Fixed-bed reactors are widely used in chemical and industrial processes due to their ability to provide precise control over reaction parameters such as temperature and residence time. This design is particularly advantageous for processes like pyrolysis, where maintaining consistent conditions is critical for optimizing product quality and yield. Unlike fluidized-bed reactors, which excel in continuous operation and uniform mixing, fixed-bed reactors offer simplicity, ease of operation, and scalability, making them suitable for a variety of applications, including biomass conversion and chemical synthesis.
Key Points Explained:
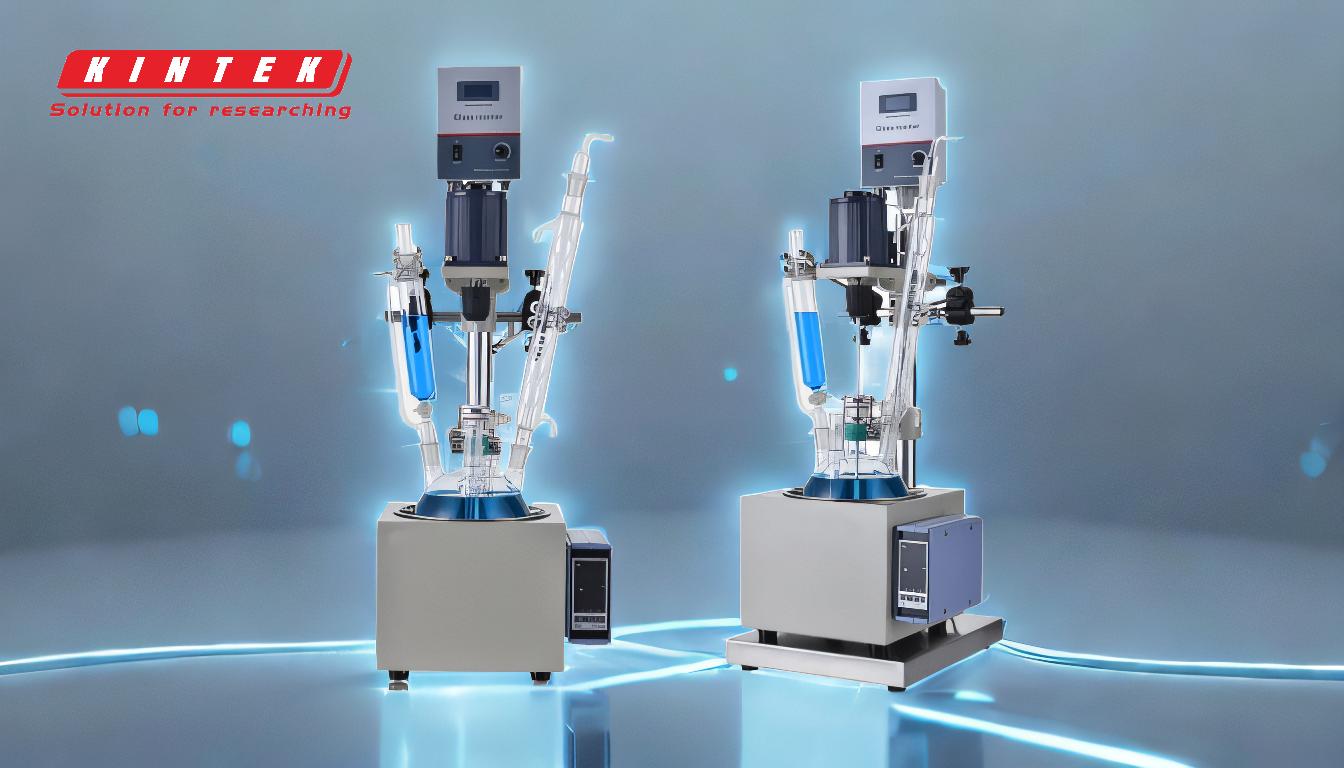
-
Better Control of Reaction Parameters
- Fixed-bed reactors allow for precise control of critical parameters such as temperature and residence time.
- This is particularly important in processes like pyrolysis, where consistent conditions are necessary to ensure optimal product quality and yield.
- The ability to maintain stable conditions reduces the risk of unwanted side reactions or incomplete conversions.
-
Simplicity and Ease of Operation
- Fixed-bed reactors have a straightforward design, making them easier to construct, operate, and maintain compared to more complex systems like fluidized-bed reactors.
- This simplicity reduces operational costs and minimizes the need for specialized training or equipment.
-
Scalability
- Fixed-bed reactors are highly scalable, making them suitable for both small-scale laboratory experiments and large-scale industrial applications.
- The design can be adapted to accommodate varying feedstock volumes and processing requirements without significant modifications.
-
Suitability for Particulate Substrates
- While fluidized-bed reactors are often preferred for particulate substrates like woody biomass, fixed-bed reactors can also handle such materials effectively, especially when precise control over reaction conditions is required.
- This makes them versatile for applications in biomass conversion, chemical synthesis, and other industries.
-
Reduced Risk of Hot or Cold Spots
- Although fluidized-bed reactors are known for their uniform temperature gradients, fixed-bed reactors can also achieve consistent temperature distribution with proper design and operation.
- This reduces the risk of localized hot or cold spots, which can negatively impact reaction efficiency and product quality.
-
Lower Energy Consumption
- Fixed-bed reactors typically require less energy to operate compared to fluidized-bed reactors, which rely on fluidization to maintain particle mixing and temperature uniformity.
- This makes fixed-bed reactors more energy-efficient, particularly for processes that do not require continuous operation.
-
Flexibility in Process Design
- Fixed-bed reactors can be designed to accommodate a wide range of catalysts and reaction conditions, allowing for greater flexibility in process optimization.
- This adaptability makes them suitable for diverse applications, from biomass pyrolysis to catalytic cracking in the petroleum industry.
-
Lower Capital and Maintenance Costs
- The simpler design of fixed-bed reactors translates to lower capital costs and reduced maintenance requirements.
- This makes them an attractive option for industries looking to minimize upfront investments and operational expenses.
-
Improved Product Recovery
- The stationary nature of the bed in fixed-bed reactors facilitates easier separation and recovery of products, particularly in processes involving solid catalysts or feedstocks.
- This can lead to higher overall process efficiency and reduced waste generation.
-
Compatibility with Batch and Continuous Processes
- Fixed-bed reactors can be operated in both batch and continuous modes, providing flexibility depending on the specific requirements of the process.
- This versatility makes them suitable for a wide range of industrial applications, from small-scale research to large-scale production.
In summary, fixed-bed reactors offer a combination of simplicity, precise control, scalability, and cost-effectiveness, making them a preferred choice for many chemical and industrial processes. Their ability to handle diverse feedstocks and reaction conditions further enhances their utility across various applications.
Summary Table:
Advantage | Description |
---|---|
Precise Control | Enables accurate management of temperature and residence time for optimal results. |
Simplicity | Easy to construct, operate, and maintain, reducing operational costs. |
Scalability | Suitable for both small-scale labs and large-scale industrial applications. |
Energy Efficiency | Lower energy consumption compared to fluidized-bed reactors. |
Flexibility | Adaptable to various catalysts and reaction conditions. |
Cost-Effectiveness | Lower capital and maintenance costs. |
Improved Product Recovery | Easier separation and recovery of products. |
Ready to optimize your chemical processes with fixed-bed reactors? Contact our experts today to learn more!