In sputtering, the target is indeed the cathode. This is because the target is connected to a negative potential (cathode) in the sputtering system, while the substrate acts as the positive electrode (anode). When a high voltage is applied, the inert gas (typically argon) in the chamber is ionized, creating a plasma. The positively charged argon ions are accelerated toward the negatively charged target (cathode), bombarding it and ejecting atoms from the target surface. These ejected atoms then deposit onto the substrate, forming a thin film. This process is fundamental to both magnetron sputtering and DC sputtering, where the target's role as the cathode is critical for the deposition of materials.
Key Points Explained:
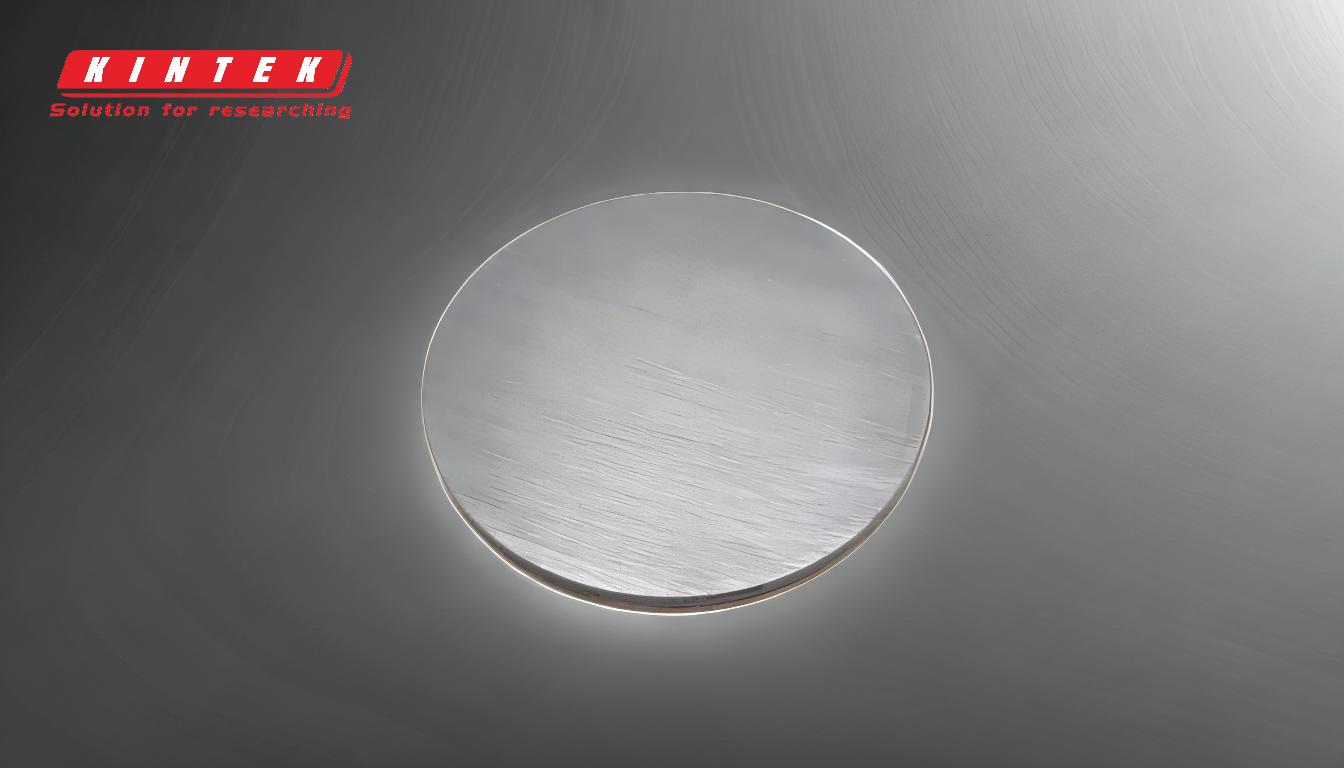
-
Target as the Cathode:
- In sputtering, the target is connected to a negative potential, making it the cathode in the system.
- The substrate, on the other hand, acts as the positive electrode (anode).
- This setup creates an electric field that accelerates positively charged ions toward the target.
-
Role of Inert Gas:
- An inert gas, typically argon, is introduced into the vacuum chamber.
- The gas is ionized by the high voltage applied between the target (cathode) and the substrate (anode), creating a plasma.
- The plasma consists of positively charged argon ions and free electrons.
-
Sputtering Mechanism:
- The positively charged argon ions are accelerated toward the negatively charged target (cathode).
- When these high-energy ions strike the target, they eject atoms from the target's surface through a process called sputtering.
- The ejected atoms then travel through the vacuum chamber and deposit onto the substrate, forming a thin film.
-
Magnetron Sputtering:
- In magnetron sputtering, a magnetron is placed near the target to enhance the sputtering process.
- The magnetic field confines the plasma near the target surface, increasing the ionization of the inert gas and improving the sputtering efficiency.
- This results in a higher deposition rate and better film quality.
-
DC Sputtering:
- In DC sputtering, a direct current (DC) field is used to generate the plasma.
- The target (cathode) is at a negative potential of several hundred volts, while the substrate acts as the positive electrode.
- This method is particularly effective for metallic targets but less so for non-conductive materials, which can become positively charged and repel the argon ions.
-
Target Material and Shape:
- The target is a solid piece of the material to be deposited, such as gold or other metals.
- It is typically flat or cylindrical in shape and must be large enough to avoid unintended sputtering of other components, such as metallic bearings.
- The target surface is always larger than the actual sputtered area, and used-up targets often display deeper grooves or "race tracks" where sputtering has been predominant.
-
Applications in Semiconductor Manufacturing:
- Sputtering targets are widely used in semiconductor manufacturing to deposit thin films of metallic alloys onto substrates.
- The targets must ensure chemical purity and metallurgical uniformity to meet the stringent requirements of semiconductor production.
In summary, the target in sputtering is indeed the cathode, playing a crucial role in the deposition process by providing the material that is ejected and deposited onto the substrate. The interaction between the target (cathode), the substrate (anode), and the plasma created by the inert gas is fundamental to the sputtering process, enabling the creation of high-quality thin films for various applications, including semiconductor manufacturing.
Summary Table:
Key Aspect | Details |
---|---|
Target as Cathode | Connected to negative potential, attracting argon ions for sputtering. |
Role of Inert Gas | Argon is ionized to create plasma, essential for the sputtering process. |
Sputtering Mechanism | Argon ions bombard the target, ejecting atoms that deposit on the substrate. |
Magnetron Sputtering | Magnetic field enhances plasma confinement, improving deposition efficiency. |
DC Sputtering | Direct current generates plasma, ideal for metallic targets. |
Target Material & Shape | Typically flat or cylindrical, made of materials like gold or other metals. |
Applications | Widely used in semiconductor manufacturing for high-quality thin films. |
Discover how sputtering targets can optimize your thin film processes—contact our experts today!