.
- Oil-Sealed Pumps: Require regular oil changes and maintenance to ensure optimal performance. The cost of oil replacement and disposal, along with potential contamination cleanup, adds to the total cost of ownership.
-
Noise Levels
- Dry Pumps: Operate more quietly, making them suitable for environments where noise reduction is important, such as laboratories or offices.
- Oil-Sealed Pumps: Tend to be noisier due to the mechanical operation of the oil-sealed system.
-
Service Intervals
- Dry Pumps: Have longer service intervals because they do not rely on oil, which degrades over time. This results in fewer disruptions and lower maintenance costs.
- Oil-Sealed Pumps: Require more frequent servicing to replace oil and maintain performance, leading to higher maintenance demands.
-
Vacuum Performance
- Dry Pumps: Typically provide sufficient vacuum levels for most general applications but may not achieve the same depth of vacuum as oil-sealed pumps.
- Oil-Sealed Pumps: Offer deeper vacuum levels, making them suitable for applications requiring high vacuum performance, such as certain industrial or scientific processes.
-
Environmental Impact
- Dry Pumps: Are more environmentally friendly as they eliminate the need for oil, reducing the risk of oil spills, contamination, and the disposal of hazardous waste.
- Oil-Sealed Pumps: Pose environmental challenges due to oil usage, which requires proper handling, disposal, and potential cleanup in case of leaks.
-
Initial Cost and Reliability
- Dry Pumps: Often have a higher upfront cost but offer long-term savings through reduced maintenance and operational expenses. They are highly efficient and reliable for most applications.
- Oil-Sealed Pumps: Are generally more affordable initially and are well-established, proven technologies. However, their long-term costs can be higher due to maintenance and oil-related expenses.
-
Application Suitability
- Dry Pumps: Ideal for applications where contamination, noise, and maintenance are critical concerns. They are widely used in laboratories, food processing, and cleanroom environments.
- Oil-Sealed Pumps: Better suited for applications requiring deeper vacuum levels and where the additional maintenance and contamination risks are manageable.
Conclusion:
The decision between an oil-sealed vacuum pump and a dry vacuum pump depends on your specific requirements. Dry pumps are generally better for applications prioritizing cleanliness, low maintenance, and environmental considerations. Oil-sealed pumps, while more traditional, remain a cost-effective and reliable option for applications requiring deeper vacuum levels. Carefully evaluate your operational needs, budget, and long-term goals to make the best choice.
Summary Table:
Feature | Dry Vacuum Pump | Oil-Sealed Vacuum Pump |
---|---|---|
Contamination Risk | No oil, no contamination risks | Risk of oil contamination |
Maintenance | Minimal, no oil changes required | Regular oil changes and maintenance |
Noise Levels | Quieter operation | Noisier due to mechanical operation |
Service Intervals | Longer intervals, less downtime | Frequent servicing required |
Vacuum Performance | Sufficient for most applications | Deeper vacuum levels |
Environmental Impact | Eco-friendly, no oil disposal needed | Requires oil handling and disposal |
Initial Cost | Higher upfront cost | More affordable initially |
Application Suitability | Ideal for clean, low-noise environments | Best for deeper vacuum requirements |
Still unsure which vacuum pump is right for you? Contact our experts today for personalized advice!